Understanding the precise amperage for welding rods such as the 6011, specifically in the 1/8 inch size, is pivotal to achieving quality welds. This welding rod is renowned among professional welders for its versatility and reliable performance on multiple metals and dirtier surfaces. The amperage setting plays a decisive role in determining the outcome of your welding process, influencing penetration, bead appearance, and overall strength of the weld.
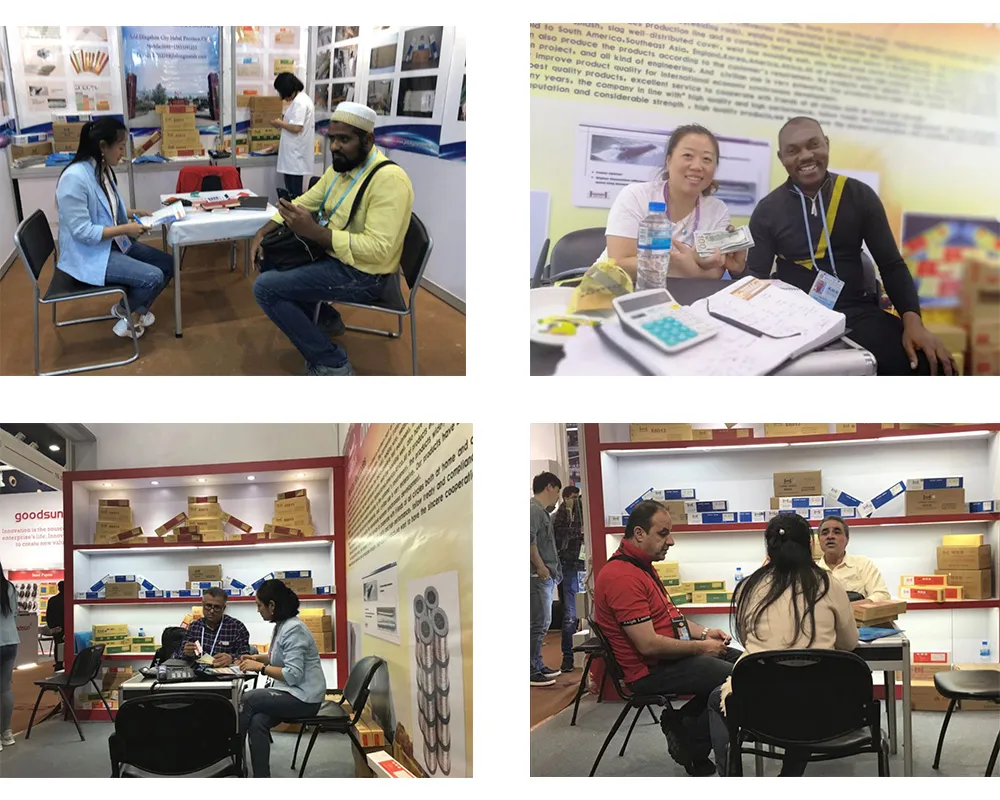
The 6011 welding rod has its distinct place among welding materials due to its cellulose potassium coating, enabling a deep penetrating arc ideal for vertical and overhead positions. The critical focus for welders using 6011 rods in a 1/8 inch size is finding the sweet spot of amperage, typically ranging from 75 to 125 amps.
The experience of using these rods underscores the importance of adjusting the amperage correctly. For thinner metal sheets or pipes, setting the amperage towards the lower end of the range, around 80-90 amps, can prevent burn-through. This is where novice welders can sometimes falter, opting for higher amperage that leads to excessive melting and weakens the joint.
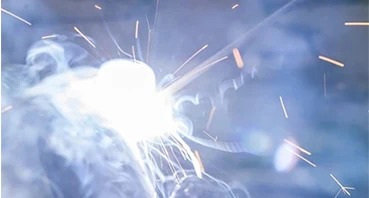
However, when dealing with thicker materials, it's recommended to increase the amperage, approaching 100 to 125 amps. Doing so ensures adequate penetration and a robust weld. Here, the expertise of a seasoned welder shines, as they possess the skill to judge the ideal setting based on joint preparation, material thickness, and position. These nuances in technique reaffirm the significance of having solid foundational knowledge and adjusting settings dynamically based on real-world applications.
In the realm of professional welding, the precision in amperage settings correlates directly with execution quality and equipment efficacy. Reliable welding operations consistently monitor amperage settings using digitally calibrated equipment, ensuring precise adherence to required specifications. This reliance on accurate digital readings establishes a prestigious level of authoritativeness and trust in the quality of workmanship, distinguishing true craftsmen from amateurs.
6011 1 8 welding rod amperage
Welding experts often share insights drawn from decades of practice, emphasizing the use of advanced techniques such as the whip-and-pause motion with 6011 rods. This technique is inherently linked to controlling heat input and allows fine-tuning of the weld pool. The adjustment of amperage is crucial concurrently with this technique, as it helps manage the fluidity of the puddle, particularly demanded in vertical or overhead welds.
Trustworthiness in welding practices is evidenced when industry standards are consistently met, particularly regarding amperage settings for various rods and sizes. Compliance with safety and quality standards, such as those set by the American Welding Society (AWS), not only certifies the weld but also authenticates the welder's proficiency, influencing customer trust positively.
Choosing an appropriate power source, such as an AC/DC welder, impacts the practical applicability of 6011 rods. DC welding often results in a smoother arc and is particularly preferred when precision and control are paramount. Conversely, AC settings are useful for tackling rusted or painted surfaces, a condition where 6011 rods excel, thanks to their excellent cleaning action.
In summary, mastering the amperage settings for 1/8 inch 6011 welding rods is a testament to a welder's expertise and understanding of material science. It combines technical skill, a rigorous understanding of metallurgical behavior, and a methodical approach to equipment settings. This fusion ensures reliable, high-quality results that meet both structural integrity and aesthetic standards, fortifying the welder's reputation for excellence in a competitive field.