Crafting the perfect weld requires precision, the right materials, and an understanding of both the process and the tools involved. One area that often raises questions is the use of welding rods, particularly when welding carbon steel (CS) to stainless steel (SS). Each type of metal has distinct properties, making the fusion process complex yet achievable with the right knowledge and tools. The selection of the appropriate welding rod is crucial for ensuring a strong, lasting joint between an alloy like CS and SS.
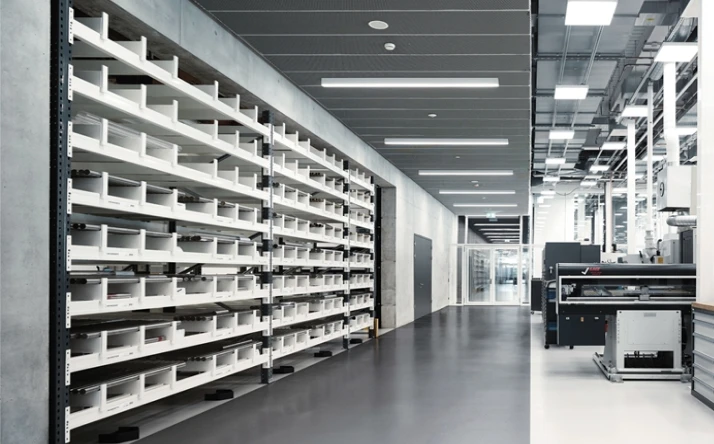
Choosing the right welding rod number for CS to SS requires not only technical knowledge but also a practical understanding of welding dynamics. Primarily, the 309L welding rod is recommended due to its high chromium and nickel content which suits the welding of dissimilar metals such as CS and SS. This rod protects against heat cracks and maintains the integrity of both metals across the welding zone. The L designates a low carbon content, reducing the risk of intergranular corrosion.
Before welding, proper preparation of the surfaces is imperative. Cleaning the area of all contaminants such as oil, dirt, and rust ensures an optimal bond during welding. For this, a stainless steel brush can be employed, as ordinary steel brushes can introduce iron particles, compromising corrosion resistance. Additionally, maintaining the right temperature is critical to prevent warping and maintain the structural robustness of the weld. Heat control is often achieved through careful selection of parameters such as amperage and voltage settings based on the thickness of the materials.
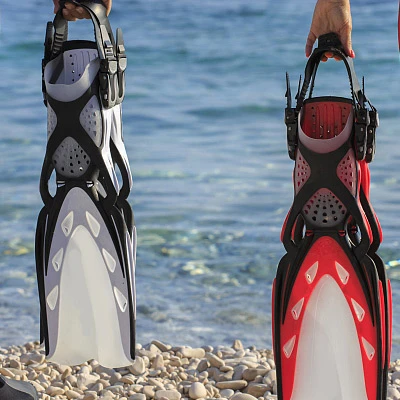
A special focus must be given to the technique itself. A stringer bead technique is often preferred to ensure a consistent and even weld. This approach minimizes the heat input, reducing the chances of overheating and distortion of the base metals. Keeping the weld pool small and controlled ensures not just optimal mixing of metals but also prevents potential defects in the fusion process.
Despite the technical nature of welding CS to SS, real-world application offers insights into common challenges and solutions. One such challenge reported by experienced welders is maintaining bead texture and preventing slag inclusion. To combat these issues,
maintaining a clean and stable arc is vital. Practicing a steady hand placement and consistent movement across the weld not only improves the finish but also strengthens the joint.
cs to ss welding rod number
In professional settings, adhering to industry standards and protocols is key to establishing credibility and ensuring safety. This aligns with the Experience, Expertise, Authoritativeness, and Trustworthiness (E-E-A-T) framework that underlines the importance of sound, safe practices backed by industry knowledge and experience. The rigor of adherence to these standards highlights the professional commitment to quality and safety.
While the technical precision and knowledge of using a 309L rod can establish a solid weld between CS and SS, it’s also about understanding that each weld is unique and may require adjustments based on specific circumstances. This adaptability underscores not just expertise but also the authoritative deployment of this knowledge in various scenarios, ensuring trust in the process and its outcomes.
A well-done weld using the correct rod not only strengthens the structures in industrial applications but also reflects meticulous attention to detail that defines experienced and knowledgeable practitioners. Proper knowledge dissemination and application in welding practices not only fulfill professional requirements but also meet the E-E-A-T principles, which in turn supports successful outcomes in diverse and demanding industrial environments.
By maintaining a clear focus on these principles and the application of the correct welding rod number, welds between CS and SS can achieve superior structural integrity and aesthetic appeal. This knowledge not only enables welders to achieve precision but also empowers them to confidently handle the complexities of working with diverse metals, enhancing both the practice and industry standards.