When using a 6011 welding rod measuring 3/32 inches, understanding the appropriate amperage settings is crucial for achieving optimal results in your welding projects. The 6011 welding rod is renowned for its deep penetration capacity, making it an ideal choice for welding scenarios involving rusty or dirty metals, even in less-than-ideal conditions like outdoor environments. This electrode's versatility stems from its cellulose-based flux coating, which produces forceful arc action and leaves a minimal slag covering, suitable for a variety of surfaces and positions.
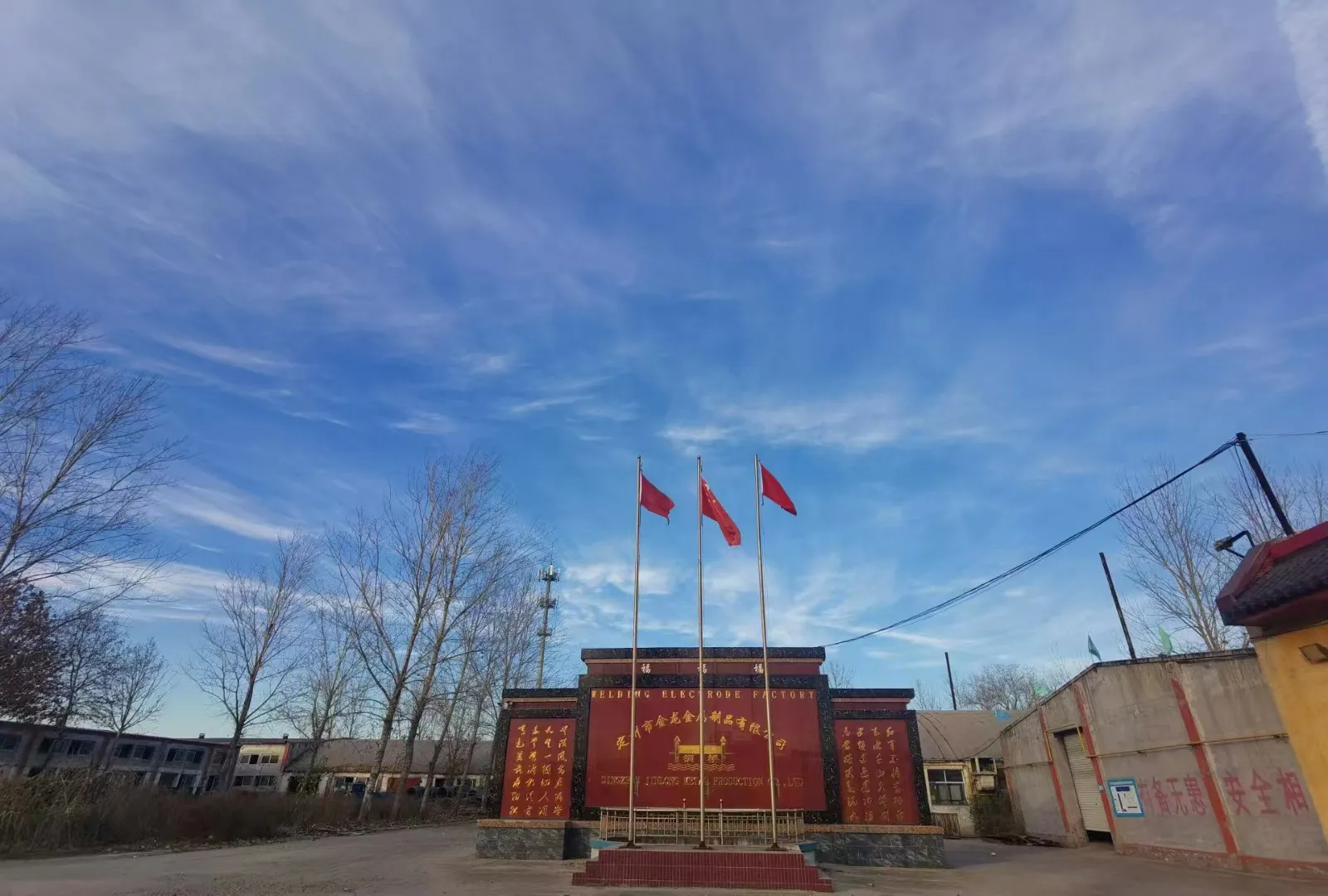
For welders who frequently tackle farm equipment repair, construction, or maintenance tasks, the 6011 welding rod provides a reliable solution due to its robust nature. Balancing the electrode size, specifically the 3/32 inch variant, with precise amperage settings significantly impacts both the quality of the weld and the ease of operation.
Experience dictates that the power source's amperage should align closely with the manufacturer's recommendations and the specific metal thickness and condition.
For a 3/32 inch 6011 welding rod, the ideal amperage range typically falls within 40 to 85 amps. This range allows for sufficient heat input to ensure deep penetration while avoiding excessive burn-through, particularly on thinner metal sections. Novice welders often start with lower amperage settings to gain confidence in controlling the weld puddle and gradually increase the power as their skill improves.
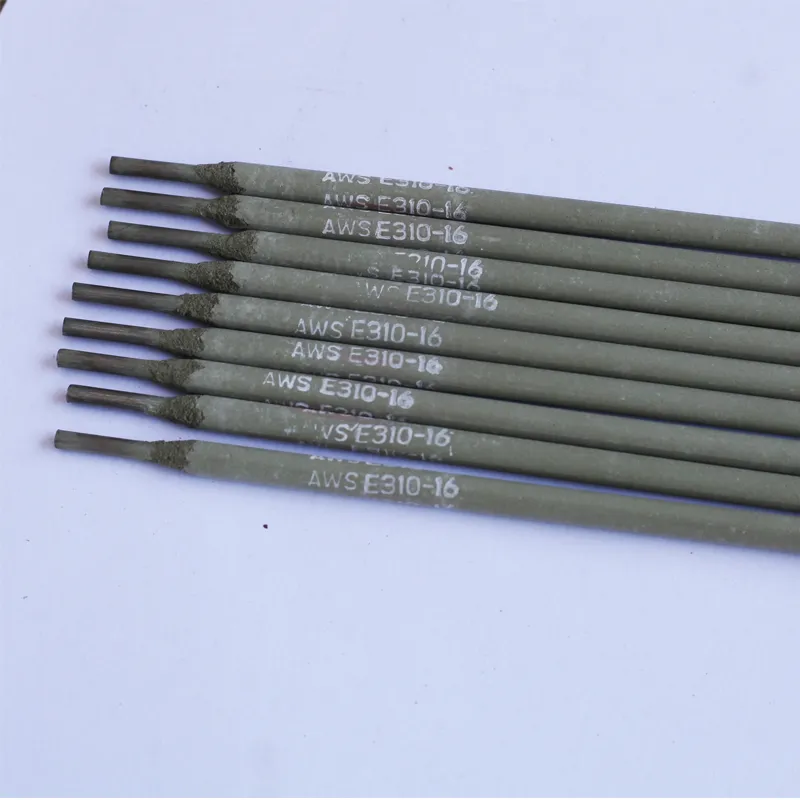
Expertise in welding also emphasizes the importance of adjusting amperage according to the welding position. For instance, vertical and overhead positions might require a slight reduction in amperage compared to flat or horizontal welding to prevent the dripping of molten metal and maintain effective puddle control. Deploying proper technique in managing the travel speed and angle of attack can further enhance weld quality and consistency when using the 6011 rod at these settings.
Not only does choosing the correct amperage ensure structural integrity, but it also affects the overall welding experience. A smooth, steady arc eases the process of maintaining a uniform bead, reducing the likelihood of defects such as undercut or lack of fusion. Moreover, appropriate settings can help minimize the release of fumes and spatter, contributing to a safer and cleaner working environment.
6011 welding rod 3/32 amps
From an authoritative perspective, gaining proficiency with the 6011 rod transcends mere mechanical adjustments. An understanding of its chemical composition and behavior under heat underscores the importance of welding practice guided by a theoretical foundation. The high cellulose content in the flux coating is responsible for substantial slag fluidity, which facilitates self-ejection and allows welding on painted or greasy surfaces without thorough pre-cleaning.
Trust in manual mastery also comes from recognizing the complementarity between the welder and the machine. Adopt appropriate personal protective equipment and leverage advancements such as auto-darkening helmets to enhance vision and shield against ultraviolet light, enabling more precise welds and longer working sessions without compromising safety.
Incorporating advanced technology into welding practice, such as feedback circuits or digital displays, can assist welders in accurately dialing in the recommended amperage settings. These features bridge the gap between theoretical parameters provided by technical documentation and practical, real-time adjustments based on feedback loops, enhancing both precision and confidence during application.
Ultimately, harnessing the full potential of a 6011 welding rod 3/32 inch comes with patience, practice, and a commitment to lifelong learning. Regular upkeep and understanding of the welding equipment are equally pivotal to attaining a high standard of work. As professionals refine their technique and approach, they develop not just skill but also intuition, allowing them to interpret variances in sound, heat, and arc behavior that signify the need for adjustment.
By focusing on these fundamental aspects of welding science and insights gained from field experience, users can achieve the desired results with the 6011 rod while navigating the diverse challenges presented by real-world applications. As a cornerstone electrode type, the 6011's adaptability underscores the importance of expert guidance and informed experimentation, leading to successful, repeatable outcomes and reinforcing trust in the weld's durability and performance.