Selecting the right welding rod for stainless steel can significantly impact the quality and durability of your welds. Stainless steel is revered for its corrosion resistance and aesthetic appeal, requiring attention to detail when welding to maintain these properties. The welding rod, also known as a filler rod, plays a crucial role in ensuring that the welds are strong, reliable, and consistent with the characteristics of stainless steel.
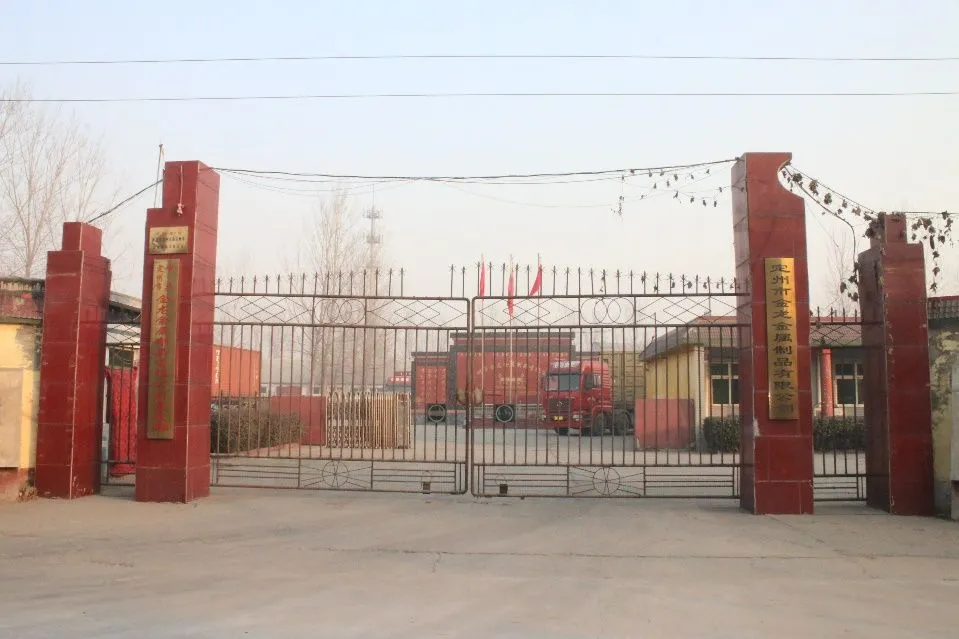
Understanding Stainless Steel Welding
Stainless steel is an alloy comprising iron and chromium, often with other elements like nickel and molybdenum.
The most popular types used in welding are austenitic stainless steels, which belong to the 300 series. Their composition demands a compatible filler material to ensure proper bonding and prevent issues like corrosion, cracking, or structural failure.
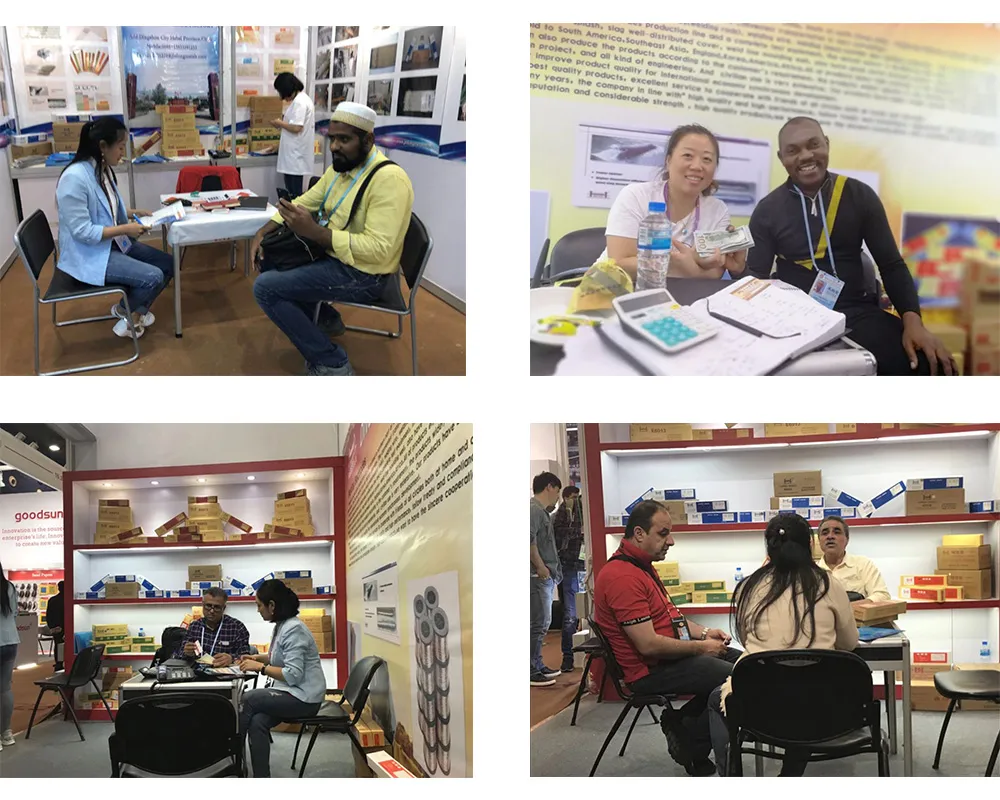
Key Factors in Choosing Welding Rods
1. Match the Alloy Composition It is essential to match the filler material with the base metal. For austenitic stainless steels like 304 or 316, using an ER308 or ER316 rod is often recommended. These rods contain similar alloys, ensuring the weld inherits their corrosion resistance and tensile strength.
2. Corrosion Resistance Since one of stainless steel's primary benefits is its resistance to oxidation and corrosion, selecting a rod that maintains this characteristic is critical. Nickel and molybdenum content in rods like ER316 provide superior resistance to pitting corrosion, making them ideal for marine environments or chemical processing applications.
3. Mechanical Properties The rod you choose should enhance, or at least maintain, the mechanical properties of the metal. Consider tensile strength, hardness, and ductility. For instance, if you are welding components subject to high pressure, rods with higher tensile strength might be necessary.
4. Avoiding Sensitization Sensitization occurs when stainless steel is heated between 800 and 1500 degrees Fahrenheit, causing chromium to form carbides, resulting in intergranular corrosion. Low-carbon rods, such as ER308L or ER316L, minimize this risk by having lower carbon content.
5. Welding Technique Compatibility The welding method you choose affects the choice of rod. For instance, TIG (Tungsten Inert Gas) welding often requires more precision and uses rods like ER308L for thin stainless steel sheets, while MIG (Metal Inert Gas) welding may use ER308L for thicker applications.
what rod to use when welding stainless steel
Expert Recommendations
The collective experience of seasoned welders highlights the importance of using high-quality rods from reputable manufacturers. Brands like Lincoln Electric, ESAB, and Hobart are well-regarded in the industry for producing consistent rods that minimize defects and enhance weld integrity.
Preparing for Welding
Preparation is as crucial as the selection of the rod. Clean the surfaces thoroughly to remove contaminants and preserve the cleanliness that stainless steel offers. Additionally, maintaining a stable and appropriate heat input helps prevent warping and ensures that the properties of both the base and filler materials remain intact.
Practical Considerations
In practice, the working environment may also dictate rod choice. For outdoor projects, where wind can impact gas shielding, using rods with suitable shielding characteristics or considering flux-cored options for MIG can be beneficial.
Ongoing Learning and Adjustment
As stainless steel technology and welding techniques evolve, staying updated with the latest advancements can provide a competitive edge. Participating in continued education, attending workshops, and consulting updated welding handbooks can keep your skills and knowledge current.
In conclusion, using the right rod for welding stainless steel dramatically influences the quality and longevity of your projects. By considering factors such as alloy compatibility, corrosion resistance, mechanical strength, and welding technique, you ensure optimal results. Prioritizing reputable brands and meticulous preparation further contribute to the efficacy and reliability of your welds.