When embarking on a welding project involving the fusion of stainless steel 304 (SS 304) to mild steel (MS), selecting the right electrode is crucial. This seemingly straightforward task requires a deep understanding of the distinctive properties of each metal and the interactions that occur during the welding process. With years of expertise and professional insights, this guide aims to illuminate the technical nuances involved in choosing the appropriate welding electrode for SS 304 to MS.
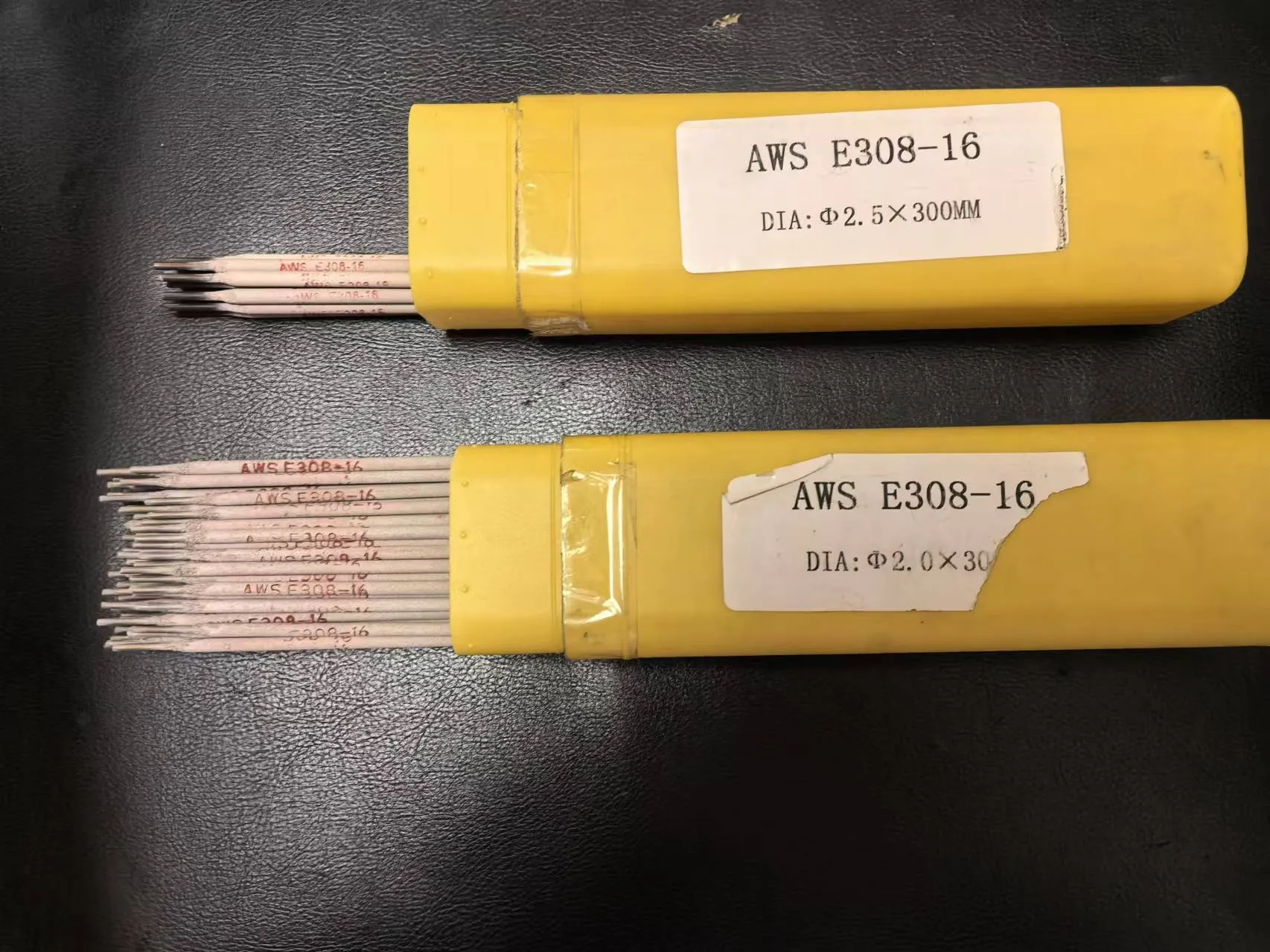
Understanding the Materials SS 304 is an austenitic stainless steel known for its superb corrosion resistance and formability, making it ideal for a range of applications from industrial to architectural sectors. On the other hand, mild steel boasts high ductility and pliability, characterized by a lower carbon content that enables excellent weldability.
Challenges in Welding SS 304 to MS The primary challenge lies in mitigating the differences in thermal expansion, melting points, and chemical composition. Mismatched thermal expansion rates can lead to cracking, while differing corrosion resistance means the joint may become a potential point of failure without proper protection.
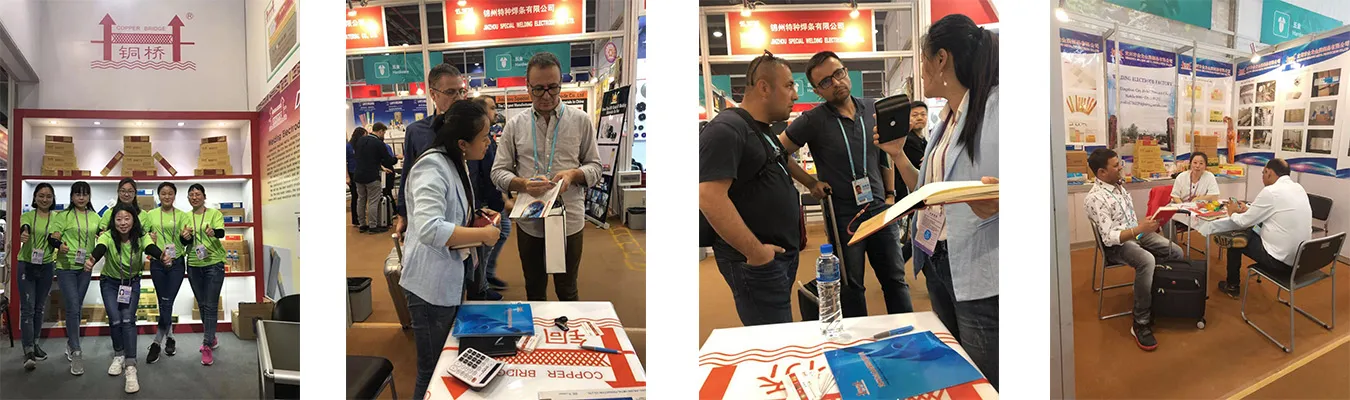
Electrode Selection For welding SS 304 to MS, a nickel-based electrode, typically an E309 or E309L, is often advocated by experts. These electrodes are designed specifically to handle dissimilar metal welding because they offer a compositional compromise that manages the metallurgical differences. E309L contains lower carbon content that minimizes carbide precipitation, thus reducing the risk of intergranular corrosion.
ss 304 to ms welding electrode
Technical Execution The welding procedure should include careful control of heat input to prevent overheating either metal, which could lead to warping or burning through.
It is vital to calibrate the welding machine settings to match the electrode type, thickness, and position of the weld. Experts recommend using a direct current electrode positive (DCEP) setting for generating the requisite depth of penetration without compromising the base metals.
Testing and Verification Post-welding, it is paramount to conduct thorough inspections and non-destructive testing (NDT) to ensure the integrity of the weld. Methods such as radiographic testing (RT) and ultrasonic testing (UT) provide insights into hidden defects that may not be visible to the naked eye. Additionally, a corrosion resistance test may be necessary to ascertain the longevity of the welded joint in corrosive environments.
Conclusion A successful weld between SS 304 and MS hinges on a comprehensive understanding of the underlying metallurgical principles, meticulous electrode selection, and proficient execution. Prioritizing these factors not only ensures a robust, durable joint but also enhances the overall quality and lifespan of the welded structure. Trust in professional expertise and authoritative guidance is essential to achieving excellence in welding projects involving dissimilar metals.
By drawing on the wealth of practical experience and technical know-how, this guide empowers you to make informed decisions and tackle complex welding challenges with confidence and precision.