When selecting welding electrodes, manufacturers play a pivotal role in ensuring quality, performance, and reliability in industrial applications. Understanding the significance of these components can aid in better decision-making for professionals and businesses alike.
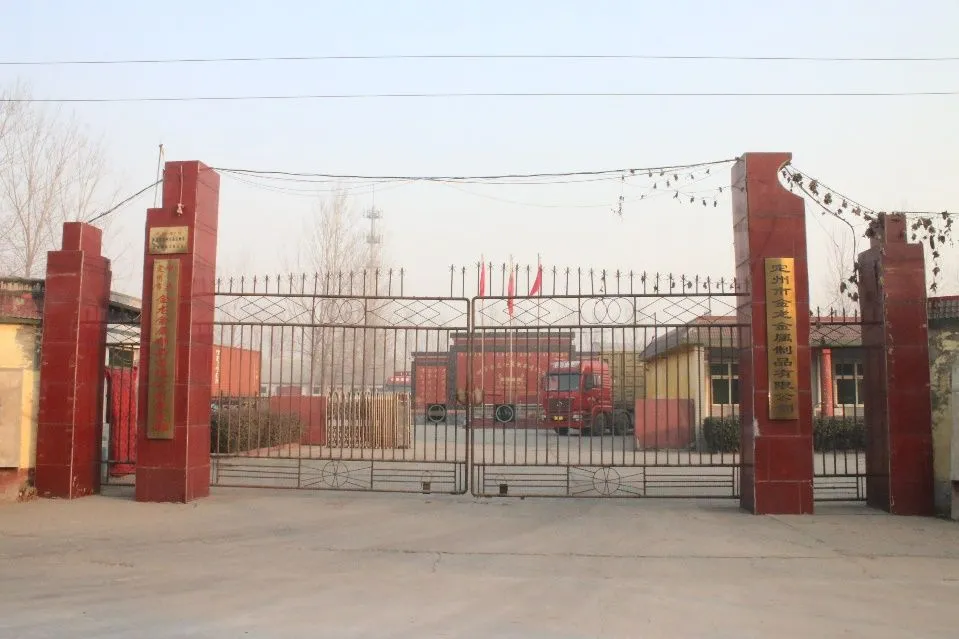
Welding electrodes are essential in the welding process, serving as the filler material that melts and creates a bond between two metal pieces. The quality of these electrodes directly influences the strength and durability of the weld, which is why sourcing them from reputable manufacturers is crucial.
Manufacturers with extensive experience in producing welding electrodes often invest in research and development to refine their products. This expertise allows them to offer electrodes that cater to a wide array of materials including steel, aluminum, and exotic alloys, each requiring specific electrode compositions. A skilled manufacturer will provide comprehensive guidance on choosing the right electrode for a particular application, accounting for factors like the type of metal, the weld position, and the desired strength of the weld.
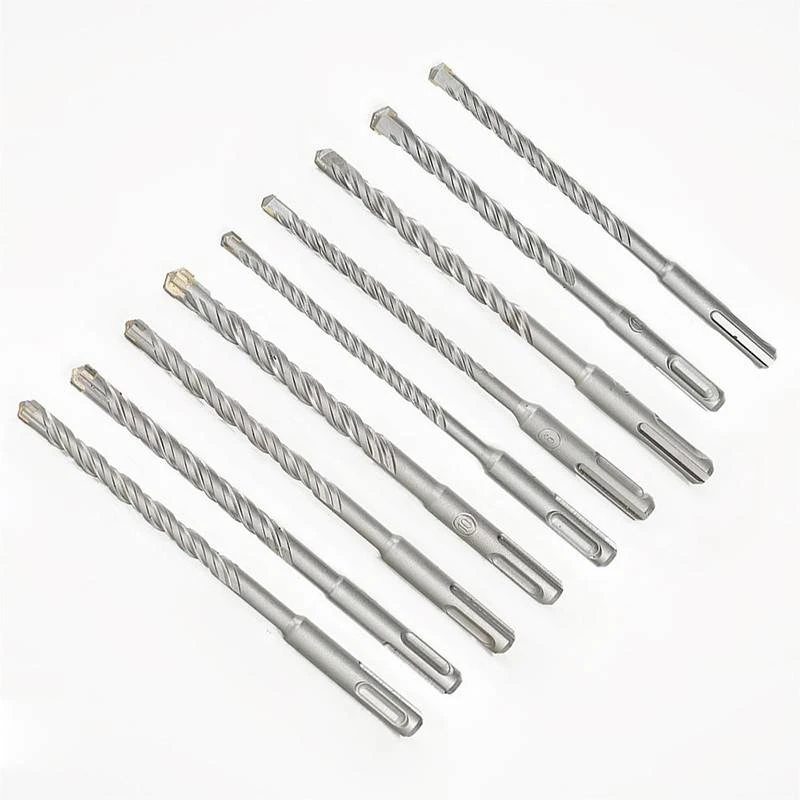
Authoritative manufacturers demonstrate their expertise by adhering to international quality standards such as AWS, ISO, and ASME certifications. These certificates are not mere endorsements but serve as benchmarks of a manufacturer's commitment to quality and safety. Partnering with manufacturers who meet or exceed these standards ensures that their welding electrodes can be trusted for both routine and critical applications.
Furthermore, trustworthiness in manufacturers extends beyond product quality. It encompasses transparent communication and support services that assist clients throughout the purchasing and application process. This includes offering comprehensive technical data sheets, user manuals, and direct access to technical support teams for troubleshooting and optimization.
welding electrodes manufacturers
Product innovation is another hallmark of leading welding electrode manufacturers. Embracing new technologies and processes, such as automation and AI-driven quality inspection, they continuously enhance their production lines, resulting in improved electrode performance. Features like low spatter, ease of slag removal, and consistent arc stability are frequently optimized in modern welding electrodes, addressing the evolving needs of today’s welding professionals.
Environmental stewardship also signals a responsible manufacturer. Companies that prioritize sustainability adopt eco-friendly practices in their manufacturing processes, such as recycling waste materials and reducing emissions. This not only benefits the environment but also demonstrates a commitment to social responsibility, an increasingly critical factor in supplier selection.
In the competitive market of welding electrodes, price, though an important factor, should rarely be the sole criterion for selection. The cost must be evaluated in conjunction with the performance and reliability offered by the electrodes. High-quality electrodes can often lead to lower overall costs by reducing rework, ensuring faster job completion, and maintaining high safety standards.
Ultimately, the choice of welding electrode manufacturer can vastly influence operational efficiency and project outcomes. Reputable manufacturers offer not just products, but solutions that cater to the specific demands of industrial applications, backed by expertise and a proven track record. Their commitment to quality, innovation, and customer satisfaction renders them a valuable partner in any welding endeavor, extending far beyond a simple transaction and into the realm of strategic partnership.
In summary, selecting welding electrodes is not just about meeting immediate needs but aligning with manufacturers known for their experience, expertise, authoritativeness, and trustworthiness. Such a partnership ensures that the equipment used consistently performs to the highest standards, providing peace of mind and supporting business success in the long term.