TIG welding has become a cornerstone in the metalworking industry, and at the heart of this process lies a crucial component the TIG carbon steel filler rod. This article dives deep into the nuances of choosing and using TIG carbon steel filler rods, aiming to provide a comprehensive guide for welding enthusiasts and professionals seeking high-quality results in their projects.
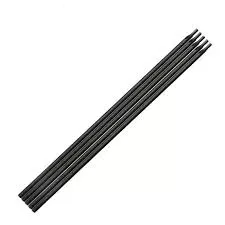
In the realm of TIG (Tungsten Inert Gas) welding, the selection of a filler rod is not just a procedural decision; it's an art that requires a blend of experience, expertise, and exactness. TIG welding, renowned for its precision and strong, clean welds, cannot achieve perfection without the aid of well-chosen filler materials.
Carbon steel filler rods are specifically designed for welding carbon and low-alloy steels, making them a staple for a variety of industrial applications—from automotive repairs to high-end architectural projects. They offer superb ductility and toughness, which are essential for preventing the cracking of welds under stress. Unlike some other filler materials, carbon steel rods blend well with base metals, allowing for ease of finishing and coating.
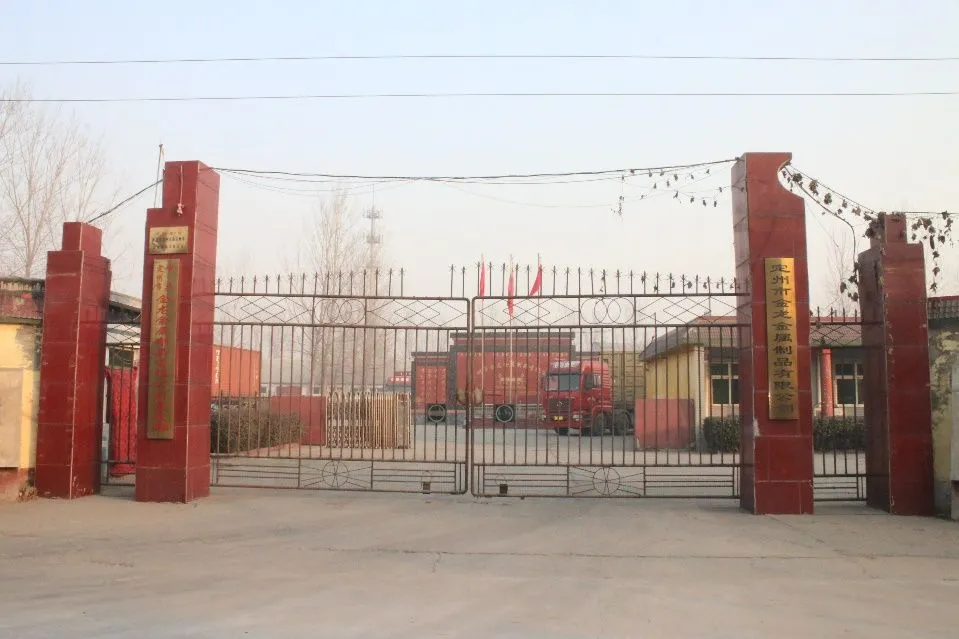
Choosing the right TIG carbon steel filler rod hinges on understanding its composition and the types of carbon steel it ideally complements. For instance, a popular choice is the ER70S-2 and ER70S-6 series, known for their high levels of deoxidizers which help in creating sound welds in both piping and sheet metal applications, even in conditions of rust or mill scale. This versatility underscores the rod's capacity to handle unforeseen circumstances in welding tasks, reinforcing trust in its use across varying conditions.
Experts in welding prioritize properties such as tensile strength, resistance to corrosion, and excellent formability when selecting filler rods. A seasoned professional is aware that not all welding conditions are optimal—humidity, temperature fluctuations, and impurities can all affect the outcome. Thus, relying on authoritative recommendations for filler rod types like the previously mentioned series ensures that welds maintain integrity even under less-than-perfect circumstances.
tig carbon steel filler rod
Furthermore, expertise in TIG welding is shown by understanding the intricacies of pre- and post-weld treatments. Air exposure during welding can introduce oxides into the weld pool; therefore, using a carbon steel filler rod that minimizes oxidation can yield better results. Additionally, adopting proper preheating techniques for thicker sections further enhances the effectiveness of the filler rod in creating seamless joints.
Hands-on experience speaks volumes when discussing TIG carbon steel filler rods. Professional welders who have honed their craft often share insights into maintaining cleanliness and focusing on technique finesse while using such rods. They stress the importance of consistent arc length, controlling heat input, and the steady addition of filler material—all of which contribute to weld excellence.
Trustworthiness in welding products is built over time with proven performance and reliability. Quality TIG carbon steel filler rods are tested rigorously for consistent chemical composition and mechanical properties. Purchasing from reputable manufacturers ensures adherence to these standards, thereby upholding strength and durability in your welding projects.
The versatility of TIG carbon steel filler rods cannot be overstated. From crafting bespoke metal art installations to constructing resilient infrastructure, the possibilities are vast. Skilled welders who understand their materials are more equipped to expand the bounds of their vocational creativity, often finding new challenges in the form of custom projects or exotic material combinations.
In conclusion, selecting the appropriate TIG carbon steel filler rod demands a synergy of professional insight and practical experience. Prioritizing product quality and understanding application-specific requirements are pivotal in achieving optimal results. As the choice of filler rod directly influences weld quality, investing time and resources in finding the right one underscores the commitment to excellence that defines a true welding artisan.