Selecting the right welding rod is critical for ensuring seamless and durable connections when working with various metals. Specifically, when transitioning from mild steel (MS) to stainless steel (SS), the choice of welding rod can significantly impact the quality of the weld. Here, we delve into what makes a particular welding rod suitable for joining MS to SS, ensuring an optimal outcome with each project.
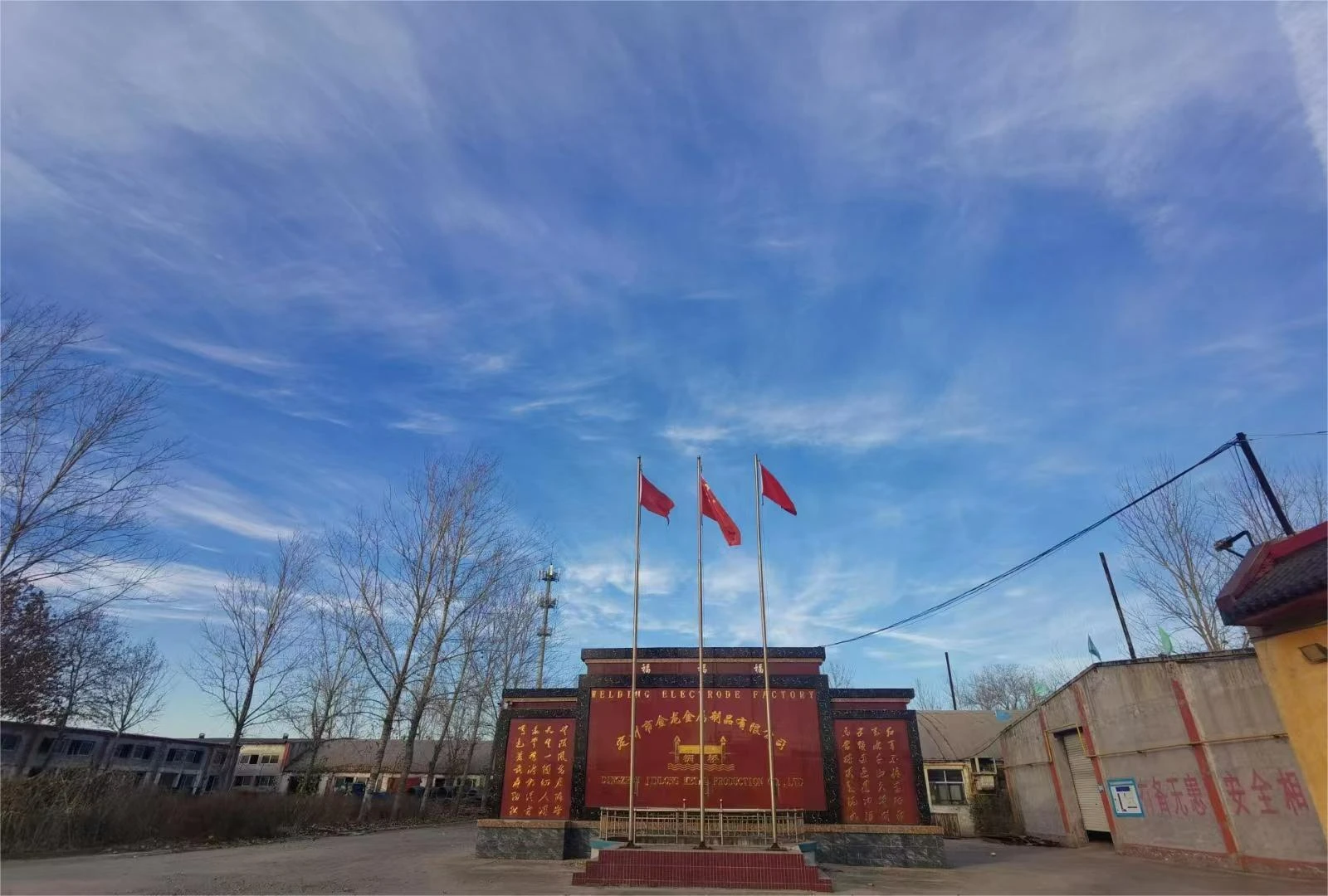
Welding from mild steel to stainless steel poses unique challenges due to the inherent differences in the properties of these metals. Mild steel, an iron-based alloy, is softer and more malleable, making it easier to weld. In contrast, stainless steel has a higher chromium content, offering superior corrosion resistance, but also requires more careful handling during the welding process due to its tendency to warp and crack under certain conditions.
The selection of the appropriate welding rod involves understanding not only the chemical properties of the metals but also the intended application of the finished product. A common choice for this type of welding is the use of an austenitic stainless steel rod, generally recommended due to its excellent compatibility with both MS and SS.
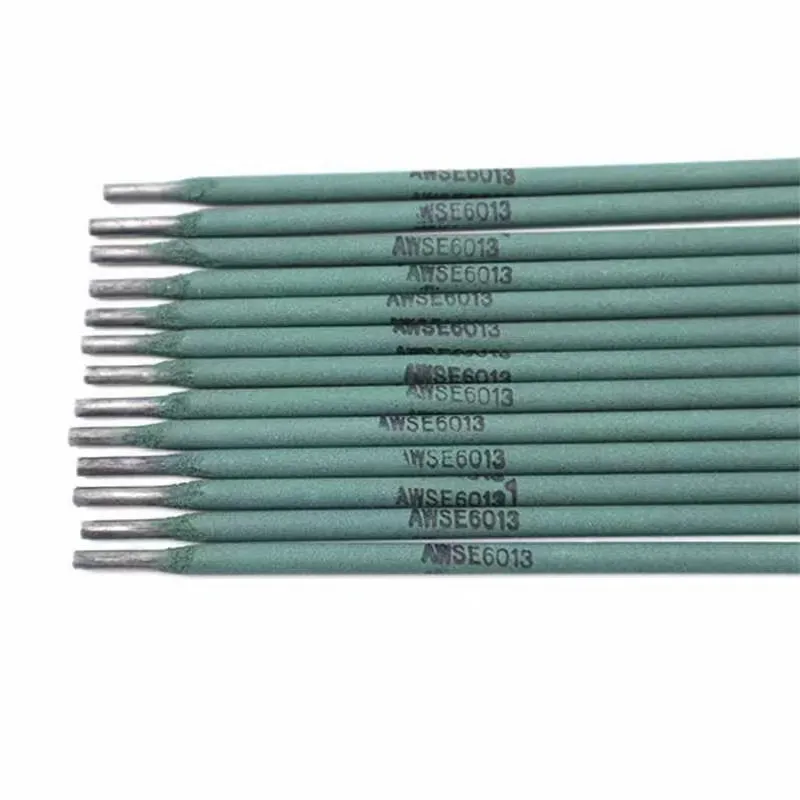
Among the various options,
the 309L welding rod stands out for its versatility and effectiveness. This rod is specifically designed for dissimilar metal welding, offering a stable arc and producing a weld deposit with high strength and good ductility. The 309L's reduced carbon content minimizes carbide precipitation, thereby reducing the risk of intergranular corrosion in the heat-affected zone (HAZ), which is particularly crucial when welding stainless steels.
Another worthy alternative is the 312 welding rod, renowned for its high tensile strength and excellent crack resistance. This rod is particularly advantageous in high-stress applications or environments where the mechanical properties of the weld must withstand significant challenges. However, the 312 rod may not always provide the best cosmetic finish, which is a consideration for projects where the visual appearance of the weld is critical.
ms to ss welding rod number
To maximize the effectiveness of these rods, proper preparation and technique are essential. First, ensure both metal pieces are meticulously cleaned, as contaminants can significantly affect the quality of the weld. Align the pieces carefully to promote even heat distribution and minimize warping. During the welding process, maintaining a consistent travel speed and arc length helps prevent defects such as porosity or excessive spatter.
Post-weld treatment is equally important in maintaining the integrity of the joint. Stress relieving the weld area through controlled cooling minimizes distortion and residual stresses, thereby prolonging the life of the weld. In applications where the weldment will be exposed to corrosive environments, additional measures such as pickling and passivating may further enhance the corrosion resistance of the joint.
Furthermore, operator skill and experience cannot be overstated. Welding from MS to SS requires a nuanced understanding of how different materials react to heat and pressure. Investing in regular training and certification for welders not only boosts the quality of the work but also reinforces the client's confidence in the durability and reliability of the product.
For projects where the mechanical and aesthetic requirements demand the highest standards, consulting with metallurgists or welding engineers can provide invaluable insights. Their expertise can offer tailored recommendations based on the specific use case, taking into account factors such as load-bearing requirements, environmental exposure, and lifecycle expectations.
In conclusion, successful welding from mild steel to stainless steel hinges on the careful selection of the correct welding rod, coupled with meticulous preparation and skilled execution. Whether the goal is structural integrity, aesthetic appeal, or both, understanding the characteristics of welding rods like the 309L and 312, and applying them skillfully, can make the difference between a serviceable joint and one that stands the test of time.