When it comes to joining stainless steel, selecting the proper welding rod is crucial for achieving durable and corrosion-resistant welds. Understanding the interplay between metals, the types of fillers, and the factors influencing rod selection forms the backbone of successful stainless steel welding. This in-depth exploration of welding rods for stainless steel highlights the expertise and authoritative insights needed for your welding endeavors.
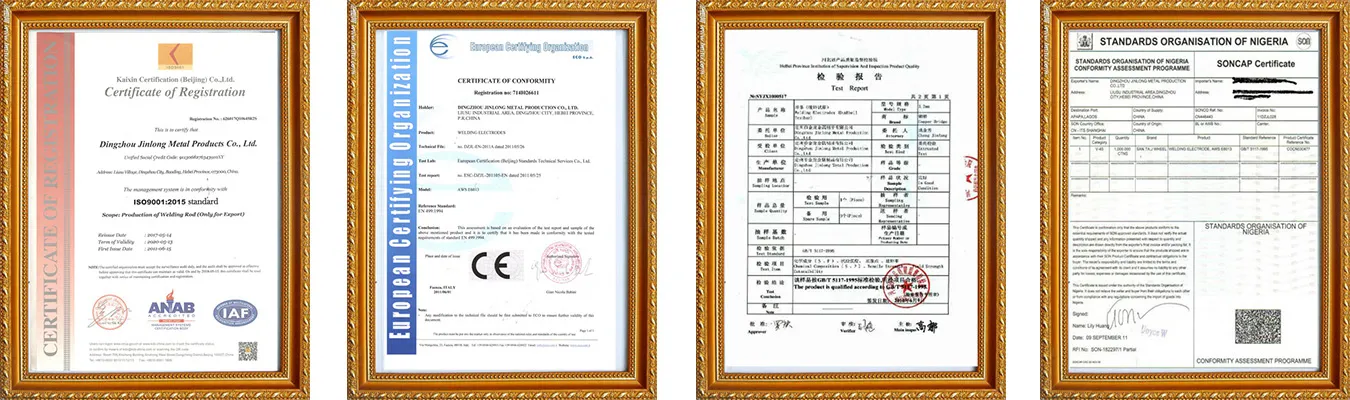
Welding stainless steel requires an appreciation of its distinctive properties such as chromium content, which provides resistance to rust and staining. Among the various welding processes, Shielded Metal Arc Welding (SMAW), TIG (Tungsten Inert Gas), and MIG (Metal Inert Gas) are the predominant methods for stainless steel applications. The welding rod, often referred to as filler metal, acts as the binding agent that ensures the welded parts together maintain their integrity under stress.
A paramount consideration is the compatibility between the base metal and the filler metal. Stainless steels are categorized into three main types austenitic, ferritic, and martensitic, each with unique requirements. Among these, austenitic stainless steel is the most prevalent in industrial applications, and it is crucial to select a rod that matches or surpasses the chromium and nickel content to prevent weld decay.
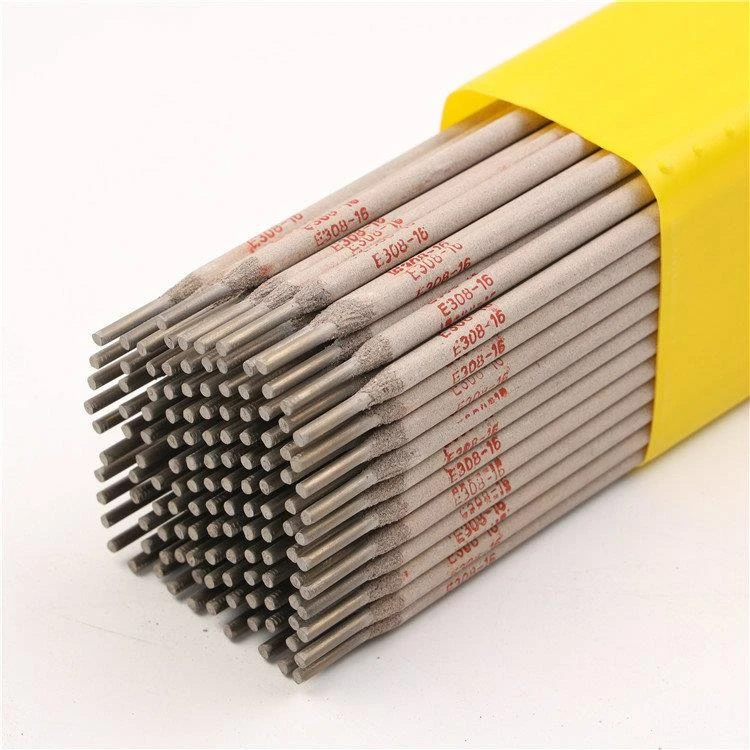
For austenitic stainless steels, E308L, E309L, and E316L rods are frequently chosen. The L in these rods denotes low carbon content which minimizes carbide precipitation, thereby preserving corrosion resistance in the weld zone. The E308L rod is typically used for welding 304 stainless steel, the most widely used stainless, providing good corrosion resistance and strength. Meanwhile, E309L and E316L rods are preferred for joining dissimilar metals or when enhanced resistance to chemical corrosion is required.
Welders working with ferritic stainless steels should consider E430 and E439 rods, offering excellent resistance to stress-corrosion cracking and higher thermal conductivity, although the latter presenting superior weldability.
When addressing martensitic stainless steel, it is essential to preheat and post-heat treat the material to avoid cracking due to its high hardenability. E410 and E420 rods are common choices that maintain the required hardness and wear resistance after heating.
what welding rod is used for stainless steel
An often overlooked but critical aspect is the environment in which the welding will occur. Special coatings on welding rods help stabilize the arc and protect the molten metal from becoming contaminated by air and moisture, making them suitable for welding in less than ideal settings, such as outdoors or in damp environments.
Storage and handling of welding rods greatly affect the welding quality too. Exposure to moisture can lead to hydrogen entrapment within the weld, resulting in porosity or cracking. Proper storage conditions, typically a dry and controlled environment, preserve the rods' integrity.
An authoritative choice of welding rods for stainless steel does not rest solely on the types of metals and their properties but also extends to user expertise and the operational setting. Expert welders understand how factors like amperage, voltage, and travel speed can influence the quality of the weld. Mastery in these factors equates to superior bead appearance, sound fusion, and enhanced overall strength of the weld.
Learnings from experienced welders reveal that the cleanliness of the welding zone is paramount. Any contamination from oils, paints, dust, or surface oxides can compromise the quality and aesthetics of the weld. Practices such as grinding the work surface and using chemical cleaners can help eliminate these contaminants.
Finally, welding is as much an art as it is science, where a welder's skill is matched by their understanding of materials and their interactions. Building trustworthiness in stainless steel welding extends beyond knowledge of materials to include meticulous technique, attention to safety protocols, and continuous learning from each project.
Embarking on stainless steel welding demands comprehensive knowledge and practical wisdom. By selecting the appropriate welding rod and committing to quality techniques and conditions, welders can achieve joints that not only meet specifications but offer longevity and resilience, incorporating the critical elements of experience, expertise, authority, and trust.