In the intricate world of metal fabrication, welding rod welding stands as a fundamental technique influencing durability, design, and functionality. Those acquainted with this craft understand the significance of selecting the appropriate welding rod, a decision that is far from trivial. Experienced welders have long acknowledged the profound impact of this choice on weld quality, structural integrity, and project success.
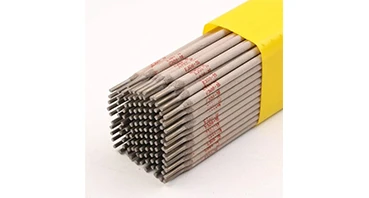
Welding rods, or electrodes, are essential in welding processes that fuse metals by generating the heat needed to melt and join parts.
The type of welding rod used often dictates the quality of the weld, making the decision incredibly important. With a seemingly endless array of options, each welding rod is designed to cater to specific welding types, materials, and environmental conditions.
When delving into the realm of welding rod welding, experts emphasize a few critical factors. First, the type of material being welded—whether it's carbon steel, stainless steel, or aluminum—determines the choice of welding rod. For example, for carbon steel, rods such as E6010 or E7018 are favored due to their deep penetration and strong material flow properties. These rods are widely praised for their strength and versatility, often used in structural steel applications.
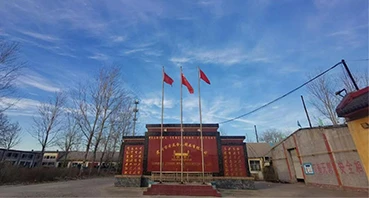
Education and experience play pivotal roles in honing welding proficiency. The various classifications of welding rods, denoted by parameters such as tensile strength, welding position, and type of coating, require not only theoretical comprehension but also practical application to master. The American Welding Society (AWS) classification system is key in guiding welders toward choosing the right rod, highlighting the importance of professional expertise in this field.
Additionally, the operational environment is a consideration that cannot be overlooked. Welding in controlled environments allows for greater flexibility in rod selection, while fieldwork might necessitate rods with specific moisture resistance or those suited for all-weather performance. Here, the trustworthiness of established manufacturers becomes central. Brands with longstanding reputations, spotlighted in industry publications and supported by user reviews, often provide the reliability required for critical welding tasks.
welding rod welding
Furthermore, the technique itself—an amalgamation of art and science—enhances the authoritative nature of welding rod welding. It demands a steady hand, a discerning eye, and an acute awareness of the metal's response to heat. Professionals adept in this trade make adjustments on the fly, guided by their extensive knowledge and intuition born from years of practice.
For those aiming to optimize their welding outcomes, attending specialized training workshops and gaining certifications can substantially enrich their expertise, offering them an expanded skillset reinforced by practical demonstrations. Such proactive education solidifies their authority in welding techniques, underlining their commitment to maintaining high standards of safety and precision.
Trustworthiness forms the foundation of any successful welding operation, culminating in client satisfaction and project durability. A welder’s ability to advise on the best materials, foresee challenges, and articulate potential solutions fosters a dependable relationship with clients and stakeholders.
In conclusion, welding rod welding requires a blend of experience, specialized knowledge, and proven methodologies to achieve optimal results. Professionals in this field continue to evolve their skillsets, adapting to new technologies and materials while maintaining the highest standards of industry practice. This dedication not only ensures the longevity and strength of their creations but also elevates the craft to an esteemed level within metal fabrication sectors.