Choosing the right welding rod for stainless steel is crucial for ensuring strong, durable, and corrosion-resistant welds, making it a cornerstone for both hobbyists and professionals alike. When it comes to stainless steel welding, the selection of the electrode can significantly affect the quality of your work. Here is a detailed exploration, grounded in experience and expertise, to help you make informed decisions.
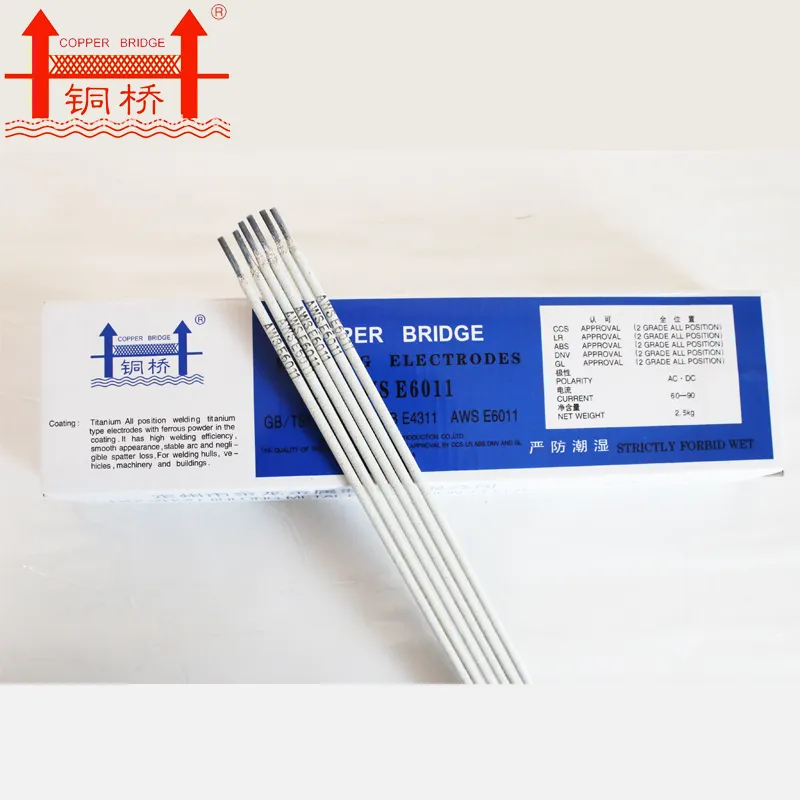
Stainless steel is prized for its corrosion resistance and aesthetic appeal, making it ideal for a variety of applications, from kitchen appliances to medical devices. The varying compositions and grades of stainless steel demand specific considerations for welding rods. Below is a comprehensive guide on selecting the appropriate welding electrode.
1. Understanding Stainless Steel Grades
Stainless steel comes in different grades, each with unique properties. The most widely used include austenitic, ferritic, and martensitic stainless steel, each requiring different welding techniques. Austenitic stainless steel, such as Type 304 or 316, is most commonly used due to its excellent resistance to corrosion and ease of fabrication.
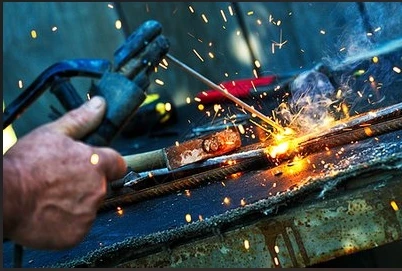
2. Selecting the Correct Welding Rod
The most suitable welding rods for stainless steel typically include the E308, E309, and E316 series, tailored to different applications and base materials.
- E308 Rods Designed primarily for welding austenitic 304-grade stainless steel. It provides excellent resistance to cracking and is highly popular in the food and beverage industry.
- E309 Rods Often suggested for welding dissimilar metals, like welding stainless steel to mild steel. These rods offer high corrosion resistance and maintain strength at elevated temperatures.
- E316 Rods Used for 316-grade stainless steel, which contains molybdenum, providing increased corrosion resistance, especially against chlorides and industrial pollutants.
what welding rod do i use for stainless steel
3. Factors to Consider
- Environment Consider the intended environment of the welded product. An environment high in salt, chemicals, or other corrosive elements will necessitate different rod choices for optimal durability.
- Desired Strength and Corrosion Resistance Select the rod that will deliver the mechanical properties required for the specific application. E316, for instance, offers superior strength and corrosion resistance under harsh conditions.
- Compatibility Ensure the welding rod is compatible with the stainless-steel grade being welded to prevent issues like cracking or weakening of the weld.
4. Welding Process and Technique
Different welding processes, such as TIG (Tungsten Inert Gas), MIG (Metal Inert Gas), and stick welding, have their specific requirements for welding rods and electrodes. Stick welding, commonly used in structural applications, frequently employs E308 and E309 electrodes due to their versatility and ease of use.
5. Professional Recommendations
Welding professionals emphasize pre-welding preparation, such as cleaning the stainless steel thoroughly to remove contaminants, which can affect the weld’s integrity and aesthetics. Moreover, maintaining the correct heat input is crucial to preventing discoloration and physical distortions.
6. Trust and Authority in Material
The choice of rod not only impacts the quality of the weld but also the trust in the welded component’s service life. Ensuring that rods are sourced from reputable manufacturers and comply with standards like AWS (American Welding Society) specifications further enhances trustworthiness and authority in your welding work.
7. Real-world Experiences and Insights
Engaging with communities and forums, where experienced welders share insights, troubleshooting tips, and personal experiences can offer invaluable practical knowledge. Many seasoned welders recommend experimenting with different electrode types and settings on scrap pieces to perfect the technique before embarking on critical welding tasks.
By integrating these factors and insights, you can ensure that your choice of welding rod for stainless steel not only aligns with the technical requirements but also delivers performance, safety, and aesthetic integrity. This careful selection process underscores the synthesis of experience, expertise, authority, and trust in achieving welding excellence with stainless steel.