Achieving a successful weld between cast iron and mild steel (MS) is a challenging task that demands expertise and the right choice of welding electrode. Cast iron, known for its brittleness and carbon-rich composition, contrasts sharply with the ductile and low-carbon nature of mild steel. To ensure a strong and durable bond between these materials, specific welding techniques and electrodes must be employed.
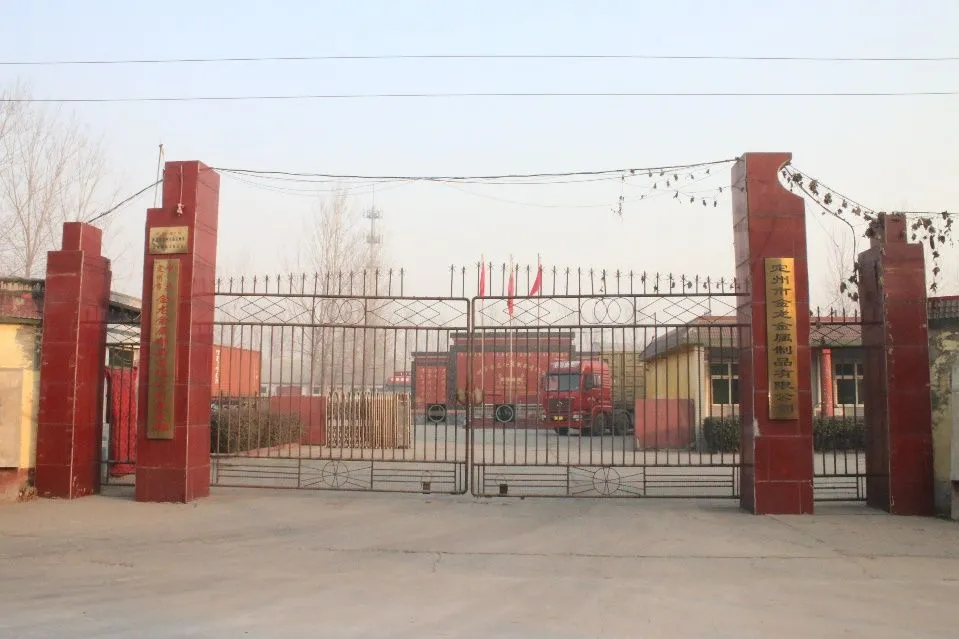
The first step in creating a dependable weld between cast iron and mild steel is selecting the appropriate electrode. Nickel-based electrodes are commonly recommended due to their ability to absorb the thermal expansion differences between the two materials, minimizing the risk of cracking. Nickel 99 electrodes, for instance, are widely acknowledged for their suitability in welding cast iron to steel, as they create a softer and more malleable weld.
Before starting the welding process, it's imperative to prepare the surfaces meticulously. Clean the weld area thoroughly to remove any impurities such as oil, grease, or rust, as these can significantly undermine the weld quality. Proper surface preparation ensures the electrode can melt and fuse the materials effectively, which is particularly crucial given cast iron's propensity to develop surface contaminants.
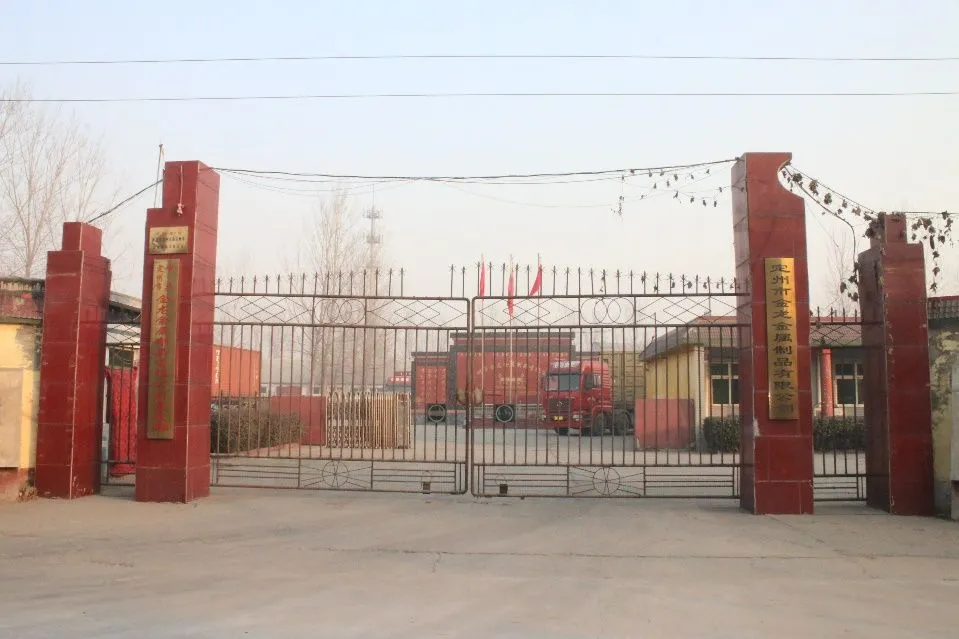
Preheating the cast iron component is another fundamental step in the welding process. Preheating reduces the rapid cooling rate and consequent thermal shock, which can lead to cracking. The preheating temperature typically ranges from 250°F to 600°F, depending on the thickness and type of cast iron. This controlled heating balances the temperature gradient across the joint, enhancing the compatibility of cast iron with the milder characteristics of steel.
During the welding process, maintaining a slow and controlled speed is essential. Rapid welding often induces excessive thermal stress, which can cause casting defects. Utilize a short welding arc and apply intermittent weld beads to distribute heat evenly. This technique helps in minimizing thermal distortion and stress concentration, crucial for creating a sturdy and crack-free joint.
cast iron to ms welding electrode
Post-weld heat treatment (PWHT) is another critical element for ensuring the weld integrity between cast iron and mild steel. Allow the welded joint to cool down slowly by covering it with a heat-retentive material to avoid drastic temperature fluctuations. This method prevents the development of hard and brittle microstructures within the weld area, which can jeopardize the longevity and strength of the bond.
In practice, the key to successfully welding cast iron to mild steel lies in understanding the distinct material properties and carefully managing the heat input throughout the process. Each material's unique characteristics dictate the necessity for specialized techniques and electrodes designed to accommodate these differences.
For engineers and welders, staying informed about the latest developments and case studies in welding technology can significantly aid in enhancing their craft. Joining professional welding associations, attending workshops, and engaging with online forums dedicated to welding technology provide invaluable resources for gaining insights and exchanging experiences with peers.
By mastering the intricacies of welding cast iron to mild steel, technical professionals can expand their skill set, enhance their project outcomes, and ensure the successful implementation of their work. Trust in expertise, experience, and the continuous pursuit of knowledge is paramount in overcoming the challenges presented by welding dissimilar materials.