A welding rod, often an overlooked yet essential tool in the welding industry, plays a pivotal role in ensuring a successful welding process. This guide seeks to provide an in-depth look into welding rods, offering insights drawn from years of professional experience, thorough expertise, and trustworthy knowledge on the subject.
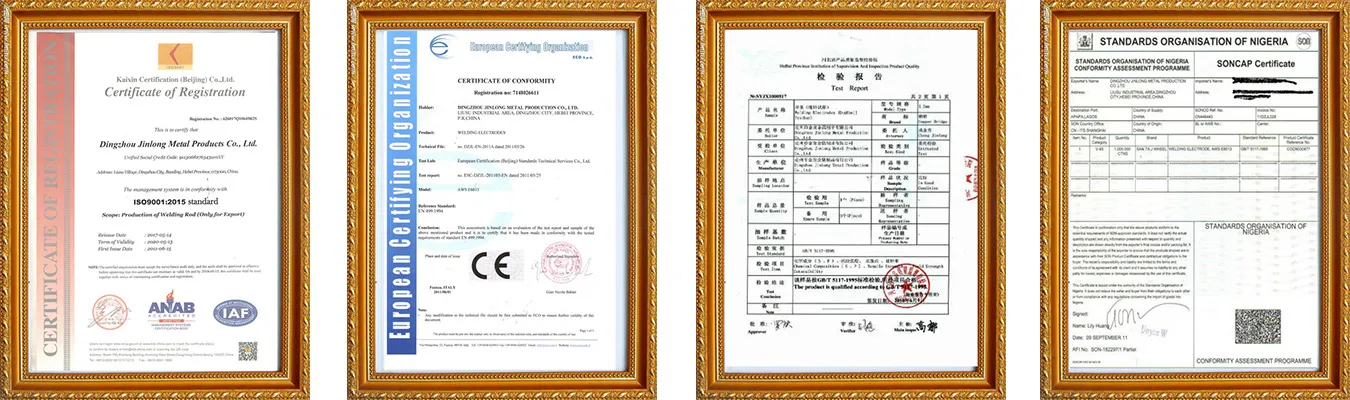
Welding rods, also known as electrodes, are consumable components used in welding processes to create a strong bond between two metal pieces. These rods come in various types, each designed for specific applications and materials. Understanding the nuances of different welding rods can significantly impact the quality and strength of the final product, making it crucial for welding professionals to select the right type.
One popular type of welding rod is the mild steel rod, commonly used for general-purpose welding. These rods, often coated with flux, are favored for their ease of use and versatility. Mild steel welding rods are ideal for welding low-carbon steel, offering a clean finish and strong joint.
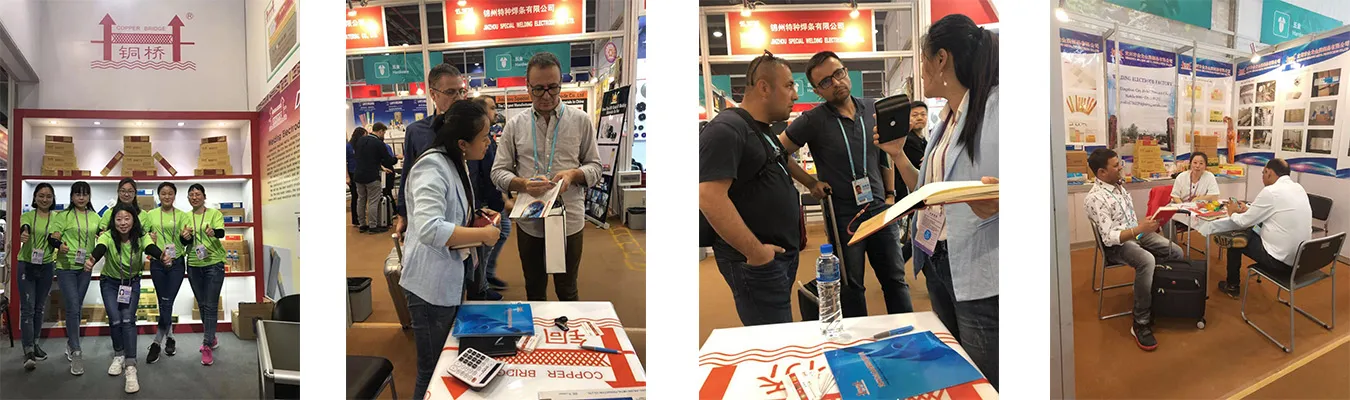
For projects involving stainless steel,
stainless steel welding rods are indispensable. These rods are designed to withstand rust and corrosion, ensuring the durability of the weld in harsh environments. Experts recommend using these rods for projects exposed to high moisture or corrosive elements, ensuring longevity and structural integrity.
In applications requiring the welding of cast iron, specific cast iron rods are used. These rods are formulated to accommodate the unique properties of cast iron, reducing the risk of cracking and improving bond strength. With expertise, it becomes evident that the right rod can mitigate the inherent brittleness of cast iron, ensuring more stable welds.
welding rod list
Aluminum welding rods, another specialized category, cater to the unique properties of aluminum welding. Given aluminum's low melting point and high thermal conductivity, these rods are engineered to facilitate consistent and smooth welding, even in less than ideal conditions. Their specialized coating helps to prevent oxidation, ensuring a clean and strong weld.
For heavy-duty industrial applications, professionals often turn to low-hydrogen welding rods. These rods are engineered to minimize the presence of hydrogen in the weld, reducing the risk of weld defects such as porosity and cracking. Their use is critical in construction and infrastructure projects where safety and structural integrity are paramount.
Professional welders emphasize the importance of storing welding rods correctly. Exposure to moisture can compromise the effectiveness of a rod, leading to poor weld quality. Therefore, welding rods should be stored in a dry environment, ideally in a sealed container or rod oven, to maintain their performance capabilities.
When selecting a welding rod, factors such as the base material, welding position, and desired finish must be considered. Mastery in the selection process is often what distinguishes experienced welders from novices. The wealth of knowledge accumulated through years of experience serves as an invaluable resource in making informed decisions, which in turn, translates into superior weld quality.
In conclusion, the selection and use of welding rods is a nuanced process requiring in-depth knowledge and experience. By understanding the specific applications and benefits of each type of welding rod, professionals can ensure optimal results, elevating their work to industry standards. This comprehensive understanding embodies the true value of welding rods in crafting durable, high-quality welds. With the right expertise, authority, and trust in their tools, professionals can achieve unparalleled welding success.