Selecting the ideal filler rod for stainless steel welding is a crucial step towards ensuring superior weld quality and structural integrity. When it comes to welding stainless steel, versatility, corrosion resistance, and overall strength are paramount considerations. This article delves into the essential factors to consider when choosing a filler rod, backed by expert advice, and real-world experiences, enhancing your understanding of optimal welding practices.
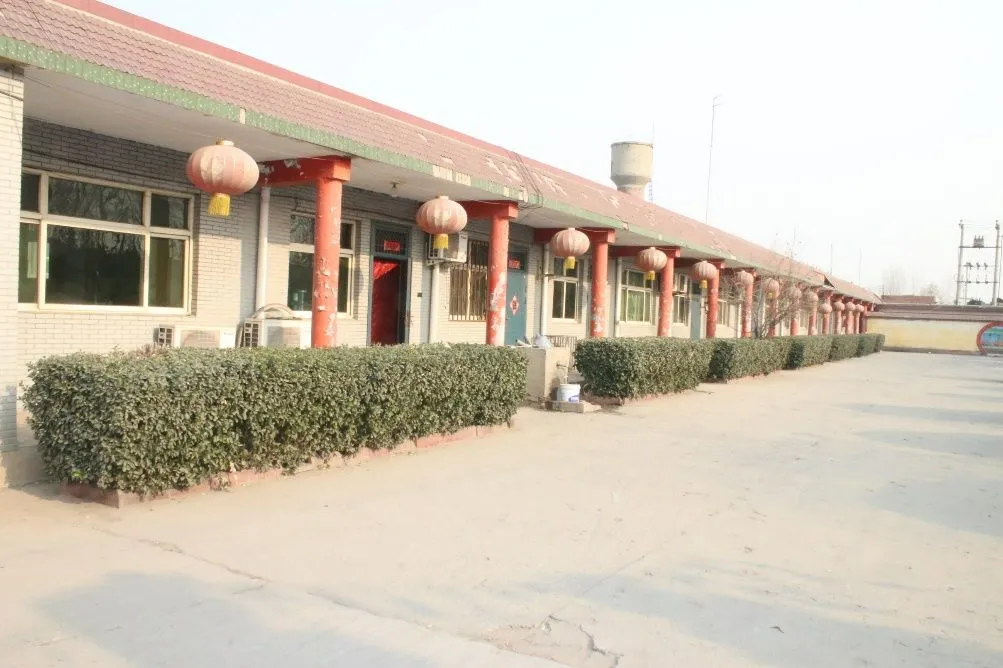
Stainless steel, renowned for its durability and resistance to corrosion and heat, poses its unique set of challenges during welding. The right filler rod plays a fundamental role in bridging the gaps effectively and ensuring the longevity and functionality of the welded joint. The complexity of the welding process demands a filler rod that not only complements the base metal but also meets specific mechanical properties and desired aesthetic outcomes.
One of the primary considerations when selecting a filler rod for stainless steel is matching the alloy composition. Ideally, the filler rod material should enhance the corrosion resistance properties of the parent material. For instance, 308L is a common choice for welding 304 stainless steel, providing excellent resistance to cracking and austenitic stability. Similarly, 316L rods are preferred for 316 stainless steel, renowned for their molybdenum content which boosts the weld's corrosion resistance against acids.
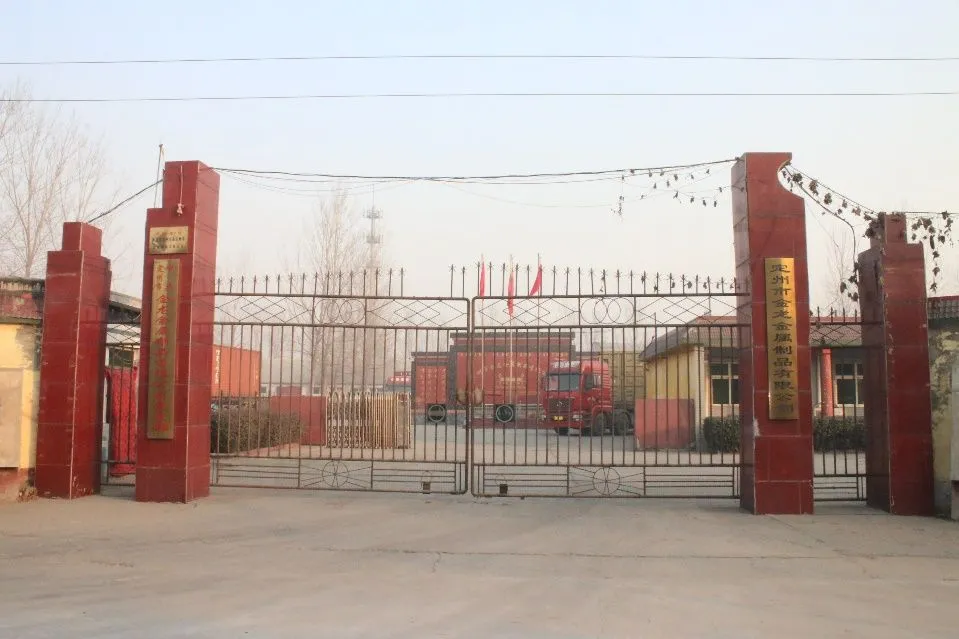
The welding process itself significantly influences the choice of filler rod. For Tungsten Inert Gas (TIG) welding, precision and control are paramount, often necessitating ER308L or ER316L rods to ensure clean, small-diameter welds. On the other hand, for Shielded Metal Arc Welding (SMAW), the versatility of electrodes like E308L-16 provides reliable results. Experts often emphasize the importance of matching the rod diameter to the thickness of the workpiece to maintain weld aesthetics and integrity.
filler rod for stainless steel welding
Temperature management is another critical factor in stainless steel welding. Overheating can cause oxidation and compromise the structural properties of the metal. Experts advise maintaining a steady, controlled heat input by selecting filler rods designed to withstand thermal stresses. Innovation in filler rod manufacturing has introduced variants with added silicon, which aids in improving fluidity and minimizing the risk of porosity. Consult with manufacturers or authoritative sources about the latest advancements in filler rod materials to optimize your welding projects.
Beyond the technical aspects, practical experience highlights the importance of storage and handling of filler rods. Moisture can lead to hydrogen inclusion, which is detrimental to the weld quality. Industry professionals advocate for storing rods in moisture-free environments and verifying the packaging integrity before use. Maintaining a clean workspace and using proper personal protective equipment further contributes to achieving welds that are not only robust but also aesthetically pleasing.
The authoritative insights of seasoned welders underscore that while technical specifications are indispensable, hands-on practice and adapting to specific project demands greatly refine the selection process. Clients or supervisors often value tangible results over theoretical knowledge. High-quality welds enhance the reputation of the welder and provide long-term benefits such as reduced repair costs and enhanced material performance.
In conclusion, the selection of filler rods for stainless steel welding is a nuanced process that integrates expertise, real-world experience, and technical acumen. As advancements continue to emerge in welding technology, staying informed about innovations and aligning them with operational needs can significantly uplift the overall welding process. Trust in the materials, methods, and your meticulous approach will safeguard the success of your stainless steel projects, ensuring lasting durability and satisfaction.