Solid welding wire plays a pivotal role in the foundation of strong, reliable, and high-quality welds, making it a critical component for industries ranging from automotive to construction and beyond. The ever-evolving demands of modern engineering require a thorough understanding and expertise in welding technologies, where solid welding wire stands out due to its unique characteristics and versatile applications.
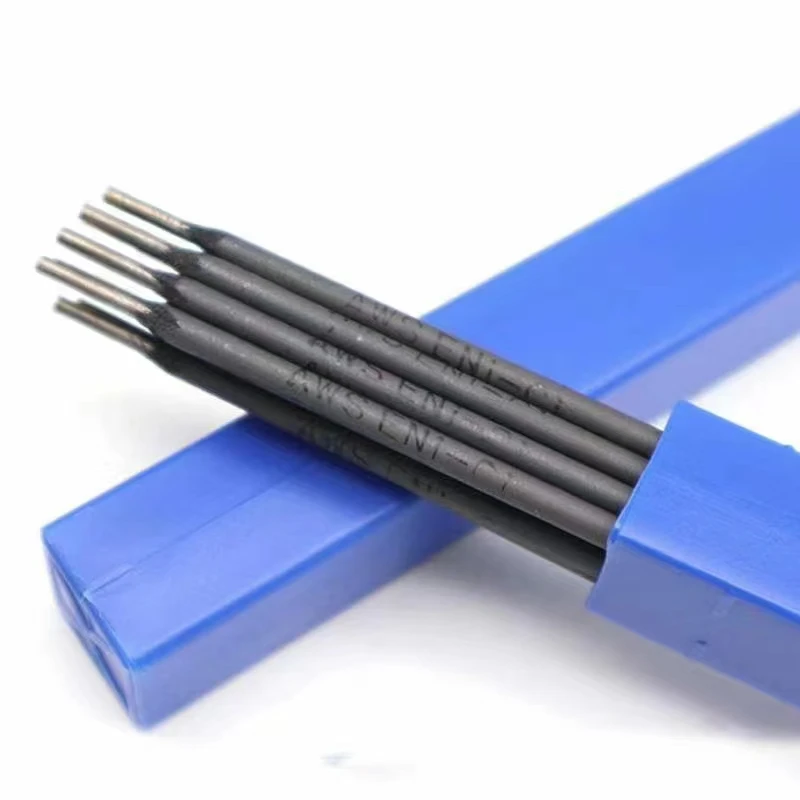
Solid welding wire is specifically engineered for consistent performance,
offering a clean and efficient welding process. Unlike flux-cored wires, solid wires lack an internal flux coating which results in minimal spatter production, reducing the need for after-weld cleaning. This attribute alone improves efficiency in industrial environments, where time and precision are paramount.
High-quality solid welding wire is manufactured with a focus on uniform diameter and excellent surface quality. This ensures smooth feeding through the welding gun, reducing the likelihood of interruptions that can lead to defects in the weld. The absence of surface impurities also enhances the stability of the arc, contributing to superior, defect-free welds.
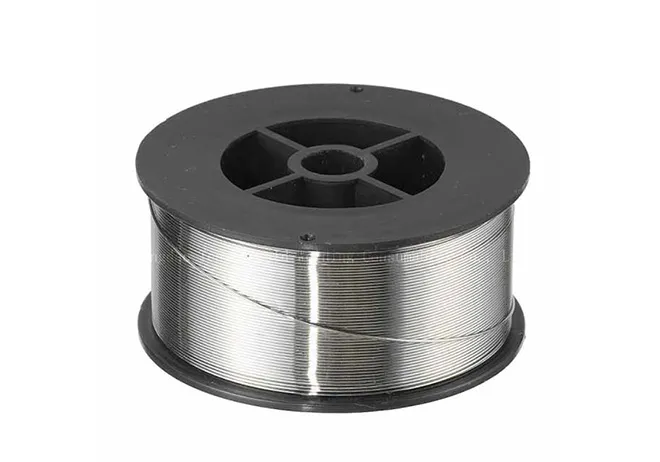
The chemistry of solid welding wire is equally crucial. It is composed of deoxidizers like manganese and silicon, which play a significant role in removing oxygen from the weld pool. This aspect prevents porosity and increases the overall strength of the weld. The ability to control these elements means solid welding wire can be tailored to match specific material compositions and environmental conditions, delivering optimal results for each project.
In terms of expertise, understanding the compatibility of solid welding wire with various base materials—such as carbon steel, stainless steel, and aluminum—is essential. Each material requires a specific wire type to achieve the desired mechanical properties and finish. For instance, ER70S-6 is a commonly used solid wire for mild steel due to its high silicon content, which provides good wetting action, perfect for sheet metal applications.
solid welding wire
The authority of a solid welding wire is measured by its compliance with industry standards like AWS (American Welding Society) or ISO (International Organization for Standardization). These certifications provide assurance of quality and performance consistency, crucial in sectors like aerospace or pressure vessel manufacturing where failure is not an option.
Trustworthiness in solid welding wire is built through both manufacturer reputation and field-proven results. Industry professionals often rely on established brands known for rigorous testing and quality control. This trust is further strengthened by hands-on experience and feedback from experienced welders who consistently choose specific brands for their reliability and ease of use.
Furthermore, the technological advancements in welding equipment necessitate solid welding wires that are compatible with modern automated and robotic systems. These wires need to exhibit excellent conductivity and compatibility with pulsed MIG systems, which are becoming increasingly popular for their precision and efficiency in high-production environments.
In conclusion, the appropriate selection and application of solid welding wire can significantly impact the success of a welding project. With high-performance solid welding wire, industries can achieve exceptional weld quality, reduce overall production costs, and enhance product durability. By harnessing the expertise, authority, and trustworthiness inherent in solid welding wire, companies can maintain a competitive edge, delivering results that meet the demanding specifications of today’s industrial landscape.