The utilization of welding rods is fundamental in the realm of metal fabrication and repair. These versatile tools are indispensable for achieving strong, reliable welds, ensuring that structures, from small-scale repairs to grand engineering feats, maintain their integrity and longevity. A deeper understanding of welding rod functionalities, types, and applications can significantly improve desirability and performance in diverse welding projects.
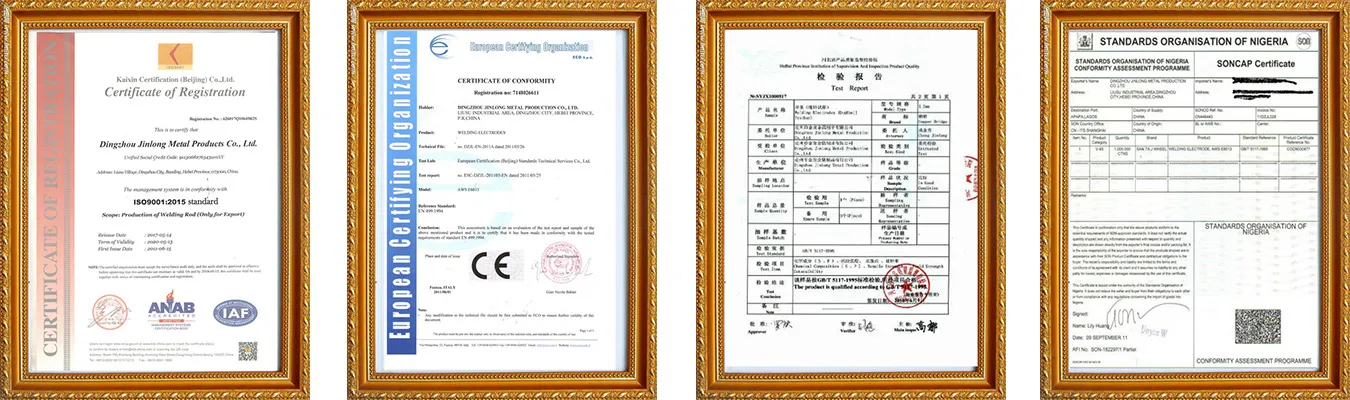
Welding rods, also known as filler metals or electrodes, serve a critical function in the welding process by fusing two pieces of metal together. Depending on the type of welding technique employed—whether it’s Shielded Metal Arc Welding (SMAW), Tungsten Inert Gas welding (TIG), or Metal Inert Gas welding (MIG)—the selection of a suitable welding rod is imperative. Each type boasts unique properties and compositions tailored to distinct materials and welding processes, thus naming it integral for achieving optimal weld results.
For Shielded Metal Arc Welding, the consumable electrodes are generally preferred. These rods are coated with a material that generates a shielding gas to protect the molten weld pool. One popular choice among professionals is the E6011 or E6013 rods, known for their deep penetration qualities and versatility in welding low-carbon or mild steels. In contrast, TIG and MIG welding involve non-consumable or semi-permanent electrodes that require additional filler rods. Here, options range from aluminum rods to stainless steel, each selected based on the parent material being welded.
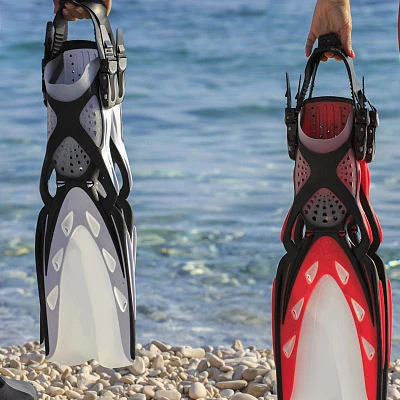
Understanding the composition and specifications of welding rods is crucial to selecting the right product for specific projects. Essentially, the chemical make-up of a welding rod ought to complement the qualities of the base metals. Factors such as tensile strength, ductility, and corrosion resistance drive this selection process. For example, when welding stainless steel, opt for rods with chromium and nickel content, enhancing resistance to rust and wear.
use of welding rod
Moreover, the welding environment influences the choice of rods considerably. Outdoor projects often require rods that endure wind and variable weather conditions, whereas indoor or controlled environments allow for more flexibility. The E7018 rod, known for its low-hydrogen properties, is an excellent choice for projects demanding high resistance to cracking and superior strength under stress.
The proficiency in wielding welding rods not only bolsters the structural integrity of welds but also reduces the likelihood of defects. Familiarity with the voltage settings, amperage, and appropriate welding speed all contribute to the creation of a strong, uniform weld bead. Additionally, maintaining the chosen rod at the correct angle and pace prevents issues like undercutting or slag inclusions, which could compromise the durability of the weld.
For optimal trustworthiness and authoritativeness in product selection and usage, relying on reputable brands and manufacturers is advisable. Renowned names in the welding industry invest in rigorous testing and quality control, offering products that meet international standards. Furthermore, consulting with seasoned welding engineers or technical experts can provide crucial insights and recommendations tailored to specific project requirements.
In sum, welding rods epitomize a core component in the toolkit of any professional welder. Understanding their applications, attributes, and effective usage is essential for anyone endeavoring in the skilled craftsmanship of metalwork. By leveraging expert knowledge and trusted products, welders can ensure they produce high-quality results that stand the test of time, effectively endorsing the significance of welding rods in the field of metal fabrication.