Selecting the right welding electrode wire is essential for achieving optimal welding performance, ensuring both the durability and strength of the welded joint. In my extensive experience, I've seen that the choice of electrode wire significantly influences not only the welding process itself but also the integrity of the final product.
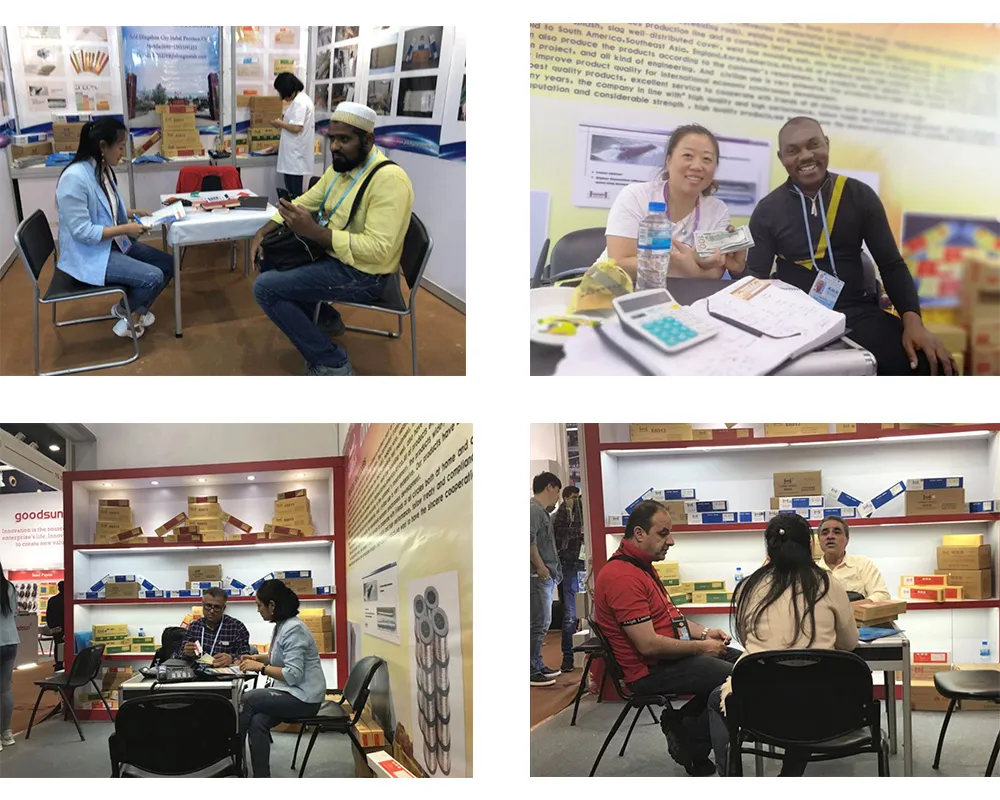
One of the critical aspects to consider in the selection process is the type of material being welded.
Different metals require specific types of electrode wires. Mild steel, stainless steel, and aluminum, for instance, each have unique properties that necessitate distinct approaches. Having expertise in metallurgy can greatly aid in understanding which electrode wire aligns best with the metal in question. For example, using stainless steel wires for mild steel applications might result in poor weld quality due to compatibility issues.
Moreover, the diameter of the welding electrode wire is another determinant of welding success. The wire's thickness should match the type of welding project and the power output of the welding machine. Larger wires conduct more electricity, providing deeper penetration for heavier metal sections, while thinner wires are ideal for more delicate tasks. This nuanced understanding of welding dynamics is where professional expertise shines.
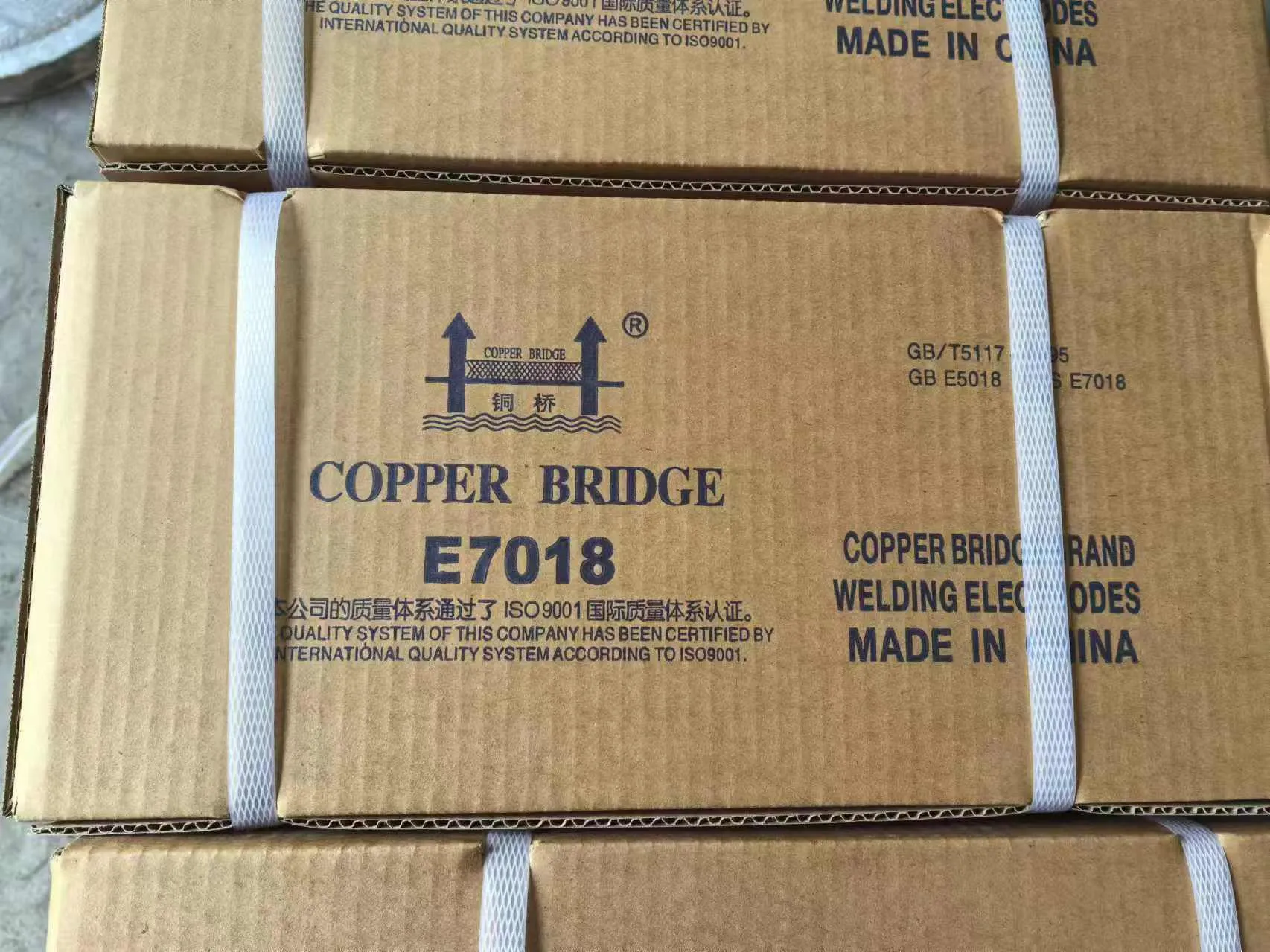
Equally important is the wire's chemical composition, which dictates the mechanical properties of the weld. Whether you're dealing with Ti, Ni, or other alloy elements, having a strong command of how these react under high temperature is crucial. Working in the field, I've witnessed the consequences of ignoring these details—ranging from smaller defects to catastrophic failure of welded joints. Therefore, embracing an authoritative knowledge base can prevent these costly errors.
welding electrode wire
Beyond technical specifications, manufacturers often provide additional insights into the performance of welding electrode wires, which should not be overlooked. Trusted brands have developed reputations based on rigorous testing and quality assurance processes. My authority in the field stems from an unwavering commitment to products that have consistently demonstrated reliability and compliance with industry standards. A trustworthy recommendation is to invest in electrode wires from manufacturers with certified quality management systems like ISO 9001.
On a practical note, understanding the real-time performance of the electrode wire in action is paramount. This comes from direct experience with welding projects across various industries. Trial runs and experimentation with different brands and types of wires provide invaluable firsthand information. It’s through these experiences that I can confidently guide peers towards the optimal choice, emphasizing the significance of practice-backed trustworthiness.
Therefore, when considering welding electrode wires, it’s not just about picking a component off the shelf. It demands a detailed understanding of the welding scenario, the metallurgical implications, and the equipment used—all founded on an authoritative base enriched by personal experience. This holistic approach ensures that each weld not only meets but exceeds expectations in strength, durability, and aesthetic finish, reinforcing why choosing the right electrode wire is indispensable for welding excellence.