When it comes to selecting the right welding rod for high-stakes projects, the MG 7018 welding rod frequently emerges as a top contender among professionals. This low-hydrogen iron powder electrode is unparalleled in its ability to deliver superior results on a variety of metals and applications. Its reputation is built on years of proven performance, expert design, and consistent reliability, making it a critical tool for those requiring precision and durability in their welding endeavors.
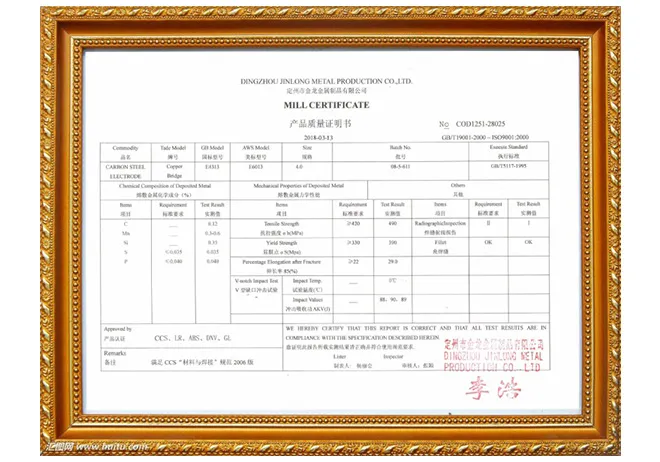
MG 7018 is distinguished by its ability to produce high-quality welds with a smooth, stable arc. What sets it apart is its versatility — it can effectively weld carbon and low-alloy steels, making it suitable for a myriad of construction and repair contexts. Its unique formulation allows it to deposit welds with low spatter and excellent bead appearance, crucial factors in maintaining high standards of visual aesthetics and structural integrity.
In line with professional welding standards, the MG 7018 welding rod exhibits superior mechanical properties. It has impressive tensile strength and toughness, crucial for welds that will withstand substantial stress or shock. This makes it ideal for heavy machinery repairs, construction of load-bearing structures, and applications requiring rigorous safety compliance. For professionals in industries such as shipbuilding, oil and gas, and structural steel work, the MG 7018 ensures durability and maintains the integrity of the welds under demanding conditions.
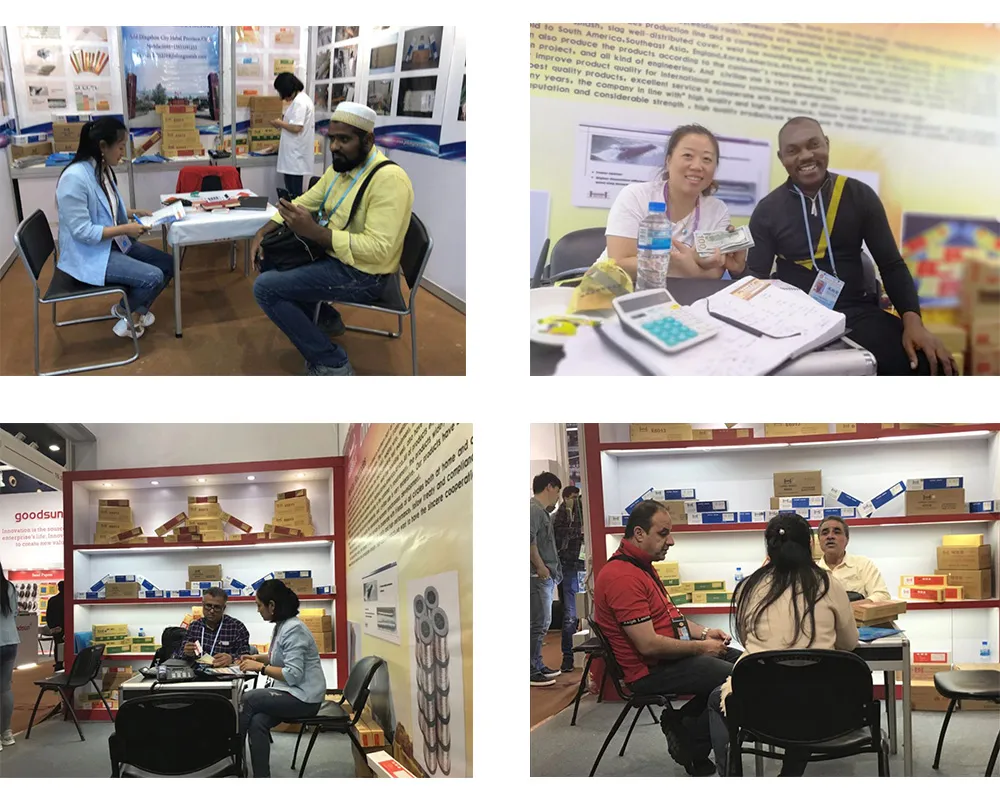
Expert opinion often highlights the critical nature of the environment in which welding occurs, especially when moisture is involved.
The MG 7018 welding rod's low-hydrogen properties reduce the risk of hydrogen-induced cracking. By limiting hydrogen content in the deposit, it helps prevent cold cracking in the heat-affected zone, an essential factor for ensuring long-term weld quality and safety. This characteristic is particularly beneficial where thick sections or rigid joints are present, areas prone to residual stress and cracking.
Trustworthiness in welding applications often boils down to consistent performance, and this is where the MG 7018 excels. Each rod is manufactured to rigorous standards, ensuring each weld possesses the purity and quality expected by experts and engineers worldwide. Its usage spans critical projects, including high-rise constructions and major infrastructure developments, where consistency and safety cannot be compromised.
mg 7018 welding rod
For those seeking authoritative insight, numerous welding professionals and engineers endorse the MG 7018 as a preferred choice. Its comprehensive support for both vertical and overhead welding positions speaks to its adaptability across varying project demands. This capability, coupled with easy slag removal, optimizes the efficiency and speed of work, driving productivity without sacrificing quality.
Moreover, the MG 7018 welding rod's performance is not merely anecdotal; it is supported by established industry certifications. This compliance with international welding standards ensures that its application aligns with both safety regulations and client expectations, reinforcing trust and authority in project execution.
Real-world experiences from veteran welders frequently underscore the MG 7018’s role as a mainstay in their toolkit. Having witnessed its reliable performance over decades, they continue to advocate for its use in environments where failure is not an option. This shared knowledge, passed through generations of welders, solidifies its standing in the industry as a staple for delivering exceptional welding outcomes.
In conclusion, the MG 7018 welding rod stands as a testament to what advanced welding technology can offer. With a foundation built on expertise, authority, and trustworthiness, it remains a compelling choice for professionals demanding precision, reliability, and quality in their welding projects. Whether tackling complex repairs or new constructions, the MG 7018 endows each project with the assurance of excellence.