The world of welding is vast and complex, offering a myriad of tools and consumables that cater to specific types of jobs and materials. Among these, the choice of welding rod significantly influences the quality and durability of the weld. The 60 13 welding rod holds a notable position in this field, revered for its ease of use and versatility across different welding scenarios.
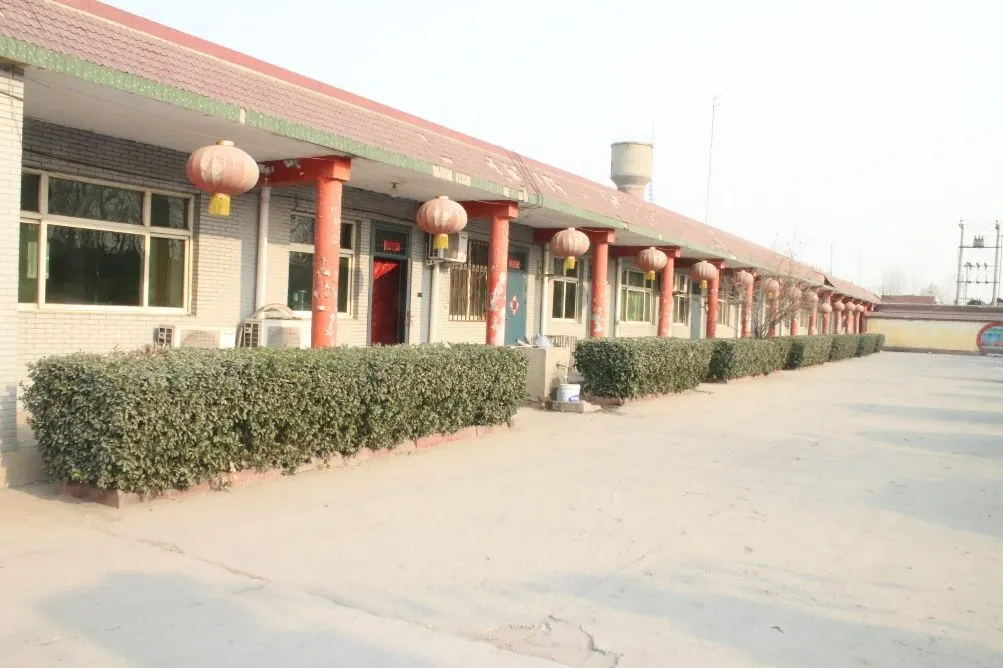
A 60 13 welding rod is an excellent choice for those requiring a balance between strength and adaptability. It is primarily known for its tensile strength rating of 60,000 PSI. This aspect is crucial when working on medium-strength steel structures, where stability and resilience are paramount. The 60 13 has been the go-to electrode for general purpose welding due to its impressive performance in various postures, including flat, vertical, and overhead applications. Its ability to provide smooth and stable arcs makes it a favorite for both seasoned welders and novices.
From a professional standpoint, the 60 13 rod’s coating is a major factor behind its popularity. The thick, iron powder coating not only protects the core wire but also contributes to a smoother welding operation by enhancing the stabilization of the arc. This feature minimizes spatter, a common challenge faced during welding, ensuring a cleaner work area and reducing the need for excessive cleanup. Furthermore, the slag removal process is relatively straightforward with 60 13 rods, facilitating a faster and more efficient workflow in rigorous environments.
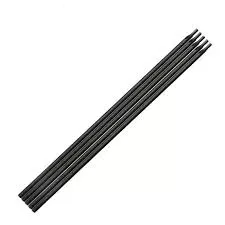
In real-world applications, the choice of a 60 13 welding rod manifests as a strategic decision in many industrial settings. Its utility extends across construction, automotive repair, and maintenance operations, where robust welds are necessary to withstand dynamic loads and stresses.
Professional welders often report the efficacy of 60 13 rods when dealing with rusty or dirty metals. This cutting-edge adaptability is credited to the flux composition, which provides a level of tolerance for less-than-perfect surfaces, thus saving time on pre-weld preparation.
60 13 welding rod
The versatility of the 60 13 rod is further highlighted by its compatibility with both AC and DC currents, allowing welders to adapt to different power supplies and field conditions. This flexibility is particularly beneficial in remote areas where power sources might be variable or unreliable.
The expertise surrounding the use of 60 13 rods is backed by industry standards and certifications which assert the rod’s quality and applicability in a variety of contexts. Brands producing 60 13 rods often undergo rigorous testing and adhere to international welding standards, giving professionals the confidence they need when selecting this electrode for critical weld joints.
Trustworthiness in utilizing the 60 13 welding rod also comes from the extensive documentation and community discussion available in welding forums and technical sheets. Welders sharing their firsthand experiences provide valuable insights into optimal settings, maintenance, and troubleshooting tips that enhance rod performance. This pool of shared knowledge is invaluable for maintaining high standards of safety and quality, effectively turning each welding experience into a learning opportunity.
In summary, the 60 13 welding rod exemplifies a product that embodies experience, expertise, authoritativeness, and trustworthiness within the welding industry. Its balanced characteristics, combined with the assurance of rigorous manufacturing standards, make it an indispensable asset for modeling effective and efficient welding practices across diverse applications. Whether restoring a classic car or undertaking complex infrastructure projects, the 60 13 rod stands as a testament to quality and reliability, ensuring that each weld job is executed to the highest standards of craftsmanship.