Welding between cast iron and mild steel (MS) can be a challenging task often encountered in various industrial applications. The complexities arise due to the differing metallurgical properties of the two metals, which can lead to issues such as cracking and improper bonding if not handled correctly. By selecting the right welding rod and techniques, these challenges can be mitigated effectively.
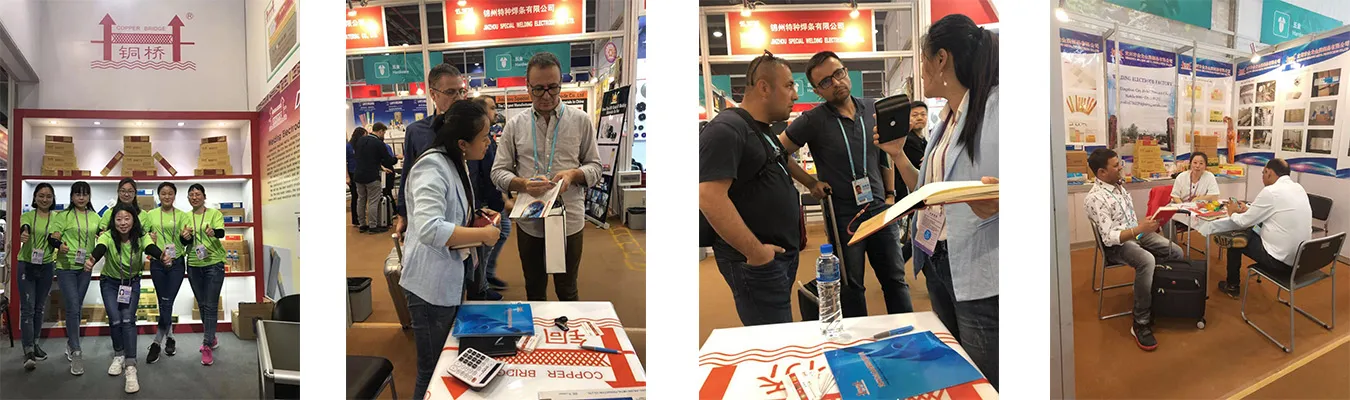
When considering weldability between cast iron and mild steel, the foremost concern is the difference in carbon content. Cast iron contains a higher percentage of carbon compared to mild steel, which could lead to incompatibility during welding. Selecting a nickel-based welding rod is vital as it accommodates the substantial differences in composition. Nickel rods, such as the popular ENiFe-CI, provide flexibility with thermal expansion and superior strength, ensuring a reliable and durable weld.
Expert welders emphasize the importance of preheating the cast iron prior to welding. This technique is crucial as it helps in reducing the thermal shock experienced by cast iron during the welding process. Preheating should be performed at a temperature range of 250°F to 500°F (121°C to 260°C), thereby aiding in avoiding cracks and enhancing ductility. Prompt post-weld cooling further stabilizes the weld area, combining with slow cooling under insulating materials to prevent potential stress.
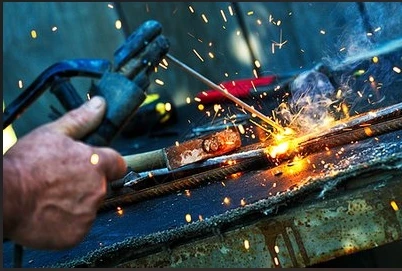
Industries that operate machinery and equipment faced with frequent repairs benefit significantly from the use of cast iron to mild steel welding rods. Using these specialized rods allows industries to manage repair downtimes effectively, extending the lifespan of machinery. For instance, machinery parts subjected to wear, such as gears or machine beds, frequently require welding repairs instead of complete replacements. Employing a nickel-based welding rod ensures robust performance even under repetitive stress.
In automotive applications, the necessity for hybrid repairs involving cast iron and mild steel is not uncommon. Engine blocks, often made of cast iron, require welding with mild steel components during modifications or repairs. Here, the nickel rods' adaptable nature minimizes problems associated with thermal cycling and vibration, which are routine in automotive environments. This adaptability not only improves the immediate quality of the repair but also increases long-term reliability.
cast iron to ms welding rod
Instrumental to the success of cast iron to mild steel welding is the skill level of the welder. A highly skilled welder will be equipped with in-depth knowledge of material sciences, particularly the behavior of carbon-rich metals under high temperatures. Expertise in selecting the right rod, applying preheating techniques, executing the weld, and, importantly, managing post-weld treatment is essential. These skills underpin a welder's ability to deliver quality results routinely.
Beyond practical execution, authoritative sources strongly advocate for ongoing training and certification for welders working with such specialized materials. Trusted institutions offer comprehensive courses tailored towards expanding knowledge of advanced welding techniques and equipment proficiency. These courses also cover health and safety standards, instilling best practices that contribute to project success and job site safety.
Over the years, research and development in welding technologies have also contributed to improvements in welding rods designed specifically for dissimilar metal joining. Modern welding rods now incorporate advanced metallurgy and composition techniques, yielding impressive results in strength and versatility. Recent advancements in flux technology further boost weld integrity, ensuring lesser impurities and smoother finishes on welded structures.
Overall, trust in professional recommendations combined with field expertise underscores the successful application of welding rods when joining cast iron to mild steel. Industries relying heavily on hybrid metal welding can maintain operational efficiency and enhance structural performance by prioritizing specialized equipment and skilled craftsmanship. As technology evolves, continuous learning and adaptation remain the keystones for advancing weld quality and reliability, satisfying both user expectations and structural demands.