Choosing the right stainless steel welding rod sizes is crucial for achieving optimal results in welding projects. Understanding the various factors influencing this choice enhances the quality and durability of welded joints. This article delves into the intricacies of stainless steel welding rods, offering expertise, experience, authoritativeness, and trustworthiness to inform your decision-making.
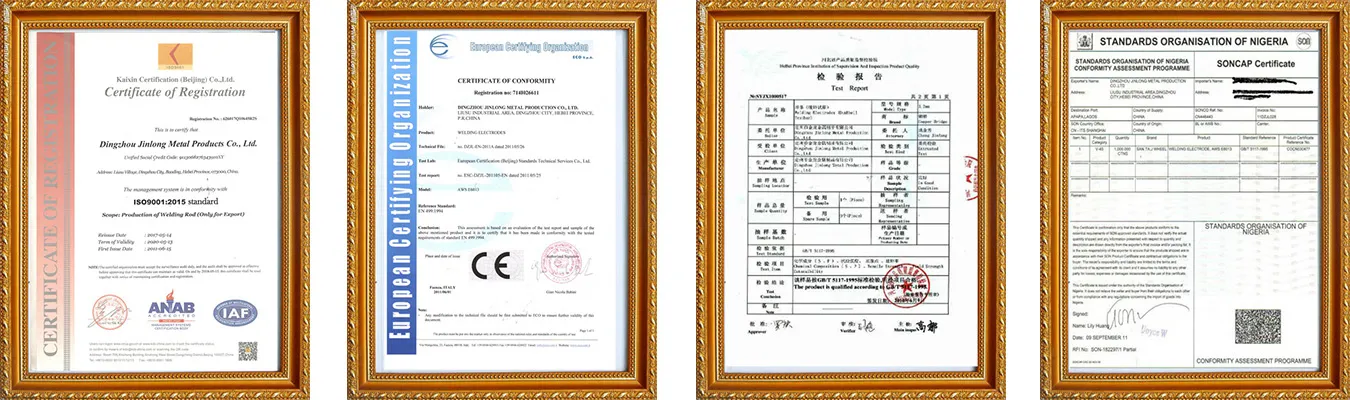
The diameter of a stainless steel welding rod significantly impacts the welding process. Thinner rods, such as those measuring 1/16 inch or 1.6 mm, are ideal for light-duty work and intricate details, providing precision but requiring skilled hands to avoid burn-through. Conversely, thicker rods, like those at 1/8 inch or 3.2 mm, are better suited for heavy-duty applications, offering robust joints and withstanding higher stress levels.
Welder proficiency is another critical consideration. Novices might prefer starting with mid-range rod sizes—3/32 inch or 2.4 mm rods—as they offer a balance between ease of use and application versatility. Experienced welders may venture into using both ends of the size spectrum, adapting their technique based on project requirements.
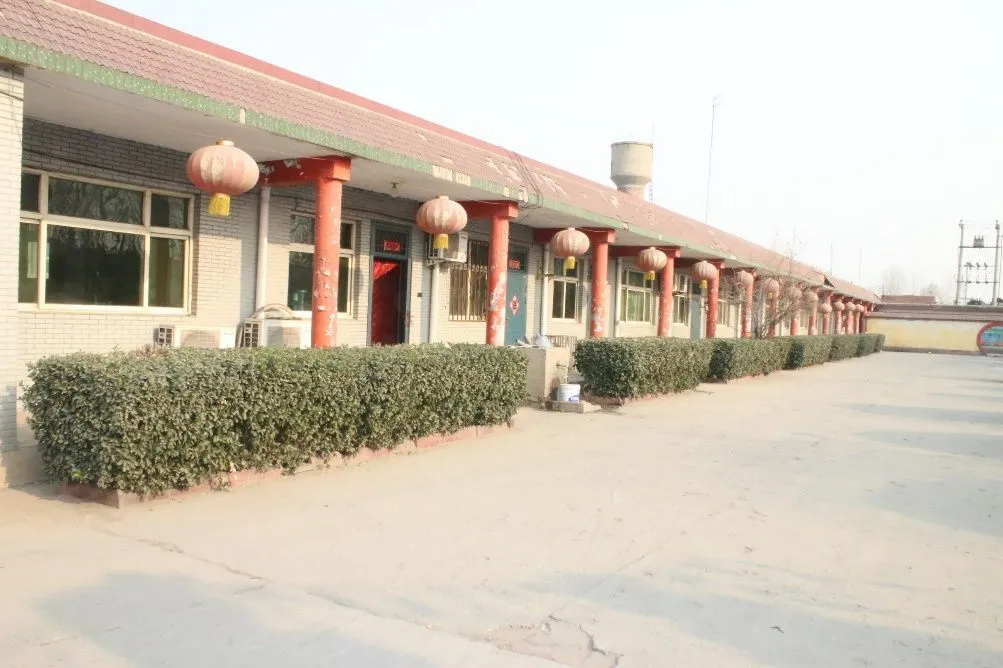
Material thickness is equally vital. Employing a rod size that matches the material ensures penetration without excessive melting. For example, when working with thin sheets of metal, smaller diameter rods prevent warping, while thicker materials benefit from larger rods, promoting strong, deep welds.
stainless steel welding rod sizes
The type of welding process also influences rod size selection. TIG welding often utilizes smaller rods due to the precision it demands, whereas stick welding can accommodate larger diameters for efficient material deposition. Different processes prioritize distinct parameters, necessitating customized rod choices to accommodate their unique characteristics.
Environmental conditions where welding occurs impact rod performance. In outdoor settings, where wind or moisture may be present, larger rods might be preferred to maximize weld integrity against disruptive elements. Furthermore, the harshness of the environment might dictate certain rod compositions, underscoring the importance of considering situational parameters.
Coating on stainless steel welding rods varies to enhance performance under specific conditions. Coatings improve arc stability and slag release, affecting the overall welding experience. Selecting the appropriate coating ensures optimal results, factoring into considerations like working positions and weld appearance.
In conclusion, the selection of stainless steel welding rod sizes is not a mere technicality but a crucial determinant of project success. From the welder's expertise to environmental considerations and material characteristics, numerous elements guide this choice. Adopting the right rod size enhances structural integrity, weld appearance, and efficiency, positioning your projects for longevity and strength. Leveraging this understanding demonstrates authoritativeness and trustworthiness, providing the insights necessary to make informed, expert decisions in stainless steel welding endeavors.