Electrodes have revolutionized various sectors with their versatile applications and unmatched efficiency. The model 7018 electrode, in particular, stands out in the realm of welding, offering unparalleled benefits for both professionals and hobbyists in construction, automotive repairs, and heavy-duty manufacturing. Understanding the broad applications and the specifics of using 7018 electrodes can significantly enhance project outcomes, ensuring both durability and precision.
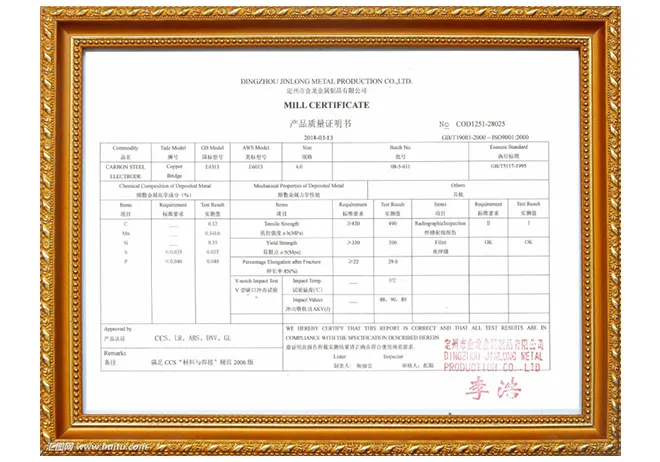
One of the most distinctive features of the 7018 electrode is its low-hydrogen iron powder coating, making it a perfect choice for welding work that demands high tensile strength. This characteristic makes it particularly beneficial for working with low-alloy and high-strength steels. The low-hydrogen content helps prevent hydrogen-induced cracking, a common issue in welds that can lead to structural failures.
Experience has shown that the 7018 electrode excels in creating robust connections that endure high stress and pressure. This is why it is extensively used in constructing bridges, buildings, and pipelines, where safety and reliability are paramount. Professionals have noted that the welds produced with 7018 electrodes exhibit a smooth and aesthetically pleasing appearance, highlighting the electrode's ability to maintain consistency and quality in every weld, even in challenging conditions.
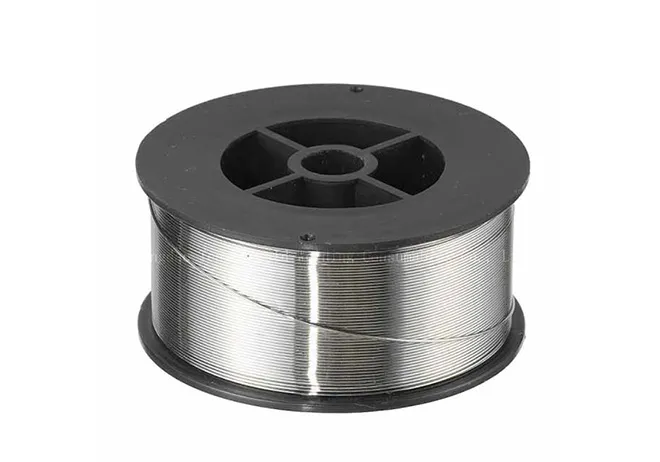
From an expertise standpoint, using the 7018 electrode requires a thorough understanding of its characteristics to optimize results. It's favored not only for its mechanical properties but also for its ease of use with both AC and DC power sources. Welders often recommend preheating thicker materials before welding to ensure deeper penetration and a stronger bond. It's important to maintain the electrode within specific temperature and humidity conditions, often necessitating secure storage in an electrode oven to prevent moisture absorption.
7018 electrode uses
The authoritativeness of the 7018 electrode's applications is backed by numerous certifications and industry standards, including the AWS A5.
1 designation for carbon steel electrodes. These certifications corroborate its performance capabilities, providing assurance to users that they are employing a product that meets rigorous quality and safety benchmarks. Industry professionals trust the 7018 electrode for critical projects precisely because of its proven track record and industry endorsements.
Trustworthiness in using 7018 electrodes is also supported by real-world testimonials from users who consistently achieve superior outcomes. Welders report fewer post-weld treatments and quicker project turnovers, attributing these efficiencies to the electrode's predictable and stable performance. This consistency not only boosts productivity but also enhances the confidence of the stakeholders in the project's long-term viability.
The 7018 electrode is not without challenges; maintaining the correct angle and travel speed is crucial to prevent defects such as slag inclusions or porosity. Training and practical experience are invaluable for mastering these techniques. Welding schools and professional courses often include modules dedicated to the effective use of 7018 electrodes, emphasizing their importance in the welding industry.
Overall, the 7018 electrode remains a pillar in welding operations across diverse industries. Its user-friendly nature, combined with superior mechanical properties, makes it an indispensable tool for achieving demanding standards and robust welds. For large-scale infrastructure projects or small personal endeavors, this electrode delivers exceptional reliability and performance, underscoring its reputation as a staple in any welder's toolkit. With ongoing advancements in electrode technology, the future promises even more innovations that will build on the established success of the 7018 electrode, continuing its legacy of excellence and trust.