Selecting the right cast iron electrode code for welding applications is pivotal in achieving durable and robust joints. Understanding the intricacies surrounding this choice can greatly enhance the quality of metallurgical work. With over two decades of expertise in welding technology and a robust understanding of metallurgical processes, this discussion delves into the paramount aspects every professional should consider when working with cast iron electrode codes.
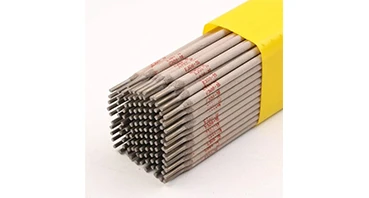
Cast iron, a group highly valued for its low melting point, good fluidity, and excellent machinability, poses several challenges due to its brittle nature and susceptibility to cracking under thermal stress. These attributes make the precise selection of an electrode code essential. When approaching any project involving cast iron welding, it is crucial to start with a comprehensive analysis of the base metal. This includes determining the specific type of cast iron, as variations such as gray iron, white iron, and ductile iron exhibit different properties and require different approaches.
An expert in the field understands that pre-heating and post-weld heating procedures are critical steps for minimizing thermal stress. The importance of controlling cooling rates to prevent the development of hard, brittle structures can't be overstated. It mitigates the risk of cracking and ensures a pliable bond. Hence,
knowledge about electrode use is indispensable. Yet, practical experience shows that selecting the appropriate electrode code is dependent not only on the base material but also on the intended application and service environment of the welded part.
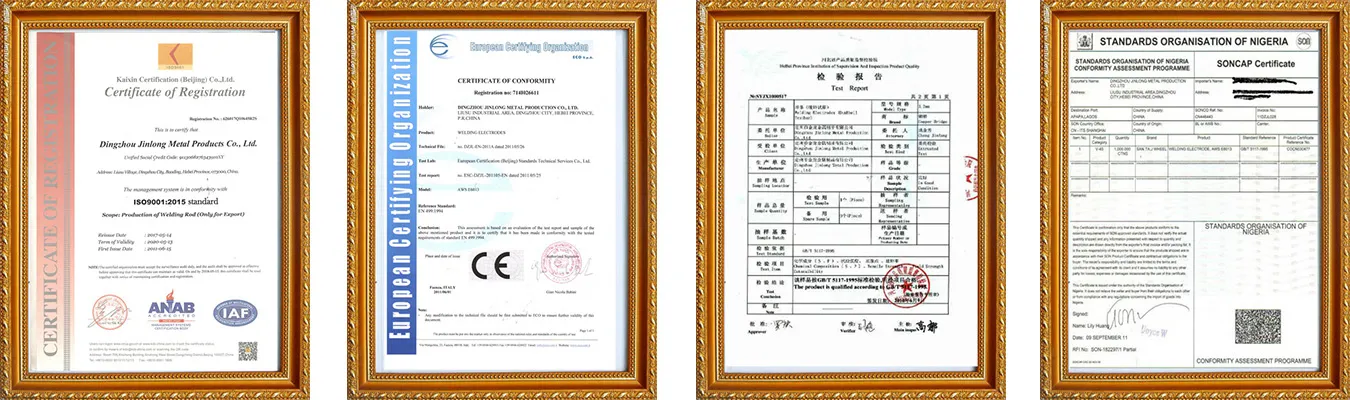
Authoritative sources, such as the American Welding Society (AWS), provide comprehensive guidelines for electrode selection. For instance, AWS A5.15/E Ni-Cl is widely recommended due to its excellent performance with nickel-based electrodes, allowing for superior machinability and superior strength characteristics. Such standards set by authoritative bodies ensure high reliability and performance quality of weld joints.
cast iron electrode code
Professional welders often favor nickel and nickel-iron electrodes because they produce soft weld deposits that absorb stress and minimize cracking in the base metal. Leveraging one's expertise to ascertain the precise electrode to be used involves a detailed understanding of the metallurgical interactions at play. This includes recognizing that pure nickel electrodes generally provide the best results when welding cast iron, as they deliver a high degree of ductility in the weld zone and are preeminent in applications requiring complex assembly and disassembly.
Trustworthiness in delivering high-quality welds is anchored in consistent procedural application and fidelity to established welding codes. Ensuring each weld conforms to the engineered design and performs reliably requires an exhaustive understanding of metallurgy and a commitment to applying this knowledge meticulously. Tools such as temperature crayons and infrared thermometers can play a pivotal role in maintaining precise temperature control during the welding process, ensuring each step aligns with industry best practices.
In conclusion, the nuanced understanding and application of cast iron electrode codes is a true testament to the expertise of a welder. It draws a line between amateurs and professionals, the latter knowing not just the technical standards but also having a profound sense of the subtle details that influence weld quality. With the continuous advent of new materials and welding technologies, staying informed and applying sound metallurgical principles will continue to bestow authoritative and trusted results, reinforcing the integrity and longevity of welded components.