When choosing the correct welding rod size, understanding fractions and their implications is paramount for ensuring successful welds. Among the frequently debated sizes are the 1/8 inch and the 3/32 inch rods. Is 1/8 truly bigger than 3/32? Let’s delve into the details, exploring from an experienced welder's perspective and backed by welding expertise.
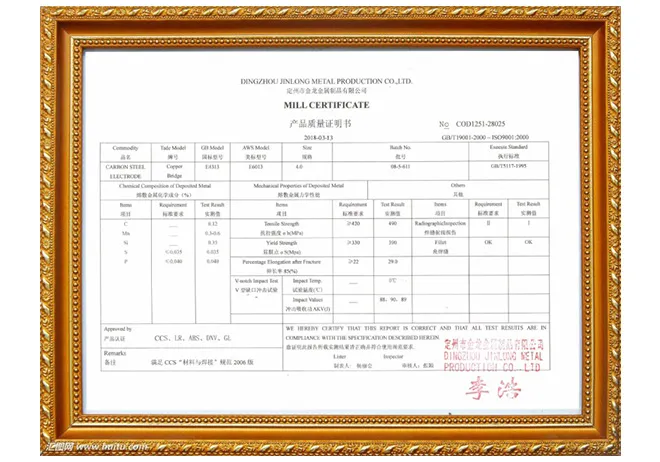
To start, comparing 1/8 and 3/32 inches requires basic fraction knowledge. Expressed over a common denominator, 1/8 is equal to 4/32, confirming that 1/8 inch is indeed larger than 3/32 inch. This size difference, small though it may seem, can significantly influence the welding process, affecting heat input, joint strength, and material compatibility.
In the world of welding, rod size matters immensely. Larger rods like the 1/8 inch are typically used in heavier applications, often involving thicker materials. They permit greater current flow, producing deeper penetration and stronger seams. With a larger diameter wire, the welder can fill gaps more readily and cover wider joints swiftly. This is particularly advantageous in industrial settings where robust welds are critical.
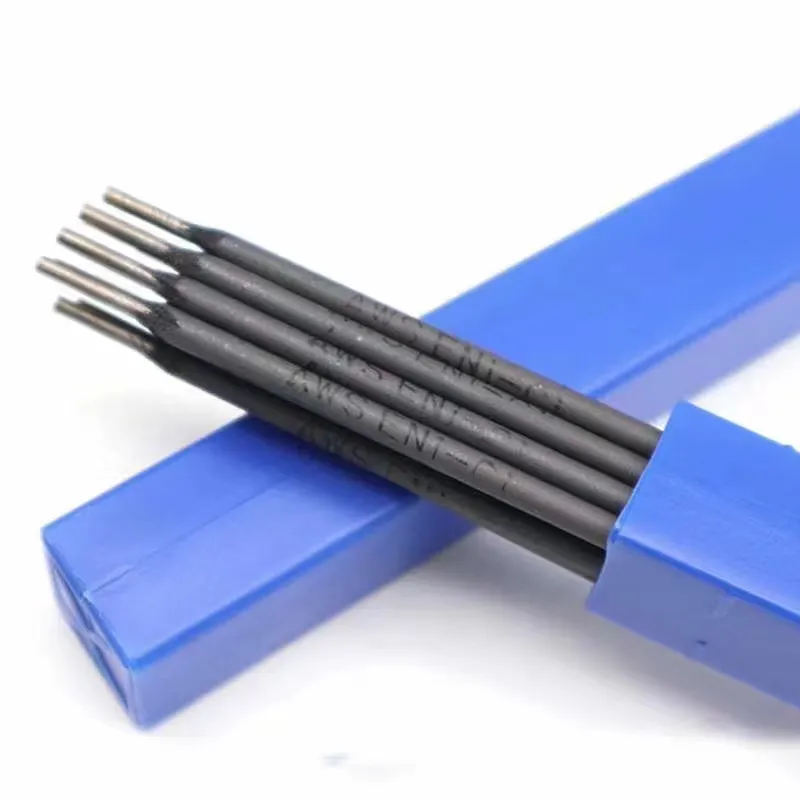
In contrast, a 3/32 inch rod suits more delicate applications. It is better for welding thinner metals or for tasks that require intricate detail and finesse. This smaller rod requires less amperage, reducing the risk of burning through thin materials. When the welding work involves precise, small-scale repairs or when working with delicate metals like certain stainless steels, a 3/32 inch rod provides the control and precision that larger rods cannot.
Drawing from vast experience, professional welders know the significance of matching rod size with project needs. The choice between 1/8 and 3/32 inch rods can affect not just the integrity of a weld but also its safety and effectiveness. Larger 1/8 inch rods require higher currents and can generate more heat, potentially distorting thinner materials if not handled with skill. Meanwhile, smaller 3/32 inch rods offer ease in handling and versatility, particularly in tight or awkward spaces; however, they may fall short in strength where heavier welds are necessary.
is 1/8 bigger than 3/32 welding rod
Through authoritative training and hands-on expertise, welders also understand the influence of rod size on productivity. Larger rods decrease the number of passes needed to complete a weld, thus saving time during extensive projects. Nonetheless, smaller rods afford greater maneuverability, allowing for complex weld geometries. The expert eye evaluates these trade-offs, ensuring the chosen rod accommodates both the material and the welder's proficiency.
Furthermore, the welding process itself dictates rod choice. For instance, in stick welding (SMAW), where conditions often include outdoor or windy environments, a 1/8 inch rod might offer a stable arc and better deposition rate. Conversely, for TIG welding processes demanding precision, a welder might favor a smaller diameter like the 3/32 inch to achieve a fine, controlled welde line without overwhelming the workpiece.
The importance of welding rod size cannot be understated, and the decision should stem from a foundation of knowledge, sanctioned by authoritative guides like the American Welding Society (AWS) and trusted welding manuals. When selecting the appropriate size, consider material thickness, welding position, and desired penetration. Welding professionals rely on well-documented standards and personal experience to make informed decisions.
In conclusion,
understanding whether 1/8 is bigger than 3/32 is just the beginning. The implications of this size differentiation can drastically alter the landscape of a welding project. Welding experts, with years of experience and trustworthiness in the field, continuously refine their techniques, drawing from an authoritative knowledge base to ensure that every weld is not just a mechanical bond, but a blend of art and science that lasts through the ages. So, when it comes to choosing between 1/8 and 3/32 inch rods, remember that size is indeed significant—but it’s how you apply it that truly matters.