Welding is an essential process in various industries, requiring precision and an understanding of the tools involved. Among the crucial components are welding rods, which come in various sizes, each suitable for specific tasks. This article delves into the types of welding rod sizes, focusing on providing insightful expertise to both novices and seasoned professionals.

In welding, selecting the appropriate rod size is integral to the strength and quality of the weld. Rod sizes typically range from 1/16 inch to several inches in diameter, and each size serves a different purpose. The choice of rod impacts the heat input and penetration, which are critical for the integrity of the joint.
Smaller rods, around 1/16 inch to 3/32 inch, are often used for thin materials. They require lower amperage, reducing the risk of burning through the material. These rods are ideal for sheet metal work such as car body repairs or thin-walled applications. Many professionals prefer smaller rods for detailed work because they allow for greater control and finesse.
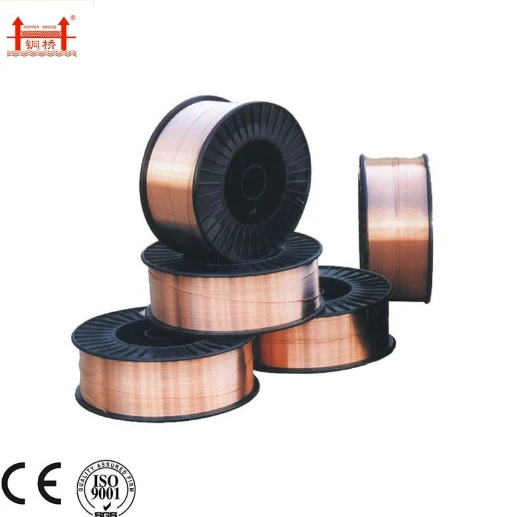
Medium-sized rods, like 1/8 inch and 5/32 inch, are versatile and prevalent in general-purpose welding. They are suitable for materials of moderate thickness, typically ranging from 1/8 inch to 1/4 inch. Their adaptability makes them a popular choice in construction and structural applications. These rods provide a balance of control and penetration, making them effective for both horizontal and vertical welding positions.
Larger rods, from 3/16 inch upwards, are mainly used in heavy-duty welding tasks. They are designed for thicker materials, such as steel beams and heavy machinery. These rods necessitate higher amperage, which offers deeper penetration, ensuring the structural stability of the joint. However, they require a skilled hand, as improper use can lead to excessive heat build-up or distortion.
types of welding rod sizes
Understanding when to use each type of welding rod size comes from experience and technical knowledge. Factors like the material type, thickness, and desired weld strength are vital considerations. For example, stainless steel and aluminum each have unique properties requiring specific rods and sizes.
Moreover,
different welding processes favor certain rod sizes. SMAW (Shielded Metal Arc Welding), commonly known as stick welding, often uses medium to large rods due to its robust nature. In contrast, TIG (Tungsten Inert Gas) welding frequently employs smaller rods, necessary for its precision-oriented technique.
The expertise in selecting rod sizes also extends to the storage and care of the rods. Moisture and contamination can significantly affect the performance, leading to weak or inconsistent welds. It's vital to store rods in a dry, temperature-controlled environment and to handle them with clean gloves to maintain their effectiveness.
For novice welders, understanding the impact of rod size on their work is a journey of trial and error intertwined with guidance from more experienced welders. Attending workshops or training sessions can greatly enhance one’s practical knowledge and confidence.
In conclusion, the variety in welding rod sizes caters to the diverse needs of different welding applications. Mastery of choosing and using the right size not only reflects a welder’s expertise but also ensures the durability and safety of the welds produced. Leveraging the right combination of rod sizes and welding techniques differentiates a skilled professional in the field of welding, highlighting their trustworthiness and authority in the craft.