The use of electrodes in welding is a cornerstone of the welding industry, integral to the successful execution of various projects across different sectors. This pivotal role underscores the need for a deep understanding of how electrodes enhance welding processes, making it essential for professionals to be well-versed in their applications and benefits.
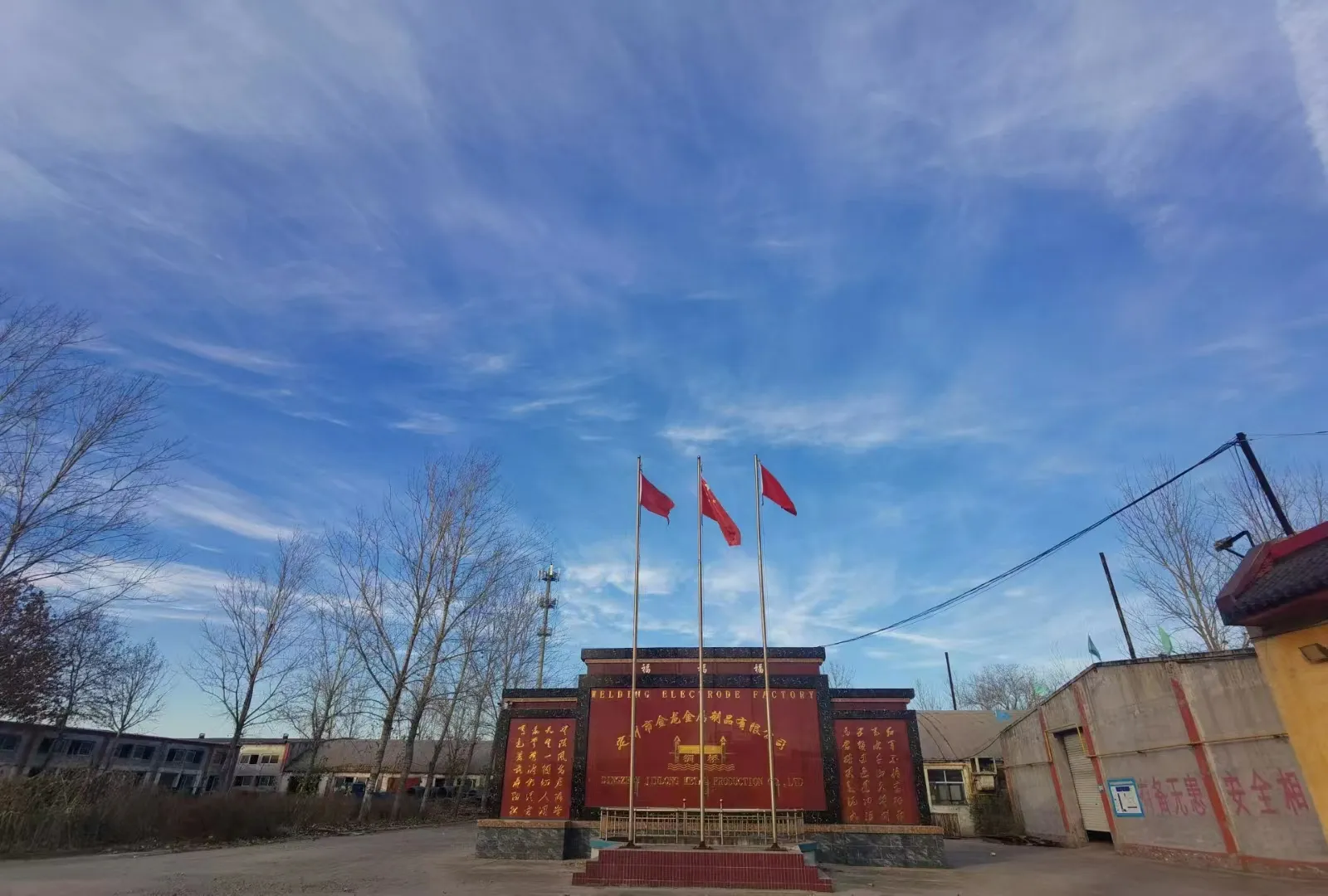
Electrodes serve as vital components in the welding circuit, crucial for conducting current and forming an arc necessary for melting and fusing metals. They come in different types, each suited for specific welding applications and materials. Stick electrodes, or shielded metal arc welding (SMAW) electrodes, are among the most common, known for their versatility and ability to weld a variety of metals. They are especially valuable in outdoor environments due to their resistance to wind and draft.
The choice of electrode significantly impacts the quality and strength of the weld. For beginner welders, using a general-purpose stick electrode like the E6013, which offers smooth arc characteristics and minimal spatter, can be a good starting point. Professionals, however, often opt for the E7018, particularly for projects requiring high strength and ductility, such as structural steel welding. Its low-hydrogen content reduces the risk of cracking, making it ideal for critical applications.
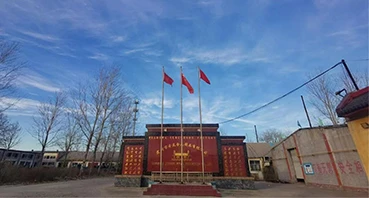
In more advanced settings, tungsten electrodes are used in Gas Tungsten Arc Welding (GTAW), also known as TIG welding. Their non-consumable nature distinguishes them, providing a precise and controlled welding process crucial for high-quality applications such as aerospace and automotive manufacturing. The chemical composition of tungsten electrodes, often embedded with thorium or lanthanum, enhances their performance by improving arc stability and longevity.
use of electrode in welding
For industries heavily involved in pipeline construction or shipbuilding, submerged arc welding (SAW) electrodes are indispensable. These electrodes, combined with a flux, enable deep penetration and high deposition rates, which are vital for creating robust welds on thick materials. This method also significantly increases productivity, making it a preferred choice in heavy-duty fabrication.
In recent years, the development of specialized electrodes has brought innovation to welding technology. For instance, cellulose electrodes are increasingly used in vertical-down welding, offering rapid cooling rates that minimize distortion and enhance weld appearance. Additionally, advancements in electrode coating technology have led to the creation of low-fume electrodes, addressing health concerns while maintaining efficacy.
Understanding the nuances of electrode selection and application reflects a welder’s expertise and contributes significantly to the overall success of welding projects. Proper training and experience in handling various electrode types ensure both the reliability and safety of welded structures. Furthermore, keeping abreast of technological developments in electrode materials and coatings enables welders to enhance their craft, promoting efficiency and quality in their work.
Trust in the quality and integrity of the final product hinges on the welder’s capacity to appropriately select and utilize electrodes. Through rigorous training and ongoing education, welders can build expertise that inspires confidence in clients, adhering to the highest standards of workmanship and safety in the industry. This expertise not only elevates professional credibility but also underscores a commitment to delivering superior welding solutions.