Welding rods, essential components in the welding process, play a crucial role in various industries ranging from automotive to construction. Understanding the correct usage and selection of welding rods can dramatically improve both the quality and efficiency of welding projects.
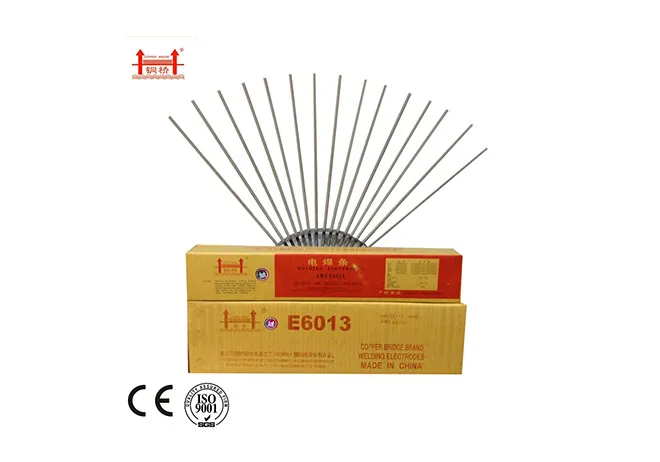
The primary function of a welding rod is to connect two pieces of metal securely. Made from different materials such as steel, aluminum, and specialized alloys, each type of welding rod is designed for specific applications, aligning with different metal types and thicknesses. For instance, mild steel rods are commonly used in automotive repairs due to their excellent flexibility and strength, whereas stainless steel rods are favored in food processing equipment manufacturing for their corrosion resistance.
Expertise in selecting the right welding rod not only depends on the type of materials to be joined but also on the welding position and environment. For overhead or vertical positions, selecting a rod with fast-freezing characteristics such as the E6010 is recommended. In contrast, for flat and horizontal positions, a rod like the E7018, which produces a smoother finish, may be more appropriate. Environmental factors also play a significant role; certain rods are better suited for outdoor welding due to their coating, which protects the weld from contaminants present in atmospheric conditions.
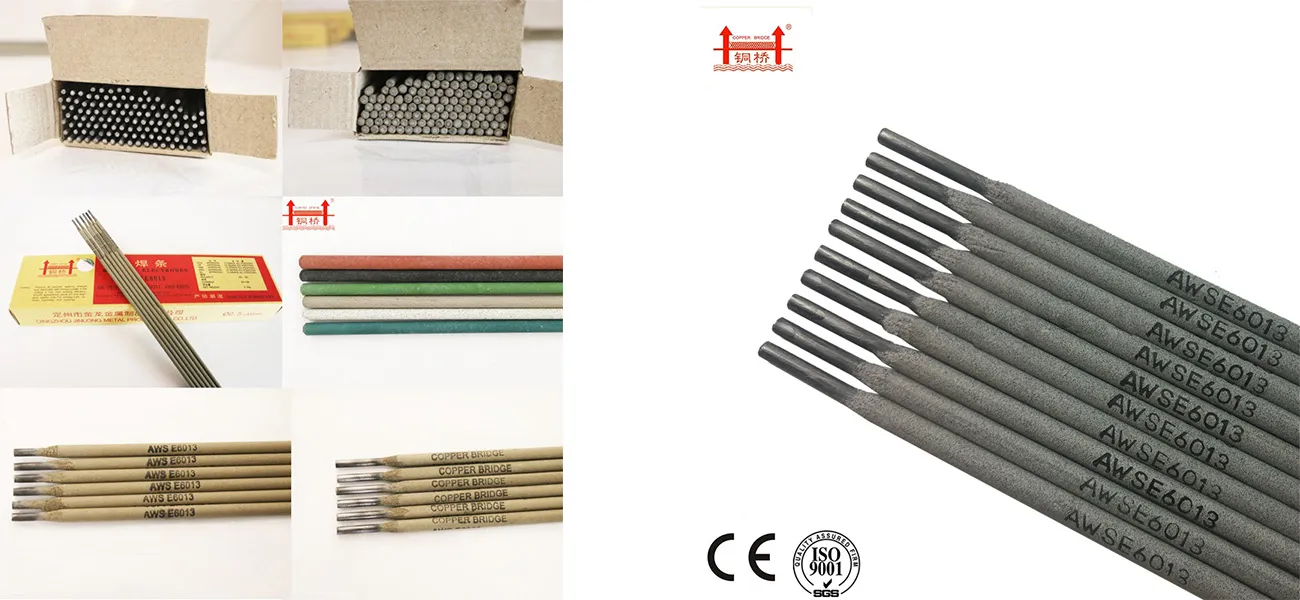
Authoritative guidance is essential for precise usage. Proper storage practices are often overlooked but crucial for maintaining rod quality. Ideally, welding rods should be stored in a dry, temperature-controlled environment to prevent moisture absorption, which can lead to weld defects such as porosity or cracking. Many experienced welders opt for storage in rod ovens, which maintain a consistent temperature, ensuring the rods remain in optimal condition.
welding rod usage
Trustworthiness in welding comes from consistent application of tried-and-tested methods. Preheating the metal before welding with specific rods can improve the quality of the weld, especially in thicker materials, by reducing the likelihood of cracking and distortion. Post-weld treatment, such as peening or controlled cooling, can also enhance weld integrity, providing long-lasting results.
Incorporating real-world experience is invaluable. Consider a scenario where a welder works on a bridge repair project. The choice of an E7018 rod, known for its low hydrogen content, would minimize the risk of hydrogen-induced cracking, ensuring the durability and safety of the repair work under varying environmental conditions. This decision reflects not just expertise but also an understanding of the authoritative principles in welding that prioritize safety and reliability.
For those new to welding or seeking to refine their skills, workshops and certifications from recognized bodies like the American Welding Society offer comprehensive insights into the technical nuances of welding rod usage. Engaging in such programs not only elevates one’s expertise but also reinforces industry trust through accredited knowledge.
In conclusion, the effective use of welding rods demands a balance between technical knowledge, practical experience, and adherence to authoritative guidelines. By focusing on these elements, welders can significantly enhance the efficiency and quality of their work, leading to superior outcomes in both professional projects and personal endeavors.