Welding electrodes are a critical component in the welding process, and their pricing can significantly impact budget allocation and project planning in various industries. Understanding the intricacies of welding electrode prices requires not only knowledge of the current market dynamics but the technical aspects influencing these costs.
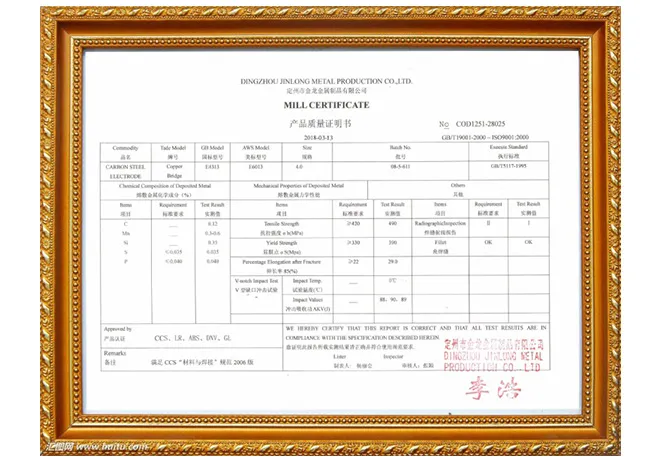
Firstly, it's essential to recognize that the price of welding electrodes is affected by the material composition. Electrodes can be made from a variety of materials, including mild steel, stainless steel, and non-ferrous metals like aluminum or copper alloys. Steel electrodes are typically less expensive due to the abundance of raw materials and established manufacturing processes. In contrast, specialty electrodes for exotic metals can be significantly more costly due to the rarer materials and advanced production techniques required.
Another key factor affecting electrode pricing is the coating type. The coating serves a critical role in stabilizing the arc and determining the electrode's usability in different welding positions. Basic coated electrodes tend to be cheaper, while those with cellulosic or rutile coatings might see a price increase due to their enhanced performance characteristics, such as improved penetration and smoother weld beads.
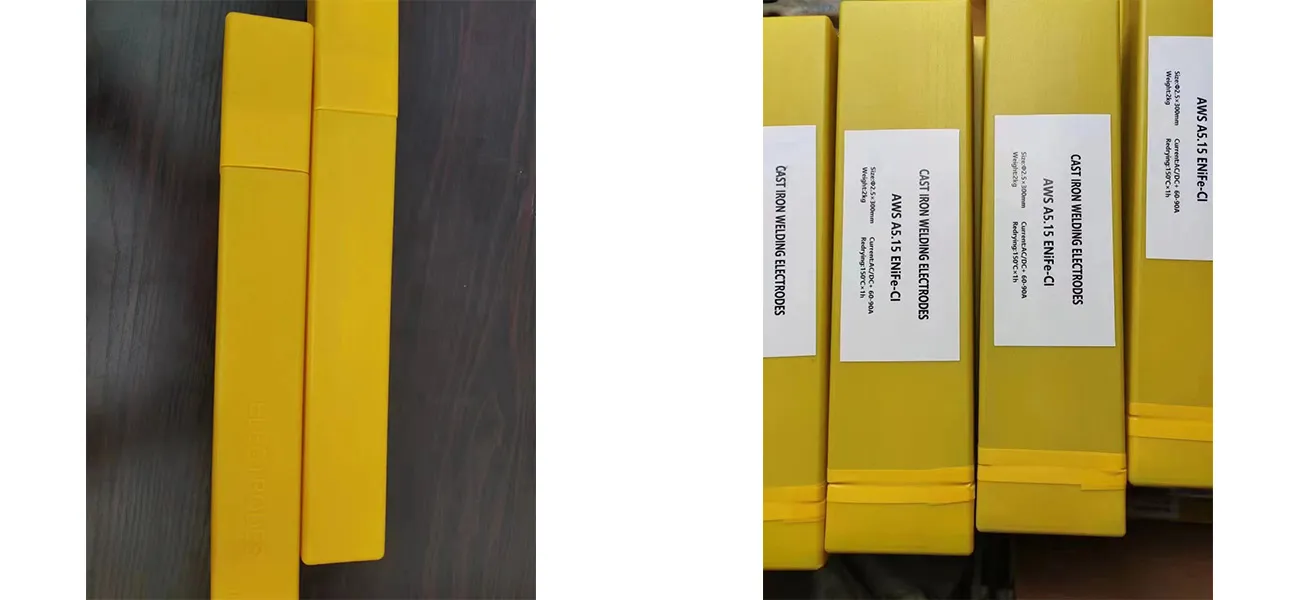
Additionally, the electrode's diameter has an impact on pricing. Larger diameter electrodes deposit more filler material in a shorter amount of time, which can be essential for heavy-duty applications, thus potentially commanding a higher price. Conversely, thinner electrodes, while potentially less expensive, might require more skill to handle and can increase overall welding time.
welding electrodes price
Market demand and geopolitical events play non-negligible roles in welding electrode pricing. Global demand for infrastructure development, particularly in emerging economies, can lead to increases in metal prices, subsequently driving up the cost of electrodes. Supply chain disruptions, tariffs, and regulatory changes can also lead to pricing volatility. It's crucial for procurement managers to stay informed about these global trends to anticipate price fluctuations and strategize purchases accordingly.
From a professional perspective, investing in quality electrodes can yield long-term savings despite higher initial costs. High-quality electrodes produce less spatter, are easier to use even under challenging conditions, and ensure stronger welds, reducing the likelihood of costly rework. Furthermore, leading manufacturers often offer technical support and product warranties, enhancing their value proposition.
For those in the industry, partnering with reputable electrode suppliers can provide a competitive advantage. These suppliers often have in-depth technical expertise and can advise on the best electrode type for specific applications, thereby optimizing both cost and performance. Moreover, bulk purchases and long-term contracts can sometimes secure better pricing, mitigating the risks associated with market fluctuations.
Ultimately, understanding welding electrode pricing requires a balance of technical know-how and market awareness. By focusing on the total cost of ownership rather than just the upfront price, companies can make informed decisions that support both quality and economic efficiency. Being equipped with this knowledge aids in the proper allocation of resources, ensuring successful project outcomes and sustained operational excellence.