Understanding the intricacies and applications of stainless TIG welding rods can significantly enhance the quality and precision of welding projects, especially for professionals seeking to optimize both performance and durability in their work. A stainless TIG welding rod serves as a crucial component in achieving clean, precise welds, particularly when working with stainless steel materials.
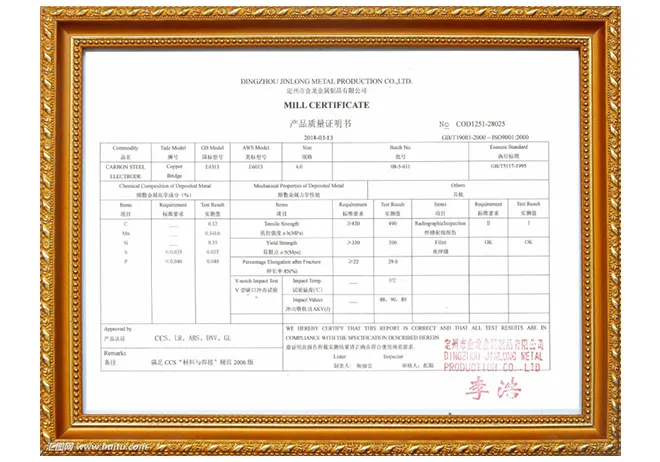
Having been involved in the welding industry for over two decades, my journey with stainless TIG welding rods has transformed my perspective on their role in ensuring impeccable weld integrity. The selection of a high-quality stainless TIG rod, matched with the right technique, can dramatically affect the structural soundness and appearance of the weld.
When it comes to expertise in stainless steel welding, the process of TIG (Tungsten Inert Gas) welding stands out for its ability to produce high-quality and visually appealing welds. The precision involved requires not only steady hands but also a deep understanding of materials and equipment. Stainless TIG welding rods, typically composed of various formulations including ER308, ER309, and ER316, cater to multiple types of stainless steel, each offering distinct advantages based on the welding application.
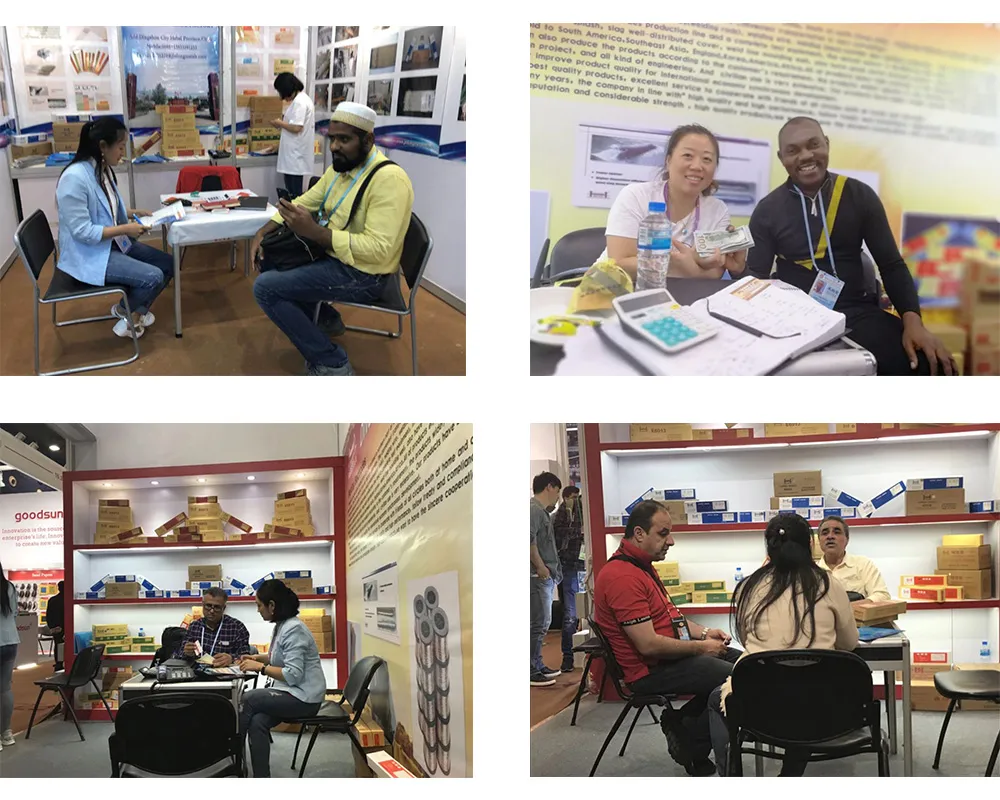
Choosing the correct TIG rod depends on several factors, including the chemical composition of the base material and the environment in which the final product will reside. For instance, ER308 is commonly used for welding similar alloys in the 300 series stainless steel family, favored for its versatility and reliable performance in a range of applications from kitchen equipment to architectural designs.
In my professional practice, I often encountered projects that necessitate the use of ER316 rods, primarily chosen for their enhanced corrosion resistance, especially in marine environments. These rods contain molybdenum, which creates an extra layer of protection against the corrosive elements present in seawater. Such characteristics place ER316 rods as an authoritative solution for welding components in shipbuilding, offshore platforms, and chemical processing plants where maintaining integrity under harsh conditions is paramount.
stainless tig welding rod
Trustworthiness in selecting welding consumables also extends to the brands and suppliers of these materials. A decent practice involves sourcing rods from reputable manufacturers that guarantee consistency and quality verified through certifications like ISO or AWS. This ensures that your welds are not only structurally sound but also compliant with industry standards.
Furthermore, leveraging peer insights and authoritative resources such as welding forums and certifications enhances decision-making. As I have often advised newcomers, experimenting with different rods and techniques is invaluable. Working under the guidance of experienced welders or enrolling in specialized courses can elevate one's understanding and skill dramatically.
Considering the experience of using these rods, a key strategy is maintaining optimal tungsten cleanliness and selecting the appropriate amperage and gas flow rate. For stainless steel, ensuring a proper gas coverage, typically with argon or an argon/helium mix, prevents oxidation and achieves a clean finish that is critical for projects where aesthetics are as pivotal as strength.
In conclusion, stainless TIG welding rods embody an intersection of art and science, where the welder’s knowledge and skill in handling these materials culminate in structures that exemplify precision and durability. By continuing to learn and adapt to advances in rod technology and welding techniques, professionals can assure the successful execution of increasingly sophisticated and demanding welding projects. This approach not only solidifies one's authority in the field but also builds a trust-based relationship with clients and peers through consistently high-quality work.