Delving into the world of welding, one cannot overlook the pivotal role played by low carbon steel electrodes. As a cornerstone of the welding industry, these electrodes offer a blend of strength, flexibility, and economic feasibility, making them a preferred choice for varied applications. Their renowned utility stems from a robust combination of chemical and mechanical properties tailored specifically for low carbon steel.
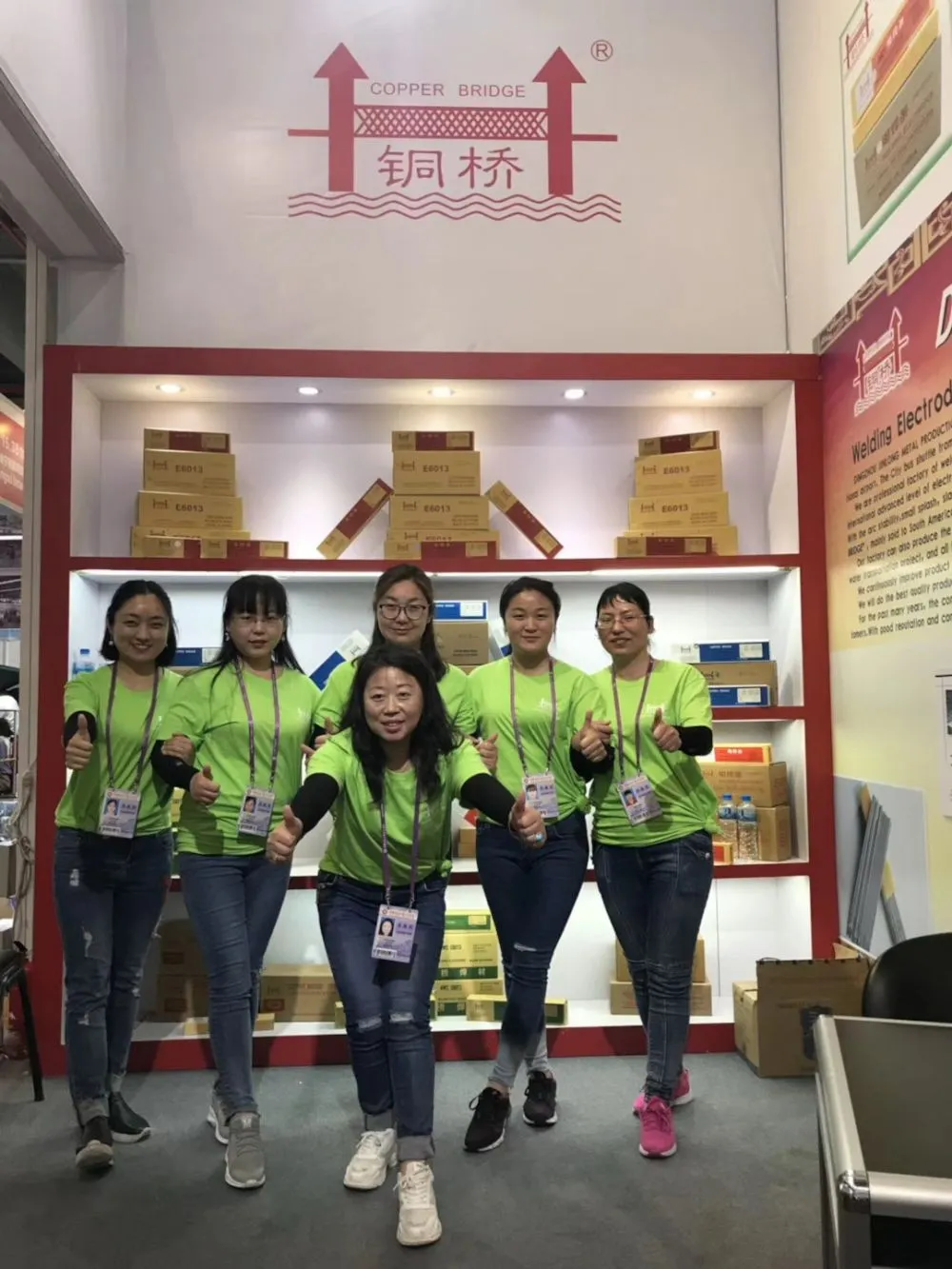
The primary advantage of low carbon steel electrodes is their suitability for creating strong and durable welds. The low carbon content ensures that the resultant welds exhibit superior toughness and ductility, essential for structures requiring high impact resistance and flexibility under stress. Professionals in construction and automotive sectors frequently leverage these electrodes to achieve optimal performance in their projects.
Given that low carbon steel is ubiquitous in these industries, having the right electrode is crucial for ensuring structural integrity and longevity.
Technical expertise in using low carbon steel electrodes can significantly impact the quality of the welds. It’s important to consider factors such as the electrode’s diameter, coating, and the welding position. For instance, selecting the appropriate diameter can influence the penetration and strength of the weld. Experienced welders often choose a slightly larger diameter for thick materials to ensure deeper penetration and a smaller diameter for thin materials to prevent burn-through.
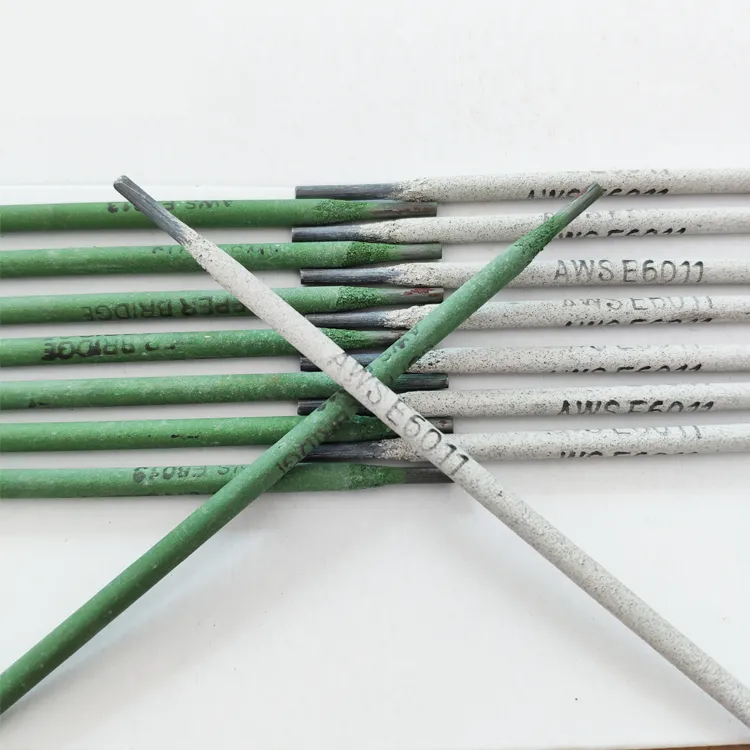
To further enhance reliability and performance, it is essential to match the electrode with the right type of power supply and settings. AC or DC power might be chosen based on the specific requirements of the project, and variables such as voltage and amperage should be meticulously adjusted. This meticulousness underscores the expertise required to wield these electrodes effectively, emphasizing the importance of both theoretical knowledge and practical skills in welding processes.
low carbon steel electrode
From an authoritative standpoint, low carbon steel electrodes stand compliant with various industry standards and certifications that vouch for their quality and safety. Standards such as those from the American Welding Society (AWS) offer guidelines on the appropriate use and handling of these electrodes. Complying with such standards not only assures safety and quality but also builds trust with clients who are reliant on certified professional practices.
Trustworthiness is further cemented by choosing suppliers who provide transparent information about their products. Leading manufacturers often furnish comprehensive details about the composition, tensile strength, yield strength, and elongation of their electrodes. Additionally, the traceability of these products from production to delivery ensures accountability and quality control, factors crucial in large scale operations where reliability is non-negotiable.
Finally, real-world feedback from those engaged in the day-to-day use of these electrodes adds tangible value to their application. Welding experts share that the consistency of arc stability, spatter control, and slag removal attributes significantly affects the operational efficiency. Gathered insights from seasoned professionals present low carbon steel electrodes not merely as consumables, but as integral components that influence workflow and project outcomes.
In conclusion, low carbon steel electrodes are indispensable to various industries owing to their performance-driven characteristics. Their effective use requires an amalgamation of scientific understanding, technical skills, and adherence to industry standards. By fostering confidence through transparency, real-world experience, and maintaining a stringent focus on quality, these electrodes continue to embody reliability and efficacy in every weld they create.