Selecting the right welding rod for a project plays a crucial role in determining the final quality and integrity of the weld. The 5 32 welding rod 7018 stands out as an exceptional choice for professionals seeking a balance between ease of use and superior results. For those venturing into the realm of arc welding, understanding the merits and nuances of the 7018 electrode is essential.
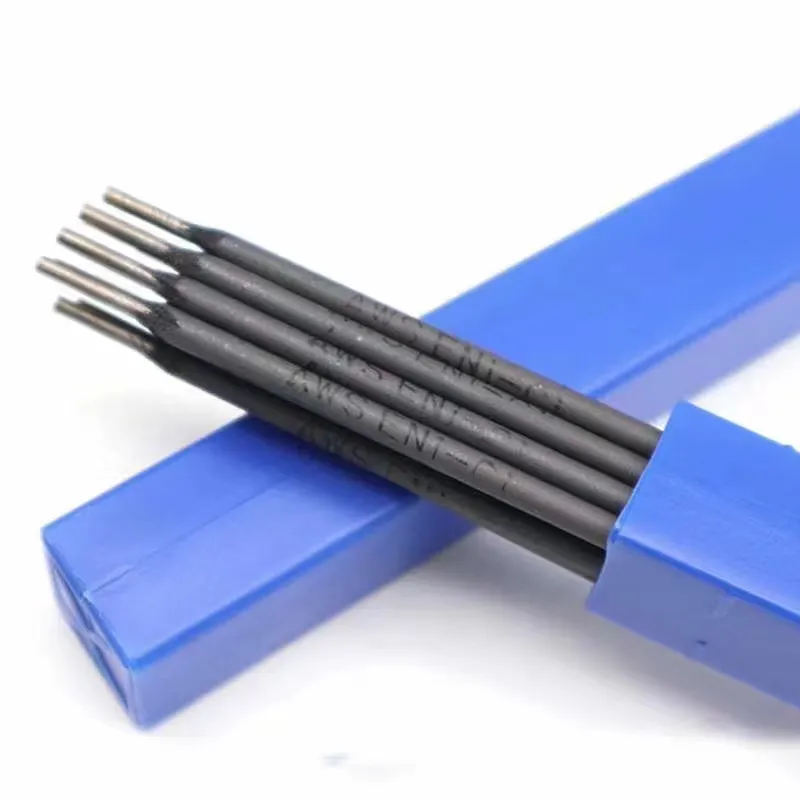
The 7018 welding rod is revered in the industry for its versatility and high strength characteristics, suitable for numerous applications. Its designation is more than just numbers; it speaks volumes about its composition and usability. The number '70' in 7018 denotes a tensile strength of 70,000 psi, making it a formidable tool in construction projects requiring strong, durable welds. The '1' signifies all position welding, allowing welders to work comfortably in flat, horizontal, vertical, and overhead positions, which is crucial for projects with complex geometries. Lastly, the '8' refers to the low-hydrogen potassium coating and an AC or DCEP (reverse polarity) current.
One of the standout features of the 7018 rod is its low-hydrogen coating. Hydrogen embrittlement can be a welder's nightmare, especially in structural welding, leading to cracks and compromised weld integrity. Fortunately, 7018 rods minimize this risk, promoting sturdier welds that resist cracking over time. This feature alone makes them indispensable in critical applications like bridge construction, pressure vessels, and high-rise buildings, where weld failure could have catastrophic consequences.
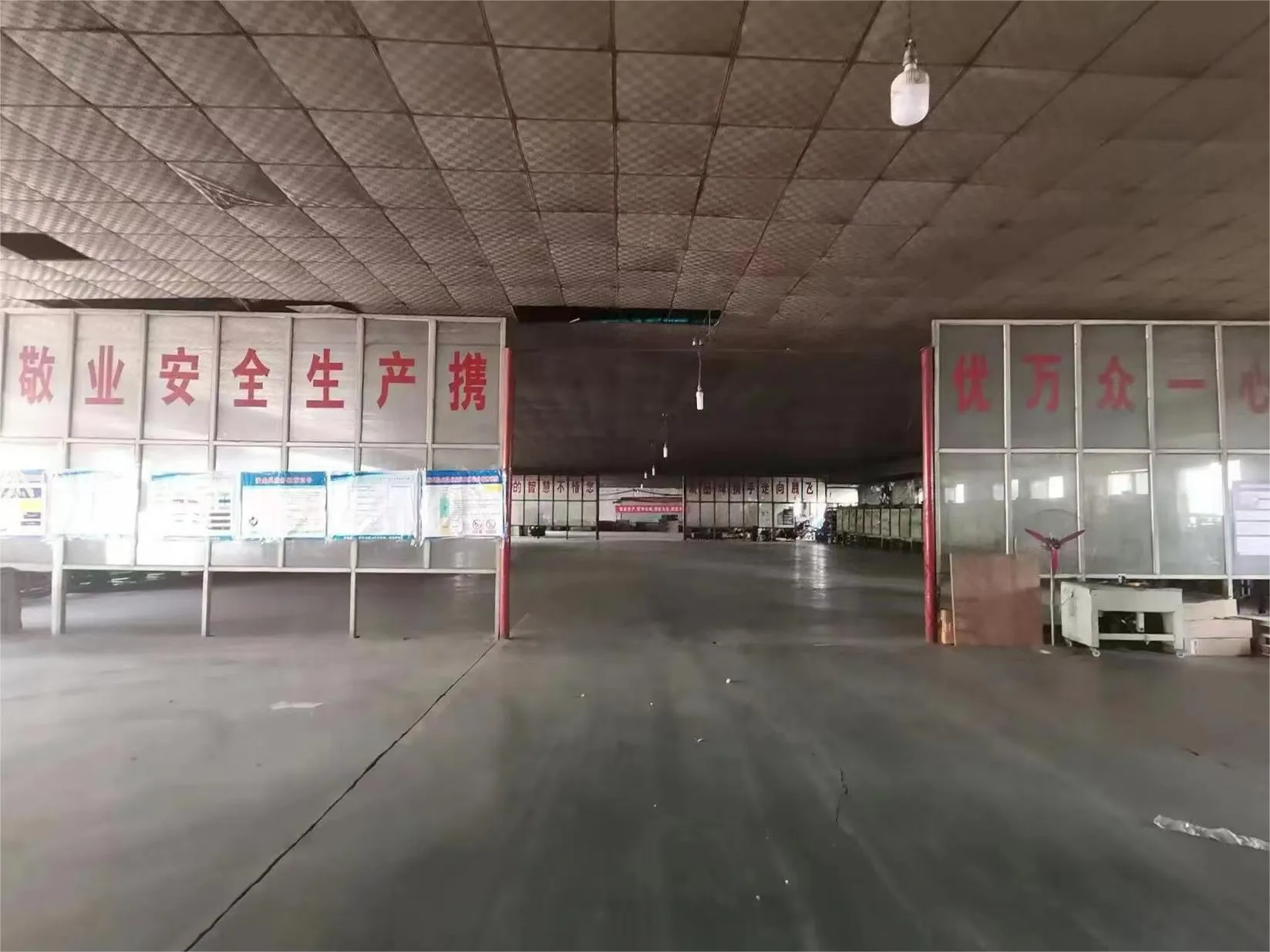
In practice, using a 5/32 7018 rod provides distinct advantages, particularly when working on thicker materials. The rod's diameter allows for deeper penetration, ensuring a robust bond between the base metals without the need for multiple passes. This efficiency not only speeds up the welding process but also enhances the quality of the weld, reducing the chances of defects that can arise from multiple starts and stops.
However, like any tool, successful outcomes with the 7018 rod rely on careful handling and technique.
Storage and preparation are as critical as the welding process itself. Due to the low-hydrogen nature, these rods need to be kept in a controlled environment, ideally in a rod oven, to prevent moisture absorption. Moisture can lead to hydrogen entrapment, which defeats the purpose of using a low-hydrogen rod in the first place. Ensuring optimal storage conditions is a testament to a welder's professionalism and dedication to delivering high-quality work.
5 32 welding rod 7018
For welders accustomed to the nuances of different rods, the 7018 offers a smooth, stable arc and a clean, presentable weld. Its slag is easily removable, and the resultant weld has an aesthetically pleasing appearance, typically requiring minimal finishing work. This attribute is particularly beneficial in projects where the visual presentation of the weld is just as important as its strength, such as in ornamental ironwork or visible steel structures.
While the 7018 is largely celebrated, successful use requires skill and understanding of its unique characteristics. Novices might find this rod slightly challenging due to its specific heat requirements and the importance of maintaining the correct arc length. However, with practice and a little guidance from seasoned professionals, most welders can harness the full potential of the 7018, producing superior quality welds that stand the test of time.
Beyond the technical aspects, the 5/32 7018 rod embodies the spirit of what it means to be a welder a pursuit of excellence, precision, and attention to detail. Investing time in understanding this tool is investing in one’s craft. Professional development workshops and certification programs often emphasize the effective use of 7018 rods, underscoring their significance in the welding arsenal.
In conclusion, the 5/32 7018 welding rod is more than just an option; it is a cornerstone in the world of welding, representing strength, reliability, and versatility. As technology evolves and industry demands grow, the foundational importance of such tools remains constant, reminding welders of the essential balance between innovation and time-tested techniques. Whether a project demands resilience under stress or immaculate weld lines, the 7018 is equipped to meet and exceed expectations, reassuring both welders and their clients of a job well executed.