In the world of welding, the 6010 welding rod stands out as a staple for many professionals, particularly when it comes to executing high-quality welds that require strong penetration. Navigating the intricacies of welding with a 6010 rod demands an understanding of its characteristics and knowing the precise amperage settings to use, especially when dealing with a 3/32 inch rod.
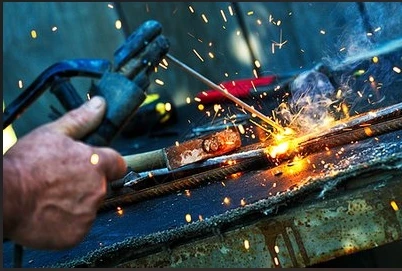
When it comes to 6010 welding rods, their exceptional ability to penetrate deeply into the metals being bonded makes them invaluable for industries that require robust welds, such as in pipeline or heavy-duty construction. This rod is designed for use with direct current (DC) and is known for producing an aggressive arc, which cuts through rust, paint, and dirt, delivering strong and trustworthy welds, even under less-than-ideal conditions.
However, achieving the desired results with a 3/32 inch 6010 welding rod is contingent upon setting the correct amperage, which directly influences the quality of the weld. Typically, the 3/32 inch size operates best within an amperage range of 40 to 85 amps. For instance, working at the lower end, around 40 to 50 amps, proves beneficial when welding thinner materials or when delicacy and precision are paramount. This setting ensures minimal material distortion and prevents burn-through.
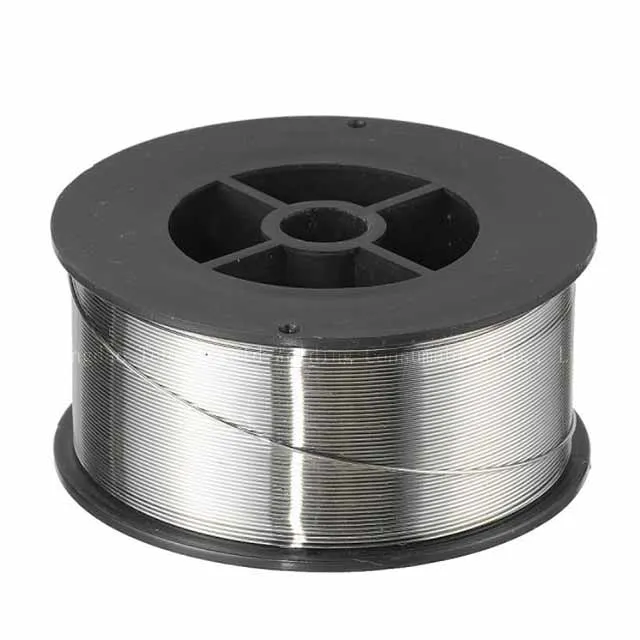
Conversely, dialing up the amperage towards the higher end of the spectrum, such as 75 to 85 amps, is advisable when welding thicker materials. The increased heat facilitates deeper penetration and stronger weld integrity, essential for structural welds requiring enhanced durability. The art of balancing amperage with material thickness is where a welder's expertise truly shines.
Experience is invaluable in this realm. Seasoned welders assert that maintaining a tight arc, typically within an eighth of an inch, is crucial when dealing with 6010 rods. Such precision prevents excessive spatter and promotes a cleaner weld, which not only looks aesthetically pleasing but is structurally reliable. Additionally, proficient welders often employ a whipping or weaving technique to manipulate the arc's movement, ensuring uniformity in bead formation and penetration.
6010 welding rod 3/32 amps
In terms of expertise, understanding the metallurgy of the materials being joined is also essential. Different alloys and compositions react uniquely to heat and filler material. Hence, pre-weld material preparation, including cleaning and beveling, play significant roles in the weld outcome. This reflects an expertise in not just welding, but also material science, showcasing the welder's comprehensive knowledge and skill.
Authority in the field comes from not just practice, but from staying updated with technological advancements and innovations within the welding industry. The introduction of welding machines with adaptable settings for automatic adjustment has revolutionized traditional welding techniques. These machines often come with preset or programmable settings, which suggest optimal amperage ranges based on electrode type and size, further refining the welding process.
Trustworthiness in welding is captured in the quality and durability of the final joint. For projects that demand rigorous safety standards, such as in pipeline welding, adhering to certified procedures and protocols is non-negotiable. This involves complying with guidelines laid out by institutions like the American Welding Society (AWS), which ensures consistent weld quality, safety, and performance.
In conclusion,
mastering the use of a 6010 welding rod with a 3/32 inch diameter goes beyond setting the right amperage. It requires a harmonious blend of technical knowledge, hands-on experience, and an unwavering commitment to quality craftsmanship. By adhering to best practices, leveraging technological advancements, and aligning with established safety standards, welders can consistently produce reliable, high-strength welds that meet the demanding needs of modern industries.