Selecting the right welding rod is crucial in ensuring durable and high-quality welds. Not only does a good welding rod facilitate the fusion of metals, but it also impacts the strength and durability of the joint. Through extensive experience and expertise in the welding industry, we offer insights into choosing the best welding rods for different applications.
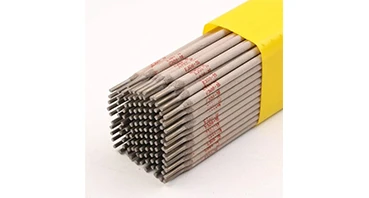
Welding rods, also known as filler metals, are available in various types and strengths, each suited to specific materials and welding techniques. One critical aspect of choosing a welding rod is understanding the material compatibility. The most common welding rods include E6010, E6011, E6013, E7018, and E7024, each designated for distinct tasks.
Take the E6010 welding rod, for example. It is renowned for deep penetration welding, making it ideal for pipeline and root pass welds in carbon steel. Its fast-freeze characteristic allows welders to create strong bonds even on unclean or rusted surfaces. However, mastering E6010 requires skill due to its quick-setting nature, which demands precise control to avoid defects like slag inclusions and undercuts.
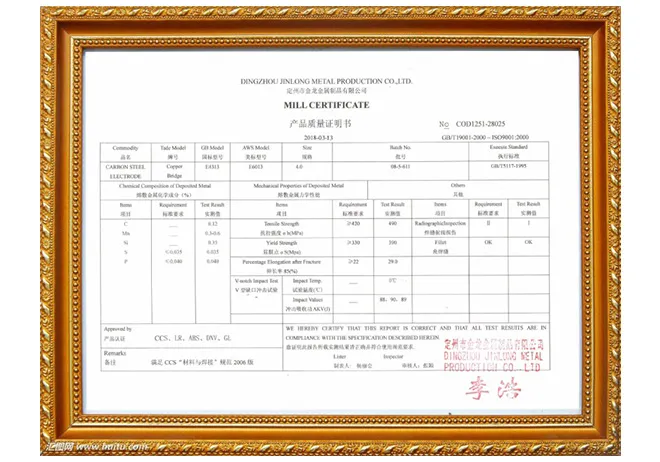
E7018, on the other hand, is a low-hydrogen rod known for producing clean and smooth welds with minimal spatter. Its versatility and strength make it a favorite in structural welding and industries requiring high integrity welds. Although more forgiving than E6010, it requires proper storage in moisture-free environments to prevent hydrogen-induced cracking.
For those new to welding or pursuing hobby projects, the E6013 rod serves as an excellent starting point. It’s known for its ease of use, producing neat and aesthetic welds with minimal practice. Suitable for a wide range of mild steel applications, it’s highly sought after for its versatility.
good welding rods
An undeniable component of welding rod selection is understanding the welding position requirements. Certain rods are optimized for specific positions, such as flat, horizontal, vertical, or overhead. For instance, the E6011 rod is adept at handling all-position welding, making it a versatile choice that accommodates varying project needs.
Expertise in welding rod selection also involves consideration of welding machinery and power supply. Some rods require specific current types, such as AC or DC, which not only influences the welding technique but also the final weld quality. For example, E7018 rods thrive on DC currents but perform adequately on AC with appropriate calibration.
Trust is built by relying on welding rods that deliver consistent performance and longevity. Leading manufacturers who prioritize quality control and stringent testing protocols are often the trustworthy choice for any welder seeking reliability and safety. Brands like Lincoln Electric, ESAB, and Hobart are lauded for their commitment to crafting rods that meet industry standards and perform exceptionally in various welding endeavors.
As technology evolves, innovations in welding rods continue to emerge, with manufacturers investing in advanced materials and coatings that enhance performance and reduce post-weld processing time.
For anyone delving into the world of welding or seeking to refine their craft, knowing and selecting the appropriate rod type is more than half the battle. By understanding the properties, applications, and requirements of different welding rods, professionals and enthusiasts alike can achieve high-quality results that stand the test of time.