Utilizing ms to ci welding rods offers a unique opportunity for industries that require reliable bonding between mild steel and cast iron materials. These welding rods represent a particular niche in the welding domain, providing solutions to challenges posed by the distinct technical properties of these metals.
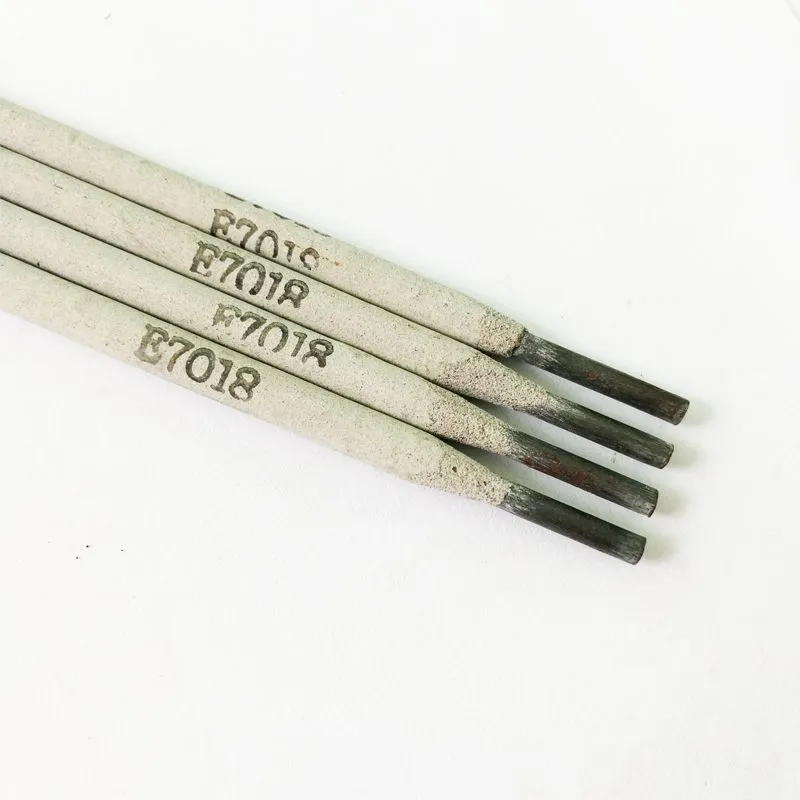
Professionals in the welding community understand that joining mild steel to cast iron requires a deep understanding of both materials involved. Cast iron, with its high carbon content and brittle nature, poses a significant bonding challenge. When combined with mild steel, a metal known for its malleability and lower carbon content, the contrasting metallurgical properties demand a welding rod designed specifically to handle these differences.
Ms to ci welding rods, in essence, are engineered to deliver high-performance bonding by balancing the need for penetration in the mild steel with controlled heat input essential for cast iron. Too much heat on cast iron can lead to cracks, and inadequate penetration on mild steel can result in weak joints. Therefore,
the selection of the right welding rod is crucial.
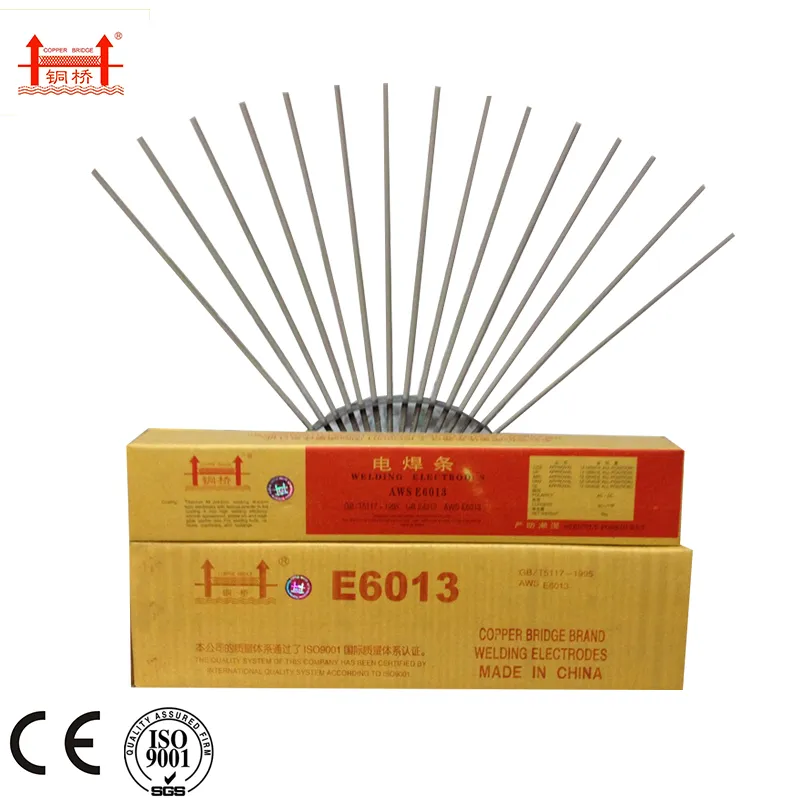
The expertise surrounding the use of these welding rods demonstrates their importance across various heavy industries, including automotive manufacturing, machinery repair, and structural engineering. Through trials and established practice, expert welders have identified optimal practices which include preheating cast iron to around 200°C to 300°C before welding to minimize thermal stress. This preheat treatment reduces the risk of post-weld cracking, preserving the joint’s integrity. Following welding, a gradual cool-down is advised, often achieved through insulating materials like a welding blanket.
ms to ci welding rod
Authoritative insights into welding processes highlight the significance of controlling the welding environment. For instance, maintaining a stable arc and selecting appropriate current settings on the welder plays a pivotal role in achieving a successful joint. Most importantly, after welding, peening the weld beads can alleviate stresses in the weld, as it facilitates the dispersion of heat-affected zones. Such expert advice underscores the nuances in technique required and the critical thinking necessary for high-quality results when working with ms to ci welding rods.
Trust in these products rests not only on the science of metallurgy but also on field-tested reports and quality certifications from trusted manufacturers. When selecting welding rods from reputable sources, consider certifications such as ISO and AWS (American Welding Society) designation, which reflect compliance with international standards. Furthermore, obtaining welding rod recommendations directly from experienced engineers and technicians can add reliability, bridging the gap between theoretical knowledge and practical application.
Ultimately, utilizing ms to ci welding rods enhances operational efficiency and longevity in constructed products, providing strong structural connections that withstand operational stresses. This application is not only cost-effective by reducing material disposal due to failed welds but also instrumental in developing products that meet high structural performance expectations.
Continuous innovation in welding technology constantly fuels the development of enhanced ms to ci welding rods, aiming for ease of use and more efficient production processes. By remaining abreast of industry advancements and accumulating field experience, a welder's skill in handling these complex materials will only improve, driving forward precision and reliability in metal joining tasks. Therefore, in projects ranging from infrastructure reinforcement to the nuanced crafting of machine parts, these specialized rods are invaluable, underpinning the success of vital engineering and manufacturing endeavors.