Nickel rods have become an essential component for anyone aiming to work with cast iron, lending both reliability and precision to the welding process. Precision in welding is crucial since cast iron, known for its brittle nature, can be a challenging material to work with. Here's how nickel rods offer an extraordinary solution, drawing on decades of professional welding expertise to ensure superior quality and long-lasting results.
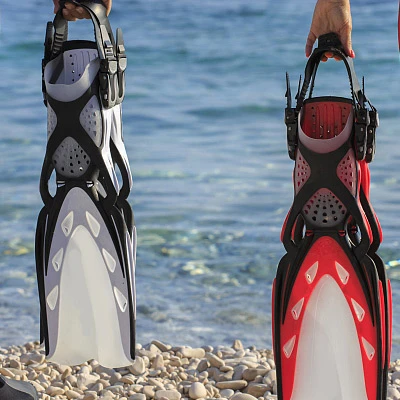
The unique properties of nickel rods make them particularly effective for cast iron applications. Nickel, as a metal, possesses a high degree of ductility and excellent thermal properties. These characteristics are pivotal when dealing with the temperature fluctuations inherent in welding cast iron. When molten iron cools, the high carbon content can lead to the formation of cracks. Nickel rods effectively minimize this risk because they closely match the thermal expansion properties of cast iron, ensuring coherence between the welded joint and the base material.
Professionals in the welding industry have historically favored nickel rods for repairing and fabricating cast iron components. Their significant advantage is the ability to provide high-strength bonds that withstand the test of time. This characteristic is particularly invaluable in industrial settings where cast iron is commonly used for its robustness and thermal resistance, such as in the construction of engine blocks, pipes, and heavy machinery.
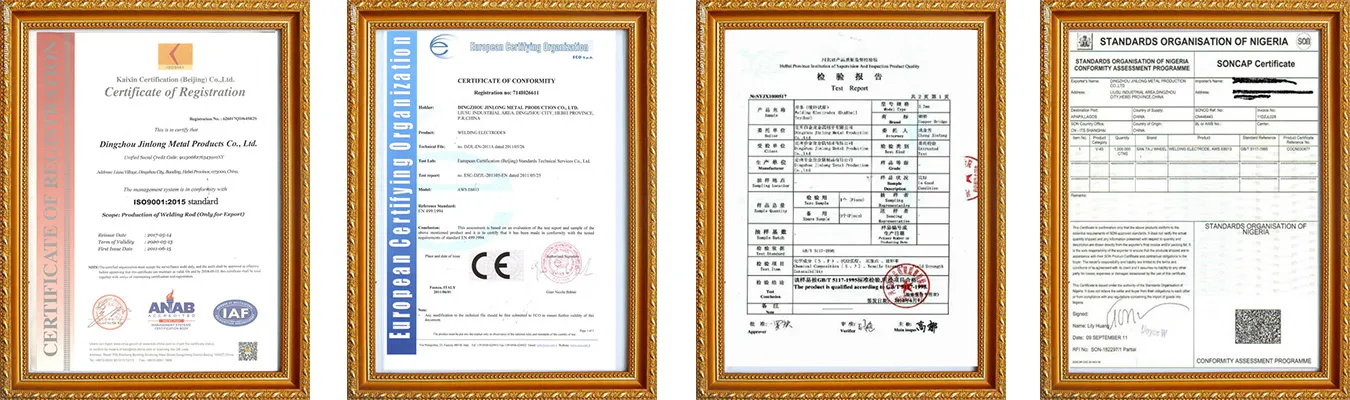
A deep dive into the technical composition of nickel rods reveals another layer of their appeal. The nickel alloy filler rods typically contain about 55% nickel, combined with iron and other elements, which enhances their mechanical properties and corrosion resistance. For example, nickel-iron rods are widely recognized for their versatility and ease of use, making them suitable even for less experienced welders or those encountering complicated repair jobs.
From an expert perspective, preparation is critical when using nickel rods with cast iron. The joint area must be meticulously cleaned to remove any contaminants, as impurities can affect the quality and durability of the weld. Pre-heating of the cast iron is often recommended to minimize thermal shock and reduce the risk of cracking, while post-weld cooling should be controlled and gradual. These steps all contribute to achieving a superior weld.
nickel rod for cast iron
In terms of market availability, nickel rods are easily accessible through various suppliers, catering to both large-scale industrial applications and small workshops. Their popularity ensures a steady availability and a range of options, allowing professionals to select the specific type and size suitable for their particular application. Choosing high-quality nickel rods from reputable manufacturers is essential to ensure excellent performance and safety.
The eco-friendly aspect of nickel rods also deserves attention. With increasing global emphasis on sustainability, nickel's recyclability makes it an appealing choice. Unlike some other materials, nickel can be effectively recycled without significant loss of quality, thus contributing to reduced resource consumption and environmental impact.
Ultimately, using nickel rods for cast iron is a practice grounded in expertise and trusted by professionals across numerous industries. The seamless blending of physical properties, practicality, and sustainable features positions nickel rods as a leading choice for achieving robust, enduring, and superior-quality welds on cast iron.
The authoritative voice of countless experienced welders and engineers attests to the indispensable nature of nickel rods in the domain of welding cast iron. Collectively, their experiences affirm not just the technical superiority of nickel rods but also their inherent value in ensuring both the reliability and longevity of critical components crafted from this challenging material.