The choice of the right welding rod is crucial for any welder who aims to deliver high-quality, durable, and safe welds. Among the vast array of welding consumables, the 3/32 or 1/8 inch welding rod stands out due to its broad applicability and efficiency in various welding scenarios. This article explores these welding rods by delving into their practical applications, expert recommendations, and factors that underscore their reliability and trustworthiness in welding projects.
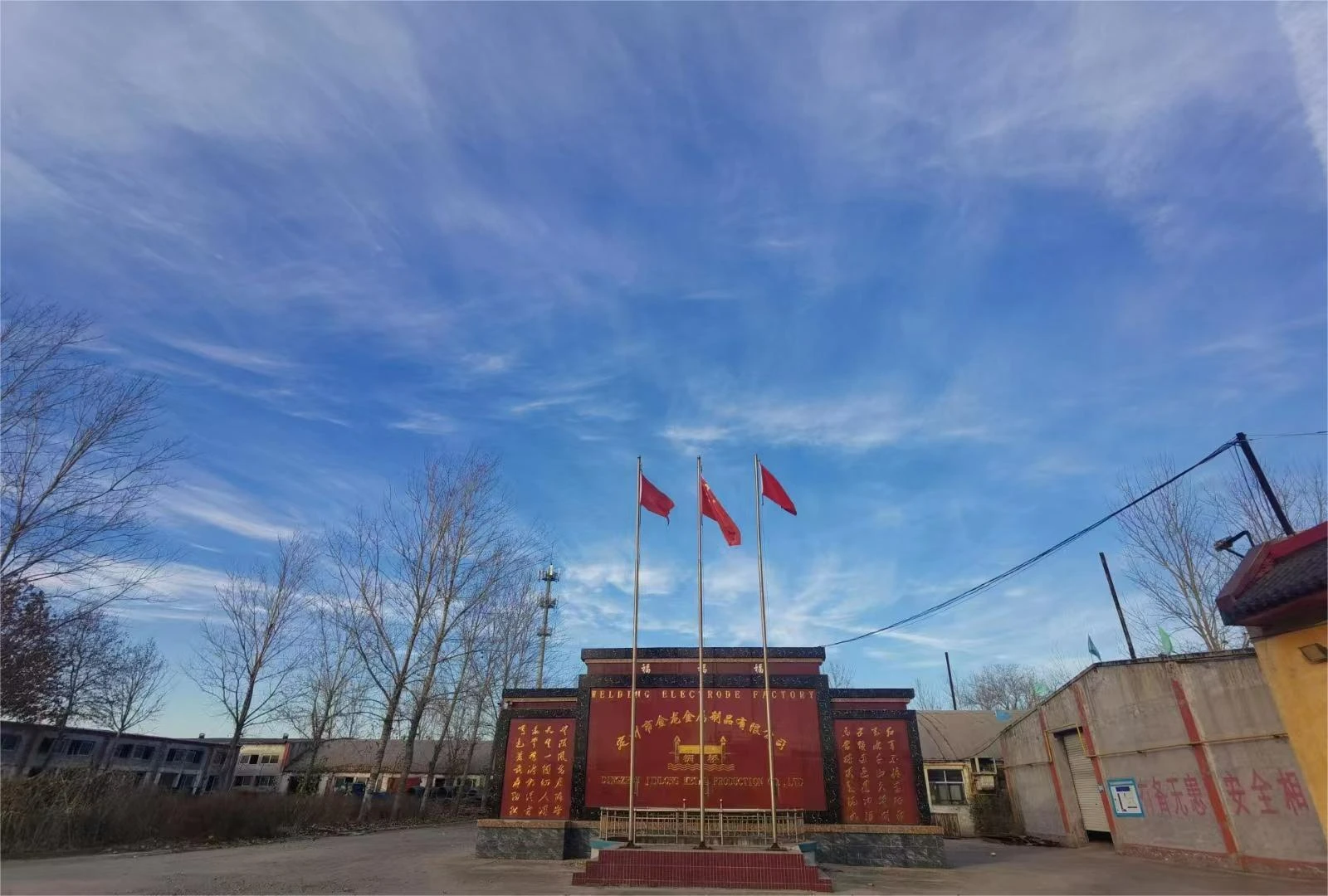
3/32 Welding Rod The Precision Expert
The 3/32 inch welding rod is particularly revered in precision welding tasks. Its smaller diameter makes it an ideal choice for thin metals and delicate welds where control and precision are paramount. Experienced welders often use 3/32 welding rods in scenarios involving thin sheet metal, tubing, and other lightweight materials that could easily warp or melt with more substantial rods.
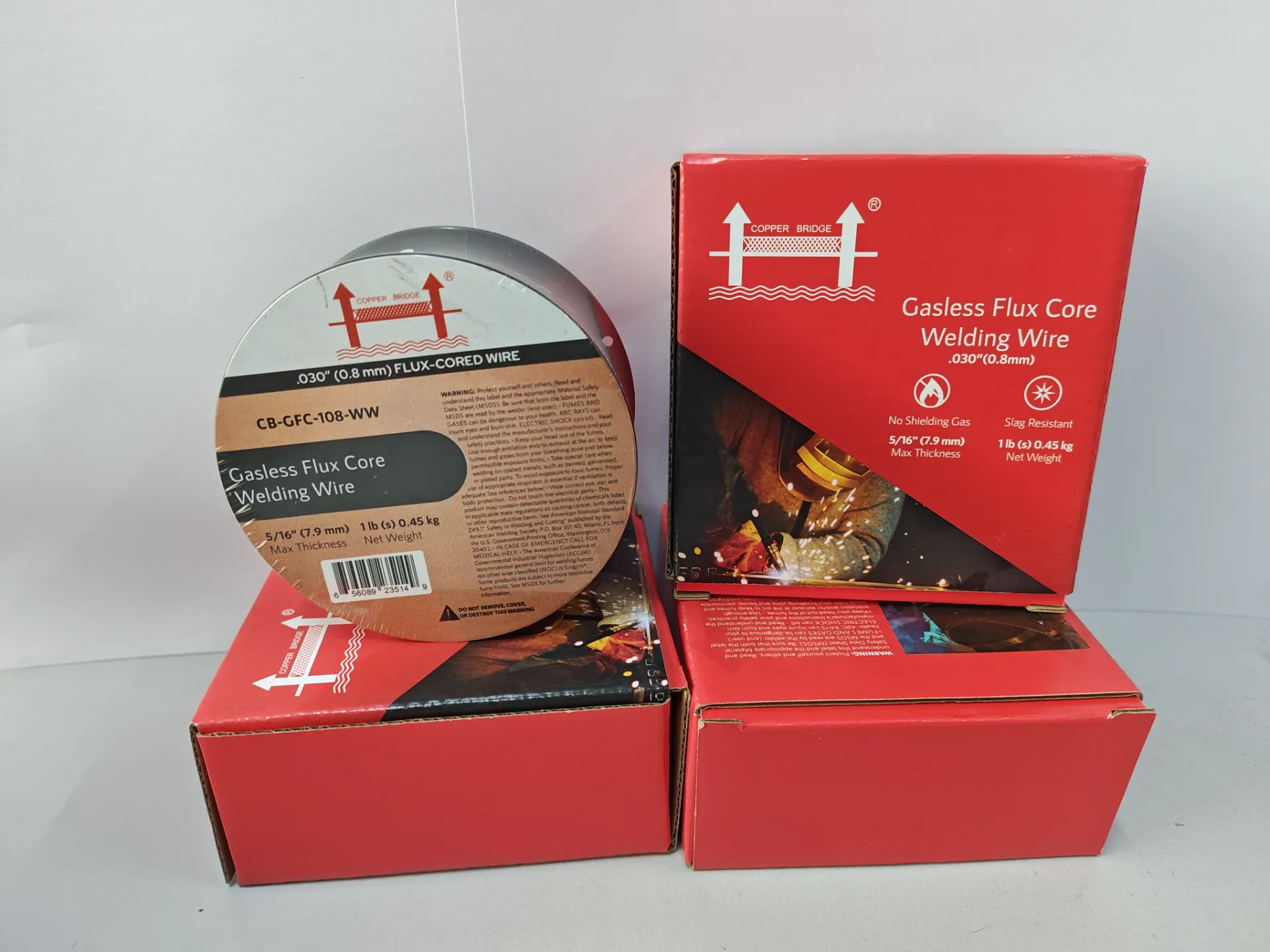
Professional expertise also highlights the adaptability of 3/32 rods. With varying compositions like E6013, E7018, and E308L, these rods are versatile enough to handle different types of metal and welding conditions. For instance, E6013 rods are frequently recommended for beginners due to their smooth arc characteristics and ease of use, while E7018 rods are noted for their low-hydrogen properties, which enhance weld quality and strength in structural projects.
Beyond their application, the trustworthiness of 3/32 welding rods is demonstrated through their consistent performance. Welders with years of experience often express how these rods provide a stable arc and produce minimal spatter, which is crucial in maintaining a clean working environment and reducing post-weld cleanup time. This reputation has been built on years of consistent positive outcomes when used under appropriate conditions.
1/8 Welding Rod The Workhorse
In contrast, the 1/8 inch welding rod is recognized as a workhorse in the welding domain, suitable for both amateur and professional use across a variety of projects. Its thicker diameter allows it to carry higher currents, making it perfect for welding thicker metals and achieving deeper penetration.
From an expert standpoint, 1/8 rods prove indispensable in heavier fabrication tasks, such as those involving rebar, structural beams, and other robust metal components. They are ideal for jobs requiring durability and strength, and are often employed in construction and industrial applications where safety and reliability can't be compromised.
3/32 or 1/8 welding rod
The authority of 1/8 rods is backed by their ability to produce consistent, high-quality welds. Welders with substantial experience often cite these rods for providing excellent bead quality and mechanical strength. The E7018 variant is particularly renowned for its ability to handle high-stress applications, offering excellent ductility and resistance to cracking.
Trust in 1/8 welding rods is further reinforced through industry standards and certifications that ensure these consumables meet stringent safety and quality guidelines. This reliability and assurance make these rods a staple in any welder’s toolkit.
Choosing the Right Rod
When selecting between a 3/32 and a 1/8 welding rod, the decision primarily hinges on the material thickness, welding position, and the specific requirements of the project at hand. Expert welders emphasize the importance of considering these factors to optimize performance and achieve the desired welding outcomes.
For projects involving thin materials or requiring precision, the 3/32 rod provides unparalleled control and finesse. Conversely, for robust applications where strength and penetration are prioritized, the 1/8 rod delivers superior results.
Seasoned professionals often advise new welders to practice and understand the characteristics of each rod size through training and trial runs. This hands-on experience is invaluable, enhancing the welder’s expertise and confidence in handling various welding scenarios effectively.
Conclusion
In the realm of welding, 3/32 and 1/8 inch rods represent two distinct yet essential tools that cater to different facets of welding projects. Their authority and trustworthiness are well-established through decades of successful applications across industries. By recognizing the unique strengths and applications of each rod, welders can enhance their precision, quality, and efficiency, ultimately leading to superior craftsmanship and reliable welds that stand the test of time. In the pursuit of excellence, these rods are invaluable allies, melding professional expertise with trust to deliver outstanding results.