When facing the challenge of welding stainless steel to mild steel, selecting the right filler rod is crucial for a successful and durable joint. This topic often perplexes both novice and seasoned welders due to the contrasting properties of these metals. However, understanding the nuances of material compatibility, proper rod selection, and technique can significantly impact the outcome.
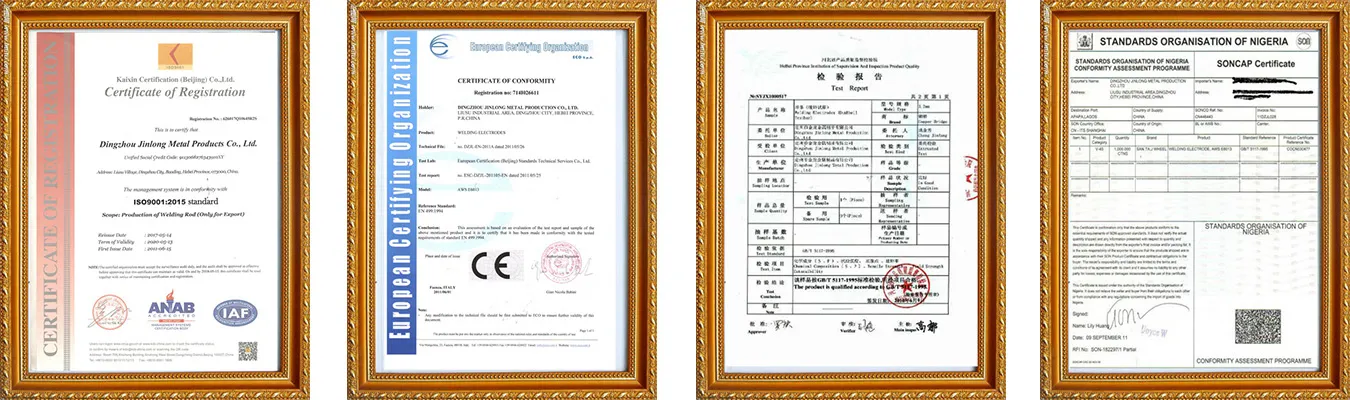
A critical component in joining dissimilar metals such as stainless steel and mild steel is choosing an appropriate filler rod. The common recommendation among welding professionals is an ER309L stainless steel filler rod. This rod is particularly favored because it contains a higher percentage of chromium and nickel, which helps in creating a stable austenitic structure. This stability is essential to prevent cracking and ensure a strong, corrosion-resistant bond.
One of the primary reasons ER309L is a preferred choice is due to its versatility. The inherent properties of ER309L make it resistant to oxidation and scaling at high temperatures, which is essential when welding stainless steel. Furthermore,
it provides a good compromise between the differing expansion rates and thermal conductivities of stainless steel and mild steel. This compatibility reduces the risk of weld defects and ensures a clean, strong joint.
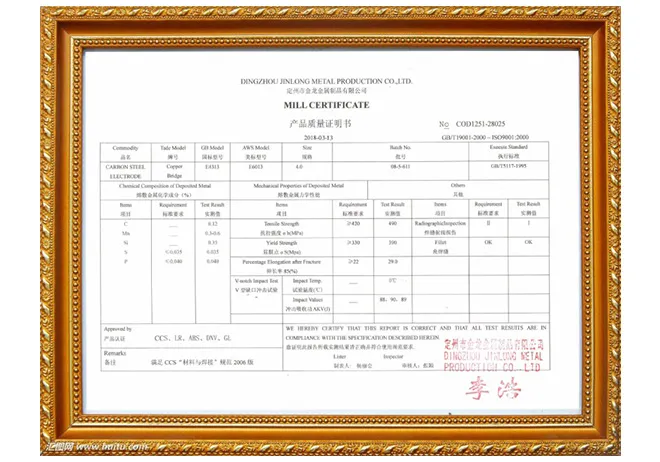
Expert welders emphasize the importance of preparation to maximize the effectiveness of the filler rod. Cleanliness is the first step; both surfaces should be free of contaminants such as oil, dirt, and rust. Contaminants can lead to porosity, weakening the weld joint. Additionally, setting the correct welding parameters tailored to the ER309L filler is essential. The recommended procedures usually involve lower heat inputs to minimize thermal distortion and reduce the risk of defects such as hot cracking.
A common piece of advice from experienced welders is to maintain a steady hand and consistent travel speed during the process. Given the differing melting points of stainless and mild steel, uniformity in technique helps in achieving an even bead appearance and thorough fusion of the metals. The bead should have a smooth transition that gradually bridges the two different materials, a sign of a successful weld.
filler rod for stainless to mild steel
Safety is another aspect where expertise can't be overstated. Proper personal protective equipment (PPE) is non-negotiable when working with these materials, especially since the alloying elements in stainless steel, such as chromium, can produce hazardous fumes. A well-ventilated area or proper exhaust system is essential to protect the welder from potential health risks.
In terms of quality control, post-weld inspection is critical, particularly for projects requiring high strength and durability. Visual inspections should look for surface defects such as cracks, while more advanced techniques like radiographic or ultrasonic testing can detect subsurface flaws. These inspections are vital to ensure the integrity of the weld and the overall structure it supports.
Trustworthiness in completed welds between stainless and mild steel is seen not just in immediate results but in long-term performance. With the right filler rod, preparation, and technique, these joints can withstand the rigors of time and application-specific conditions. Successfully mastering this welding process can lead to greater projects, ensuring that the blend of stainless steel's resilience and mild steel's versatility is effectively utilized.
Ultimately, welding stainless steel to mild steel with the correct filler rod such as ER309L is not just about technical execution but also about understanding the underlying materials science. It demands a balance of experience, expertise, and attention to detail to produce welds that are not only strong but dependable in their intended application.