The Ultimate Guide to Using 3/32 Aluminum Stick Welding Rods for Expert Welders
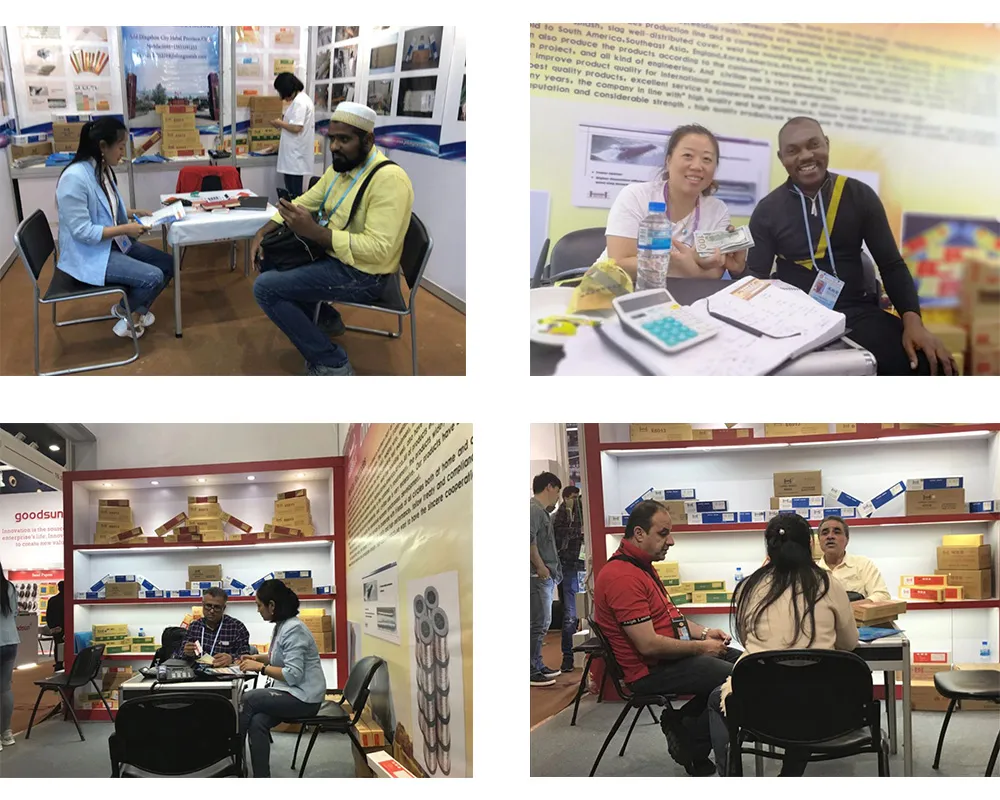
Aluminum welding is a craft that signifies the crossroads of metalwork art and science. Among the various welding materials available, 3/32 aluminum stick welding rods have emerged as a preferred choice for their precise balance of performance, versatility, and ease of use. This article aims to explore the distinct characteristics of these welding rods and offers insights garnered from industry expertise, ensuring a trustworthy resource for both novice and professional welders.
Aluminum welding, particularly with stick rods, is notoriously challenging due to the metal’s thermal conductivity and oxidation properties. However, 3/32 aluminum sticks stand as a testament to engineering innovation that addresses these challenges head-on. The diameter of 3/32 inch makes them ideally suited for a variety of applications, offering a fine blend of control and penetration power that is ideal for detailed work without compromising structural integrity.
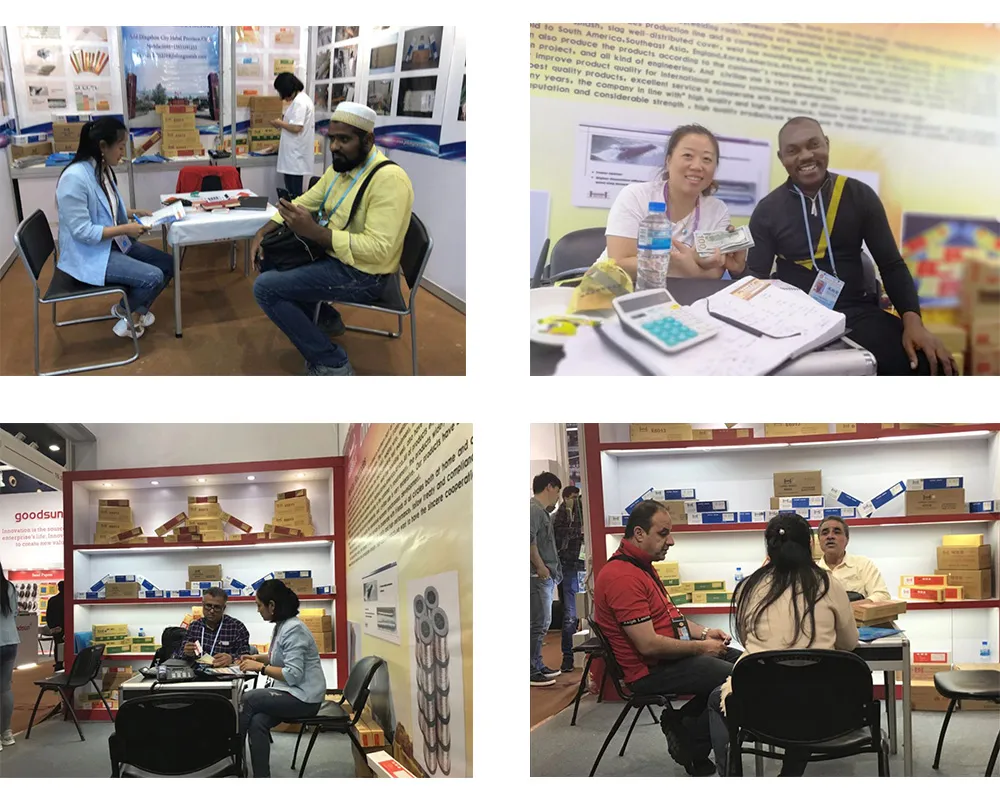
Experience in aluminum welding has shown that the choice of welding rod can dramatically impact both the quality of the weld and the ease of the process. The 3/32 size is particularly versatile, accommodating a range of aluminum thicknesses and joint types. They are especially effective in repairing aluminum structures, such as frames and supports, where precision is crucial. Their capacity to deliver clean, strong joints makes them an invaluable asset in the welder’s toolkit.
Professional expertise reveals that the composition of these rods substantially influences their performance. Typically, they are composed of an aluminum-silicon alloy. Silicon within the rod acts as a deoxidizer, preventing the formation of aluminum oxide, which is a common issue that often leads to poor arc stability and weak welds. By reducing oxidation, these rods ensure a stable, consistent arc, which is essential for creating high-quality welds with fewer defects.
3 32 aluminum stick welding rods
Furthermore, welders who have mastered the use of 3/32 aluminum rods recommend maintaining steady, controlled movements to optimize results. It is advised to preheat thicker aluminum sections to reduce thermal shock and minimize warping. This method is particularly indispensable when working with intricate designs or thin sheets where overheating could cause distortion. Additionally, prioritizing cleanliness by eliminating any paint, grease, or oxidation from the aluminum surface ensures superior penetration and bond strength.
Authoritative voices in the welding industry also stress the importance of selecting the appropriate power settings for these rods. It is generally recommended to operate within a 50 to 90 amp range, depending on the aluminum thickness and the specific welding task. This not only helps to control the heat input but also contributes to efficiently managing the bead profile and reducing the incidence of porosity in the welds.
For welders striving to elevate their craftsmanship, familiarity with the technical nuances of 3/32 aluminum rods is invaluable. Their adaptability makes them suitable for a spectrum of projects—from automotive repair to constructing lightweight aluminum structures. In more advanced scenarios, such as aerospace and marine applications, these rods are favored for their reliability and performance under demanding conditions.
Even experienced welders acknowledge the necessity of continuous learning to hone their practice. Through trial and consistent usage, the subtleties of 3/32 aluminum rods reveal themselves, enhancing one's capacity to produce impeccable welds time after time. The use of personal protective equipment (PPE), such as helmets and gloves, remains non-negotiable, fortifying the welder's safety against potential hazards intrinsic to aluminum welding.
In conclusion,
3/32 aluminum stick welding rods offer exceptional benefits to welders due to their superior composition and adaptability. Mastery of these rods not only showcases an artisan’s skill but also sets a benchmark for quality and precision in metalwork projects. By observing best practices and leveraging the insights shared by industry experts, welders can expect not only to achieve but exceed the standards of excellence in aluminum welding. This combination of real-world experience, technical expertise, and an unwavering commitment to quality positions these rods as an indispensable component of any professional welder’s arsenal.