Welding stainless steel (SS) rods has always been a subject of interest for both novice and seasoned welders. Stainless steel's unique properties, including its resistance to rust and high temperature, make it a popular choice in many industries. This article explores the intricacies of welding SS rods, combining personal experience with professional insights to provide a guide that stands out in the crowded space of SEO content.
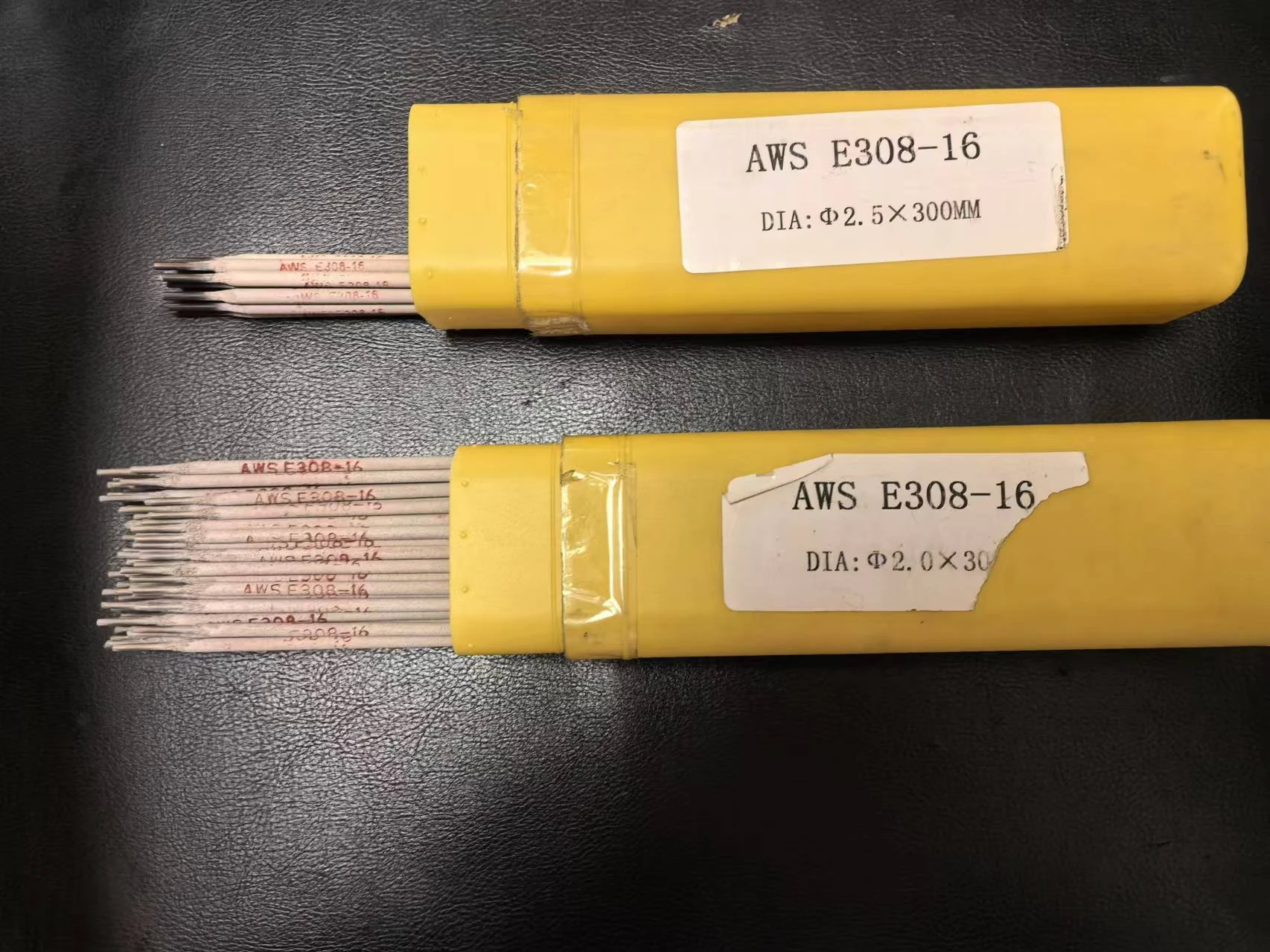
The first step in welding stainless steel rods involves understanding the different types of stainless steel available. The three main categories are austenitic, ferritic, and martensitic, each with distinct characteristics. Austenitic stainless steel is the most common, primarily due to its excellent corrosion resistance and versatility. Ferritic stainless steel, on the other hand, is known for its magnetic properties and lower cost. Martensitic stainless steel is less common but is typically used in applications requiring high strength and hardness.
Preparation is crucial when welding SS rods. Start by cleaning the surface of the rods thoroughly to remove any contaminants such as oil, dirt, or rust that could compromise the weld quality. A clean, dry cloth paired with an alcohol-based cleaner is recommended for best results. It is also advisable to properly align the rods using clamps or fixtures, ensuring precision and a clean weld.
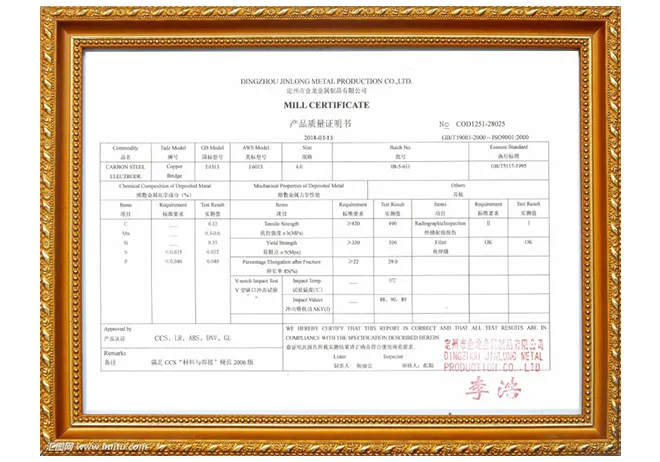
Choosing the right welding method plays a significant role in the outcome of the project. TIG (Tungsten Inert Gas) welding is often preferred for welding stainless steel rods due to its precision and control. It allows for a clean and aesthetically pleasing bead, essential for applications where appearance matters. MIG (Metal Inert Gas) welding is another viable option, favored for its speed and convenience, especially in thicker materials. For those who are not as experienced, stick welding provides a simpler yet effective approach, though it might not achieve the same level of finesse.
One common challenge when welding SS rods is preventing warping and distortion due to heat. Stainless steel's low thermal conductivity means it tends to retain heat in the weld area, potentially leading to issues. To mitigate this, welders should employ a back-stepping technique and alternate welds on the piece to distribute heat evenly. Utilizing chill blocks can also assist in dissipating heat quickly, thus maintaining the integrity of the rods.
welding ss rod
Filler material selection is equally important in achieving a successful weld. The filler rod must be compatible with the base metal to prevent corrosion and cracking. For austenitic stainless steels, a 308 or 309 grade filler is normally recommended. These fillers contain high chromium and nickel content, contributing to the durability and strength of the weld.
In terms of PPE (Personal Protective Equipment), always prioritize safety. Stainless steel welding produces harmful fumes and requires adequate ventilation. Wearing protective clothing, gloves, and face shields is essential to avoid burns and injuries. A respirator designed to filter out metal fumes is also recommended to protect against inhaling hazardous particles.
Understanding the specific application and environment of the final product is essential when performing any welding task with SS rods. Environments with exposure to high chloride concentrations or marine settings demand higher corrosion resistance—a factor to consider when selecting both stainless steel grades and filler materials.
In my years of experience, ensuring weld quality through testing is an often-overlooked step. Conducting non-destructive testing (NDT) such as X-ray or ultrasonic inspection can verify weld integrity, identifying potential weaknesses without damaging the component. This not only enhances the reliability of the weld but also builds trust with clients seeking long-lasting solutions.
Despite the complexities involved in welding stainless steel rods, mastering the process significantly broadens one’s welding skills, offering opportunities across various industries, from construction to automotive applications. As this guide outlines, achieving exceptional results relies on a thorough understanding of materials, techniques, and safety measures. By prioritizing these elements, professionals can confidently produce high-quality, durable welds, setting themselves apart as experts in the field.