The use of carbon steel to stainless steel welding electrodes is often seen in various industrial settings ranging from construction to automotive manufacturing. Ensuring high-quality welding across different metal types requires adept expertise and knowledge. Carbon and stainless steel, both widely used metals, have unique properties and present unique challenges when it comes to welding. Choosing the right electrode for these tasks is vital for optimal results and maintaining the structural integrity of the welded sections.
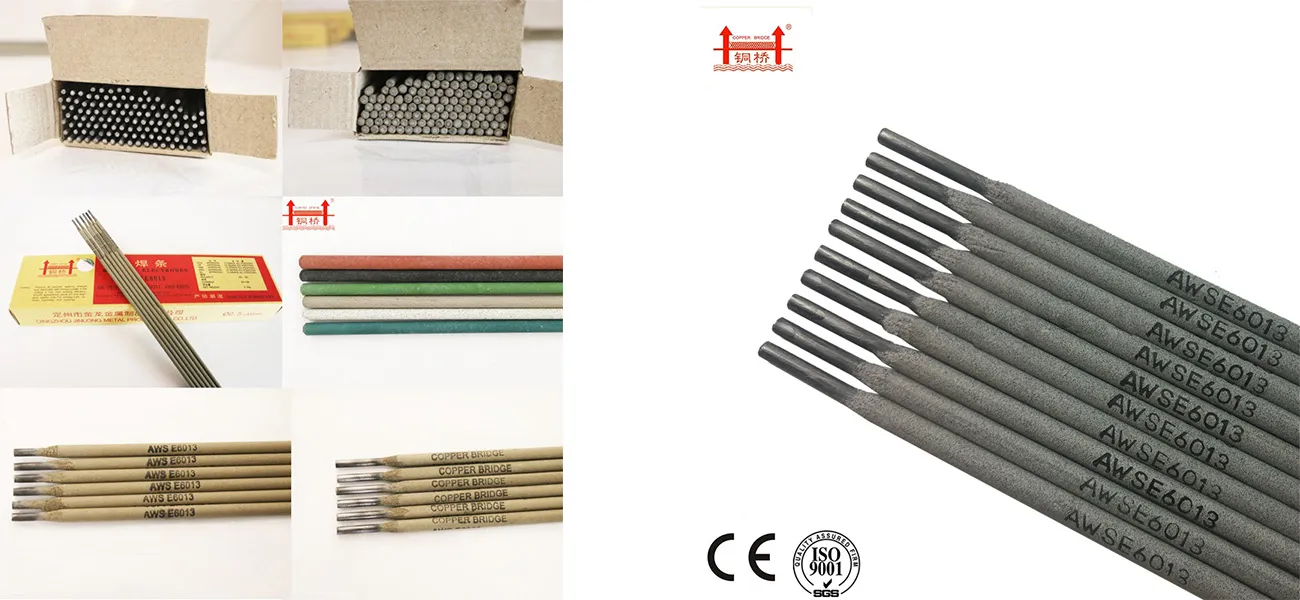
An essential aspect of welding carbon steel to stainless steel involves understanding the differences in their metallurgical properties. Carbon steel, known for its strength and malleability, differs from stainless steel which is valued for its corrosion resistance and aesthetic appeal. Stainless steel contains chromium, which provides a protective layer against oxidation, a factor that does not typically affect carbon steel to the same extent. Welding these two materials requires specific consideration to maintain the corrosion resistance of stainless steel while ensuring strong joint formation.
In practice, the welding electrode selected plays a pivotal role in the welding process. Typically,
an austenitic stainless steel electrode, such as the E309 or E309L, is recommended. These electrodes are favored for their ability to accommodate the thermal expansion coefficients and mitigate the issues of intergranular corrosion, a common problem when dissimilar metals are welded. E309L, for example, contains lower carbon content, reducing the risk of carbide precipitation and maintaining the corrosion resistance of the welded joint, a critical factor in ensuring longevity and durability.
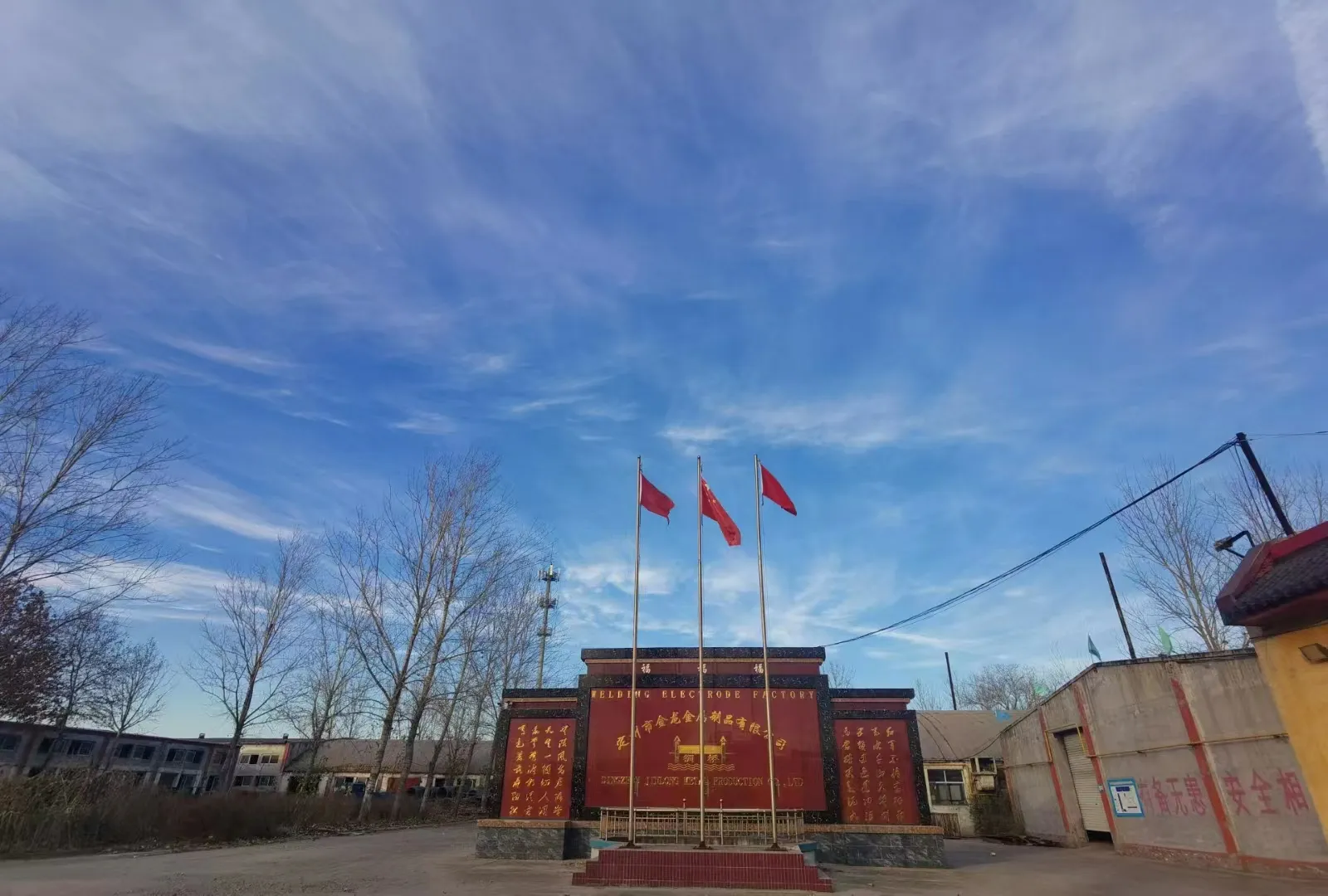
Moreover, the procedural expertise required during the actual welding process is not to be underestimated. Proper pre-weld and post-weld heat treatment are essential to prevent thermal stress and distortion. Employing a methodical approach in both planning and executing the weld ensures that the integrity of the weld is maintained. Skilled welders often employ techniques such as controlled cooling and minimal heat input to balance the composition differences at the junction. Adjusting the angle, speed, and sequence of the welding passes helps distribute heat more evenly and prevents common pitfalls like cracking or excessive brittleness in the joint.
carbon steel to stainless steel welding electrode
Experience shows that maintaining clean metal surfaces is critical before the commencement of welding. The presence of contaminants like oil, grease, or rust can significantly affect the quality of the weld and compromise its strength. Cleaning the surfaces with appropriate solvents and grinding tools can drastically reduce such risks. Experienced welders understand the importance of using clean and properly prepared electrodes to achieve seamless, high-quality welds.
The authority on welding practices, such as the American Welding Society (AWS), provides guidelines and recommendations that enhance the trustworthiness of the process and results. Adhering to industry standards not only ensures the safety and reliability of the welds but also serves to validate the competence of the welding professional involved.
In crafting an authoritative resource for carbon steel to stainless steel welding, expert recommendations, real-world experience, and adherence to standardized practices collectively offer a wealth of knowledge that can maximize the quality and effectiveness of the welding process. This ensures that each weld performed is not only strong and durable but also resistant to environmental factors that commonly degrade non-homogeneous metal joints over time.