Welding rods, often overlooked in the expansive universe of welding, serve as the backbone for welding processes, merging metals with finesse and precision. They are indispensable to both amateur welders and seasoned professionals, each type engineered to meet specific applications and environments.
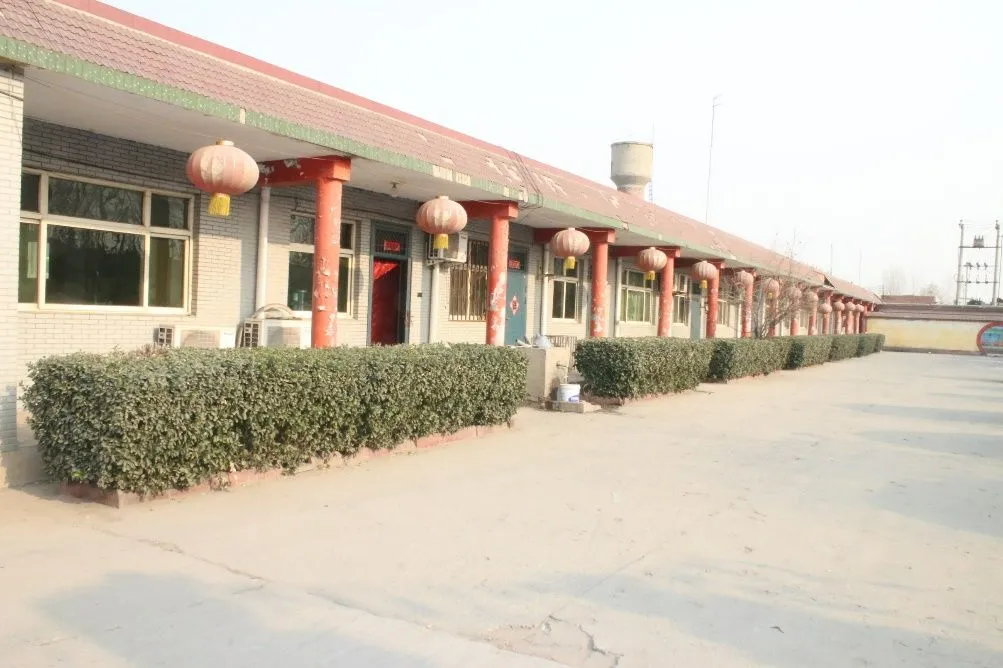
A welding rod, essentially a metal stick coated with flux, is the medium through which the electric arc is initiated. When heated by the electric arc, it melts to fuse two metal workpieces together, forming a strong bond. Understanding the nuances of different welding rods not only enhances the quality of the weld but also ensures the safety and efficiency of the process.
Experience with welding rods underscores their variability and customization. Users often start with the ubiquitous E6010 and E6011 rods, known for their deep penetration capabilities and suitability for dirty or rusty surfaces. These rods are the go-to for outdoor welding, often utilized for pipeline and structural work due to their ability to create a stable arc under challenging conditions. On the other hand, a smoother finish can be achieved with E7018 rods, favored for high-strength applications thanks to their low-hydrogen coating which minimizes the risk of cracking.
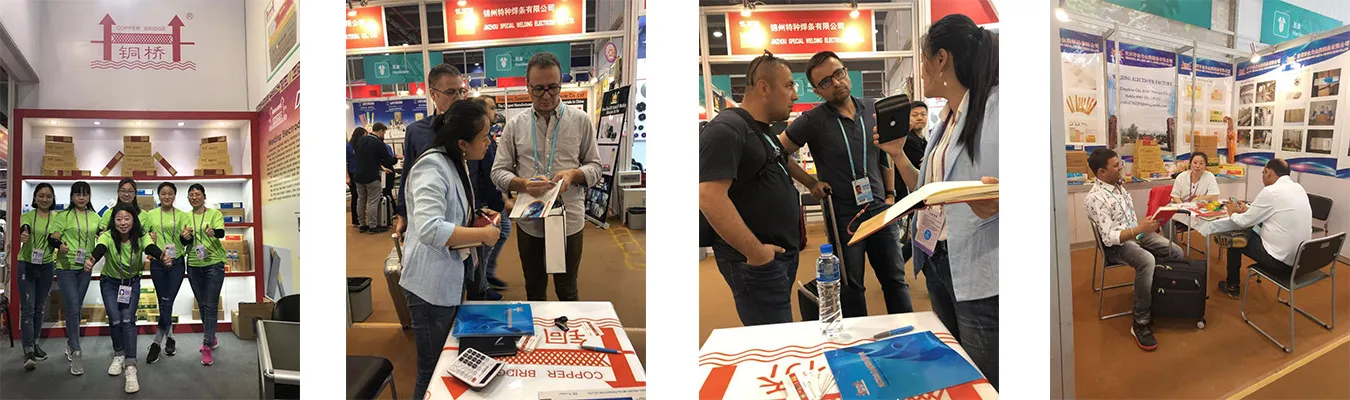
Expertise in welding rods involves selecting the right one for the task. A professional’s toolkit may look vastly different depending on their specialization. Stainless steel rods, like the E308L, cater to tasks requiring corrosion resistance, often seen in food-grade or medical applications. For aluminum welding, a different genre altogether emerges with rods like the ER4043, suitable for its malleable nature and ability to form a clean, smooth bead. Understanding these distinctions ensures that welders employ the right rod to meet the mechanical and metallurgical criteria of their workpieces.
welding rod explained
The authoritativeness of welding rods can be observed in industry standards and certifications. Organizations such as the American Welding Society (AWS) set rigorous classifications to guarantee the quality and performance of welding rods. Adherence to such standards not only instills confidence in the product's reliability but also ensures compliance with safety regulations across industries. Following these benchmarks is crucial to prevent weld failures, which could lead to catastrophic consequences.
Trustworthiness in a welding rod is often built on brand integrity and user reviews. Leading manufacturers invest in research and development to improve rod formulas, taking feedback from field experts to refine performance characteristics. This collaboration between manufacturers and end-users leads to innovation in coating materials, arc stability, and deposition rates, contributing to the rod’s dependability. Welders often rely on trusted brands and proven performance testimonials to inform their purchases, ensuring a product that consistently meets their stringent requirements.
In conclusion, welding rods are not merely consumables but are vital components in the elaborate tapestry of welding. Their selection requires an informed understanding of both the material involved and the environment in which they will operate. By blending experience, expertise, authoritative standards, and trustworthiness, welding professionals can optimize their projects, resulting in durable and precise welds that stand the test of time. As the field of welding continues to evolve, the welding rod remains an integral tool, indispensable to the art and science of metalwork.