Choosing the right stainless welding rod number is an essential step in ensuring the success of your welding projects, whether for industrial applications or personal endeavors. Understanding which rod number to select can drastically affect the overall outcome, laying the groundwork for a superior finished product.
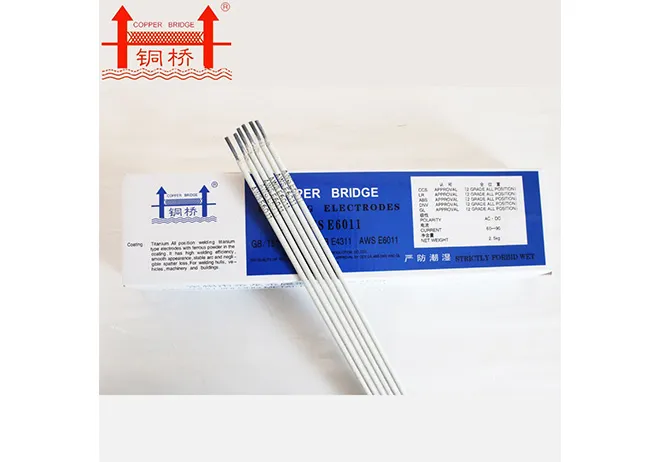
Stainless steel welding rods, also referred to as electrodes, come in a variety of numbers that denote their unique properties and suitability for specific types of welding jobs. As an experienced welder or a novice, grasping these numbers empowers you to select a rod that aligns with the specific requirements of your project. Let’s delve into why selecting the appropriate stainless welding rod number matters and how it influences your welding success.
The numbering system for stainless welding rods primarily relates to the rod's composition and its tensile strength, corrosion resistance, and ductility. Manufacturers typically utilize the AWS (American Welding Society) numbering system, which provides critical insights into the rod's characteristics. For instance, a common stainless welding rod like the E308L-16 offers several benchmarks—E designates the electrode, 308 indicates the grade of the stainless steel, L means low carbon content, and 16 signifies the type of coating and suitable welding position.
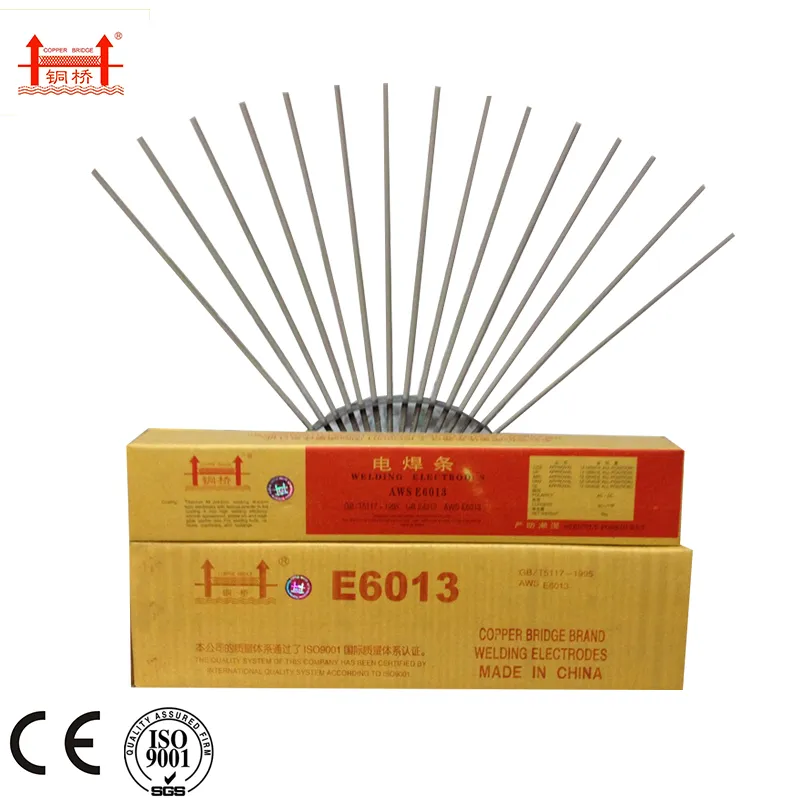
For heavy-duty industrial applications where high corrosion resistance is paramount, the E316L-16 rod may be the appropriate choice. This type of rod is composed of molybdenum-bearing austenitic stainless steel, providing enhanced resistance to chloride attack and better performance in high-temperature environments. It holds substantial significance within industries such as oil and gas, where exposure to harsh chemicals is routine.
On the other hand, if you're dealing with welding projects that demand robustness against wear and tear, the E309L-16 rod is another excellent choice.
Notably employed for dissimilar metal welding, this rod shows high tensile strength and robust resistance against thermal shock. Its versatile nature makes it a staple in the automotive and repair industries.
stainless welding rod number
An essential tip for professionals and enthusiasts is to match the rod number with the stainless steel's grade to be welded. Mismatching can lead to potential issues like cracking or corrosion that compromise the weld's integrity. Understanding and matching your materials ensures that your welding project maintains high standards of durability and functionality.
When deciding on the correct stainless welding rod number, personal experience and professional expertise play prominent roles; choosing the right number requires both understanding technical specifications and considering practical applications. If uncertain, consulting with a seasoned welding professional or a metallurgist can offer further insights, enhancing decision accuracy.
With the welding industry advancing in technology and techniques, staying informed about the latest advancements and how they impact the choice of welding rods becomes even more crucial. For welders who prioritize quality and long-term sustainability, dedicating time to understanding the nuances of these rod numbers translates into effective, trustworthy welding processes that deliver on expectations.
In conclusion, navigating the multitude of available stainless welding rod numbers marks a pivotal component of welding excellence. By combining thorough knowledge of the composition, application, and technical specifications with the hands-on experience and industry insights, one can enhance both the reliability and effectiveness of their welding endeavors, thereby fostering a sense of trust and authority within their field.