Welding stainless steel to carbon steel is a technical endeavor that demands expertise and careful selection of materials. The weldability of these metals significantly impacts the integrity, strength, and durability of the welded joint. When considering ss to carbon steel welding rods, one must focus on compatibility, performance, and safety.
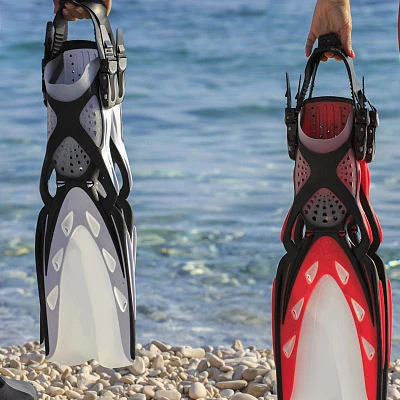
In the world of metallurgy, stainless steel and carbon steel are prevalent for their specific properties. Stainless steel is revered for its resistance to corrosion and heat, while carbon steel is renowned for its strength and affordability. Welding these two materials together combines their strengths, making it indispensable for a variety of industrial applications, including construction, automotive, and manufacturing.
The first step in welding stainless steel to carbon steel is choosing the right welding rod. This choice is critical as it influences the weld's quality and reliability. When discussing welding rods, AWS ER309L stands out as a preferred option. Known for its low carbon content, ER309L prevents carbide precipitation, which is paramount in avoiding intergranular corrosion.
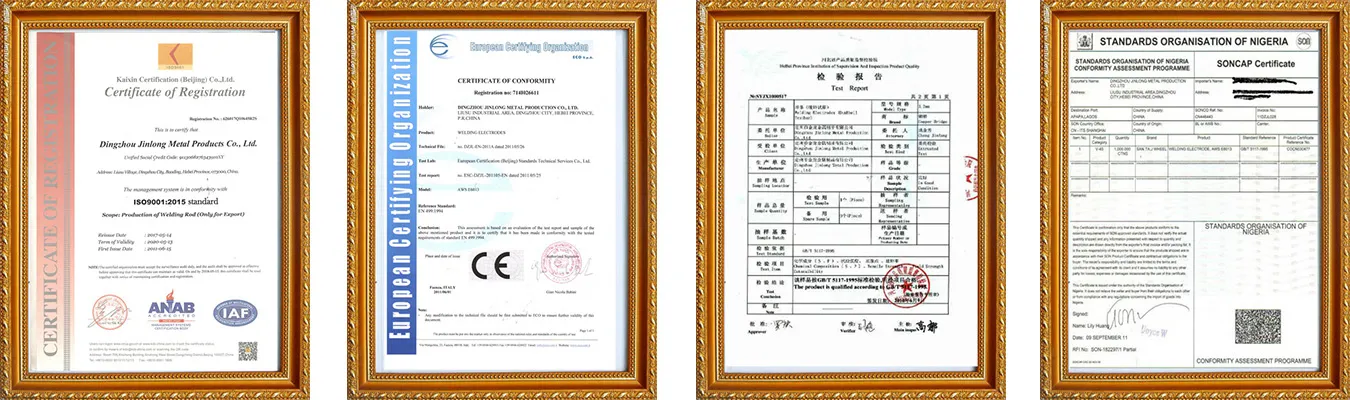
ER309L serves as a versatile welding rod designed explicitly for joining dissimilar metals. Its composition allows for the dilution of weld metal by both base metals, reducing the potential for phase changes that could weaken the joint. The chromium and nickel content in ER309L provide a balance that supports both metals' properties, ensuring a strong, ductile, and crack-resistant weld.
Another crucial factor to consider is the welding process. Gas Tungsten Arc Welding (GTAW) or Tig welding is commonly recommended for its precision and control. It limits thermal input, which is beneficial in retaining the properties of stainless steel and minimizing distortion. When performing GTAW, applying a shielding gas such as Argon with a back purge is essential. This practice protects the weld pool from oxidation, ensuring high-quality, clean welds.
Pre-weld preparation cannot be overstressed. It is imperative to clean the surfaces thoroughly to remove any contaminants such as oil, grease, or rust. These contaminants could lead to porosity and inclusions in the weld. Utilizing a stainless steel wire brush or dedicated grinding tools helps in maintaining cleanliness and ensuring a smooth weld zone.
ss to carbon steel welding rod
The welding parameters, such as current levels and travel speed, must be meticulously controlled. Since stainless steel conducts heat slower than carbon steel, managing heat input to prevent excessive grain growth in the Heat Affected Zone (HAZ) is vital. Excessive heat can lead to warping or weakening of the metals.
Post-weld treatments, including pickling and passivation, further enhance the integrity of the weld. These processes remove surface imperfections and promote the formation of the passive chromium oxide layer, which is critical for corrosion resistance.
Welders must also consider the potential for galvanic corrosion due to differing electrochemical potentials between stainless steel and carbon steel. Applying a protective coating or using a barrier such as paint or epoxy can mitigate this risk.
Professional expertise is essential in navigating the complexities of ss to carbon steel welding. Adhering to industry standards and protocols ensures that the welded structures not only meet safety regulations but also stand the test of time.
In conclusion, successfully welding stainless steel to carbon steel hinges on selecting the appropriate welding rod, meticulous preparation, and employing precise techniques. The combination of theoretical understanding and practical experience is instrumental in crafting welds that are not only robust and reliable but also resistant to the challenges posed by their operational environments. This approach guarantees that the welds not only serve their structural purpose but also enhance the overall performance of the application they support.