Choosing the correct settings for welding rods, particularly the 6010 variant, is pivotal for achieving optimal results in any welding operation. When aiming to use a 3/32 6010 welding rod, understanding the precise amp setting can influence the quality and integrity of the weld. This article will delve into this subject with an emphasis on real-world experiences, technical expertise, and authoritative insights.
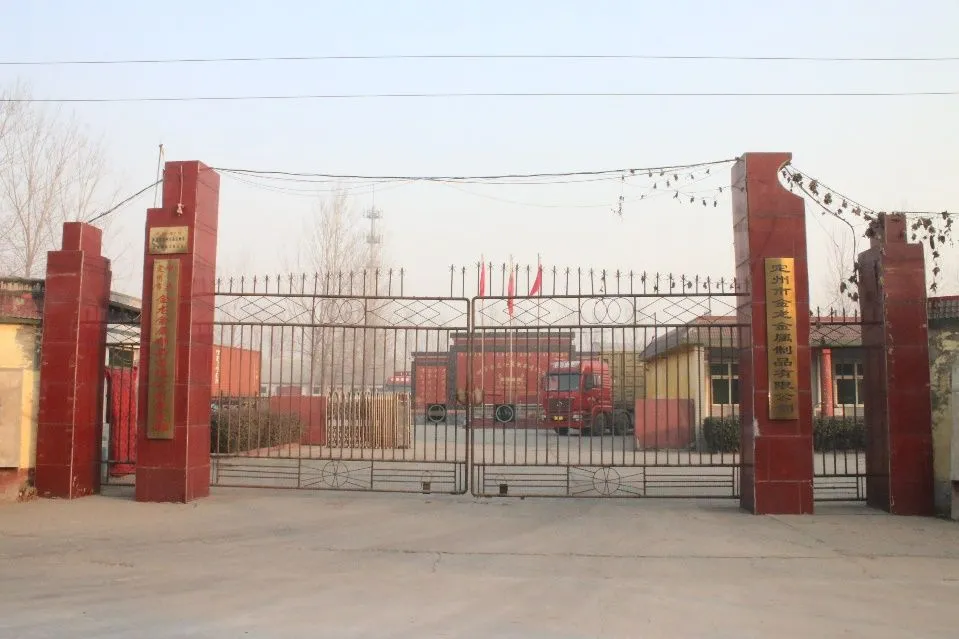
Before exploring the amp settings, it's important to comprehend the characteristics of a 6010 rod. Known for deep penetration and fast-freezing qualities, 6010 rods are favored for root passes and tasks requiring strong weld integrity. Their high cellulose sodium coating makes them ideal for welding on rusted or dirty surfaces, a common scenario in fieldwork.
A key factor in using a 3/32 6010 rod is amperage setting. While the general recommendation for this size is between 40 to 85 amps, multiple variables affect the exact choice within this range. Personal experience shows that materials, joint design, and the welder's skill level must align with these settings for desired outcomes.
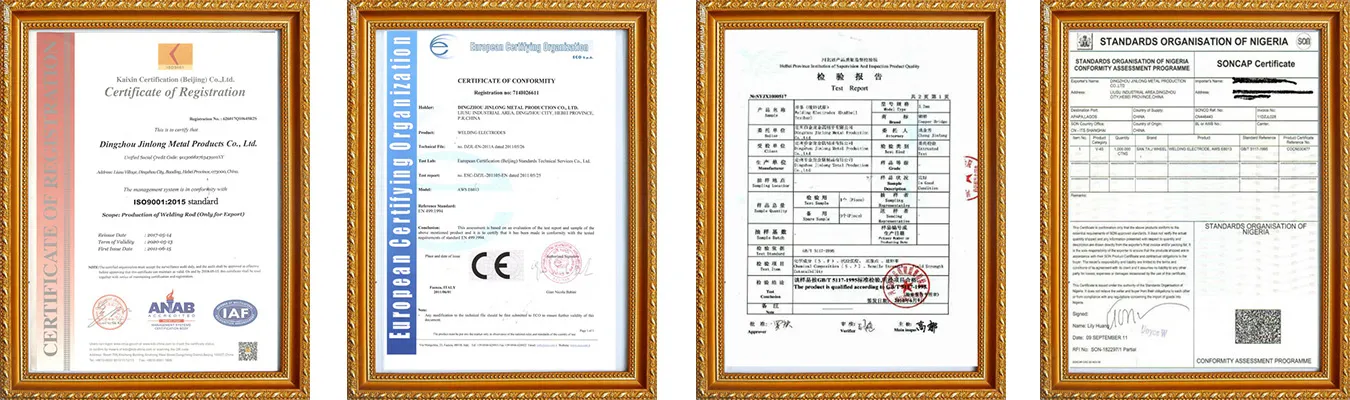
From the perspective of an experienced welder, dialing in the perfect amperage is more of an art than a science. For instance, in situations where thin metals are being joined, starting with a lower amperage, around 50 amps, can prevent burn-through and excessive spatter, ensuring cleaner welds. However, for thicker metals requiring deeper penetration, adjusting to 75-85 amps might improve weld fusion, reducing the need for subsequent passes.
The workplace environment also plays a critical role in setting amperage. Welding in colder conditions might necessitate a slight increase in amperage to sustain the arc's heat and prevent defects such as porosity. Conversely, in a controlled shop environment where conditions are stable, a welder might find more consistency at the lower end of the recommended amperage spectrum.
3/32 welding rod 6010 amps
Reference to industry standards and manufacturer guidelines adds credibility and authority to our understanding. For example, Lincoln Electric and other authoritative bodies in welding manufacturing suggest specific parameters based on extensive testing and application assessments. Following such guidelines can enhance weld quality and adhere to safety protocols.
Trust in recommendations increases when they are backed by hands-on testing and endorsements by seasoned professionals. It's helpful to regularly consult experienced welding practitioners and instructors who not only train on these standards but also perform routine tasks using a variety of techniques and tools.
For those new to welding, practicing on scrap material with various amp settings can greatly improve proficiency and understanding. Documenting each attempt and the resulting weld's appearance contributes to a personal log of data, which can be analyzed for improving technique and performance.
Finally, while technology such as inverter-type machines offers more control over fine-tuning amperage settings, a welder's individual skill remains paramount. Consistent practice, knowledge of equipment, and a keen eye for detail are indispensable in achieving successful welds with 6010 rods.
In summary, a 3/32 6010 welding rod requires thoughtful consideration of amperage settings, tailored to specific project demands, environmental conditions, and material characteristics. Experienced judgment informed by authoritative guidance ensures each weld meets safety and quality standards, fostering trust in the welding process's effectiveness.