In the world of welding, especially when working with electrodes like the 1/8 7018, understanding amperage is crucial. This electrode is revered for its versatility and ability to produce high-quality welds across a range of applications. To leverage its full potential, a welder must appreciate the intricacies of amperage settings and their impact on the welding process.
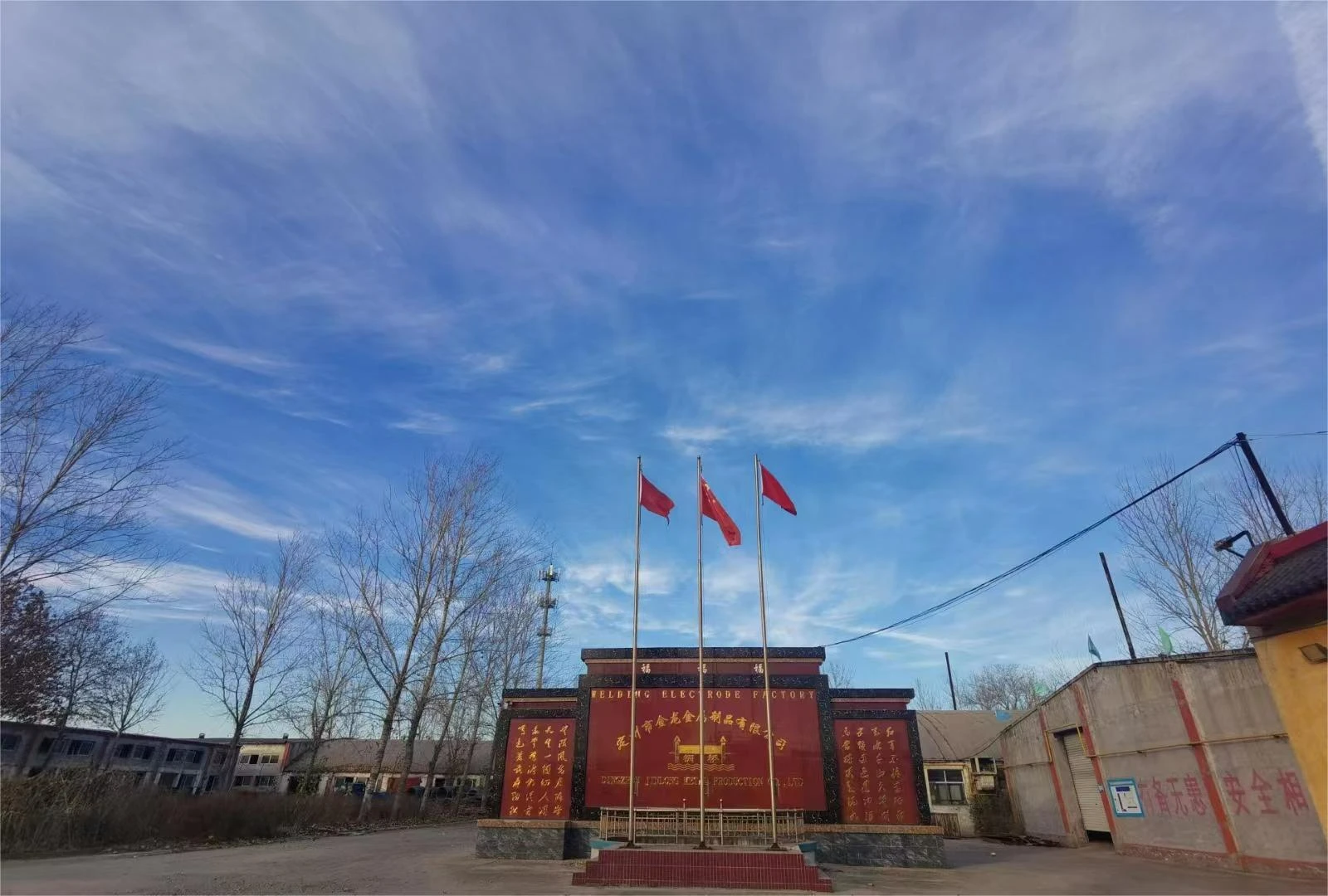
The 7018 electrode is commonly used because it offers a smooth arc, minimal spatter, and excellent weld strength. It is a low-hydrogen rod with an iron powder coating, which makes it ideal for jobs requiring critical welds on structural steel. However, achieving optimal performance with this electrode depends significantly on setting the correct amperage.
For a 1/8 7018 electrode, the recommended amperage range typically falls between 90 and 160 amps. This range is not arbitrary—it's derived from the electrode's composition, coating, and core material, all of which affect how it behaves electrically. Using too low an amperage may result in a weak arc that struggles to penetrate the metal, while too high an amperage can cause excessive spatter and burn-through, compromising the weld's integrity.
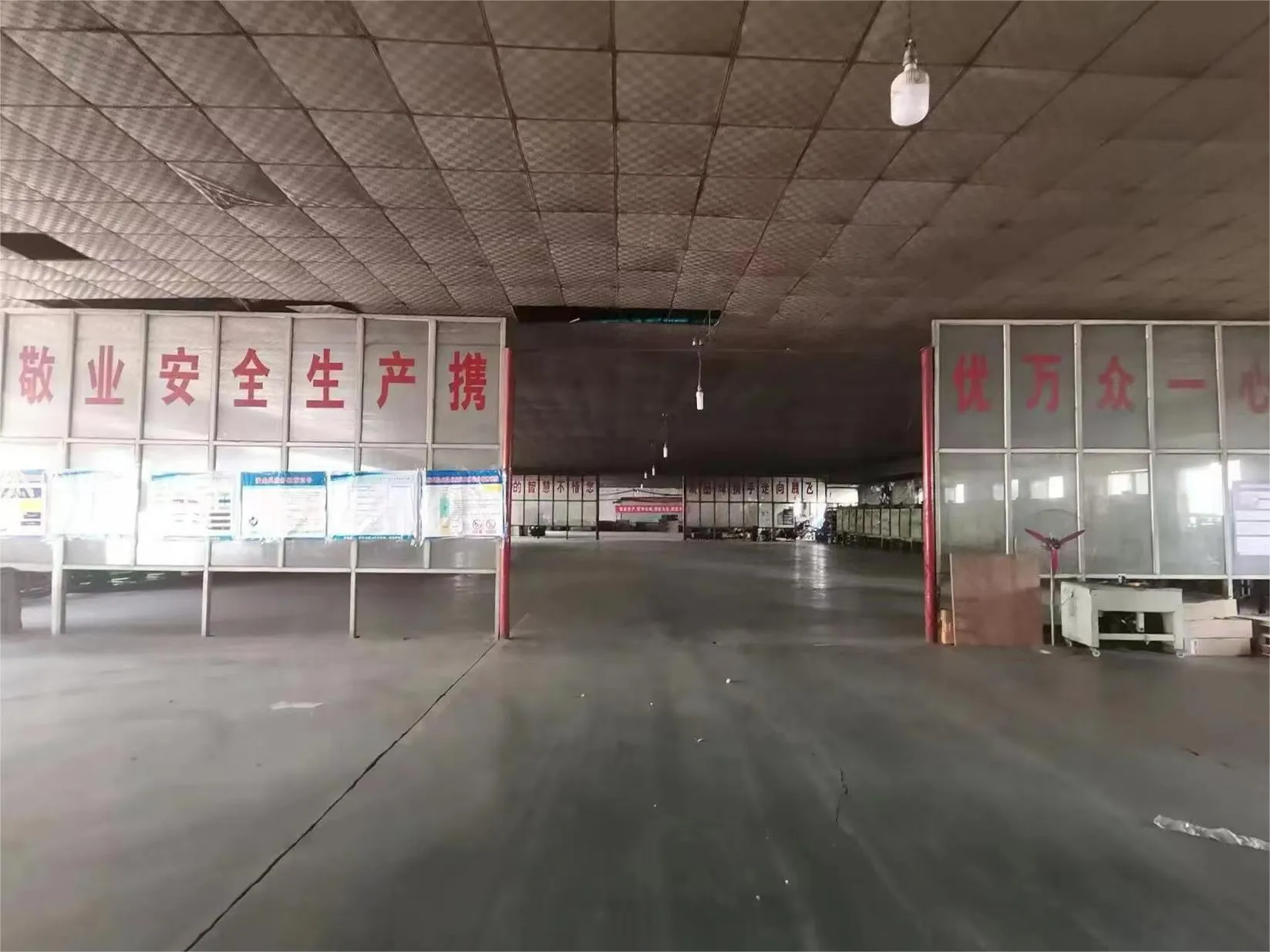
When setting amperage for the 7018, a welder must consider several variables
1. Material Thickness Thicker materials require higher amperage to ensure adequate penetration, while thinner materials necessitate a more controlled, reduced amperage to avoid damaging the workpiece.
2. Welding Position Different welding positions—flat, horizontal, vertical, or overhead—may demand adjustments in amperage levels. For instance, vertical welding typically calls for slightly lower amperage to counteract gravity pulling the molten weld pool downward.
3. Power Supply Whether AC or DC power is being used can impact amperage settings. The 7018 electrode is known to perform well on both AC and DC currents, but slight adjustments may be needed to optimize arc stability.
amperage for 1 8 7018
4. Joint Design The configuration of the joint also plays a role. Open joints may require a higher amperage for full penetration, whereas tight or closed joints might need less to control the weld pool effectively.
5. Environment Conditions such as wind, ambient temperature, and humidity can influence welding performance. External variables might necessitate slight tweaks in amperage to maintain arc consistency and quality.
The experience of the welder combined with these considerations ultimately dictates the ideal amperage setting. It's not just about sticking to a number within the recommended range, but about understanding how different factors interact to achieve the desired weld quality.
Expert welders often emphasize the importance of fine-tuning amperage based on empirical observations over strict adherence to guidelines. Conducting test welds on scrap material similar to the job at hand is a practical approach to determining the most effective amperage. Attention should be paid to the arc behavior, bead appearance, and penetration to achieve a deep, uniform weld with minimal defects.
Authoritative organizations like the American Welding Society (AWS) provide comprehensive guidelines on electrode specifications and use, which are invaluable resources for welders seeking to bolster their technique and understanding. Following best practices as defined by these bodies establishes credibility and ensures that welding is conducted safely and effectively.
Trustworthiness is further cemented by adhering to manufacturer specifications for electrodes, as deviation can lead to suboptimal performance and safety hazards. Reputable manufacturers provide detailed instructions for their products, including ideal amperage ranges, which serve as a foundation for successful welding operations.
In conclusion, mastering amperage settings for the 1/8 7018 electrode is a blend of science and art. It requires technical knowledge, hands-on experience, and adherence to best practices. When these elements come together, the result is a robust, dependable weld capable of meeting the demands of diverse applications across industries.