For welders and enthusiasts diving into the world of electric arc welding, the 1/8 6011 welding rod stands as a staple in many projects due to its versatility and excellent performance on dirty or rusty surfaces. Understanding the right amperage settings is essential for maximizing its potential while ensuring safety and precision.
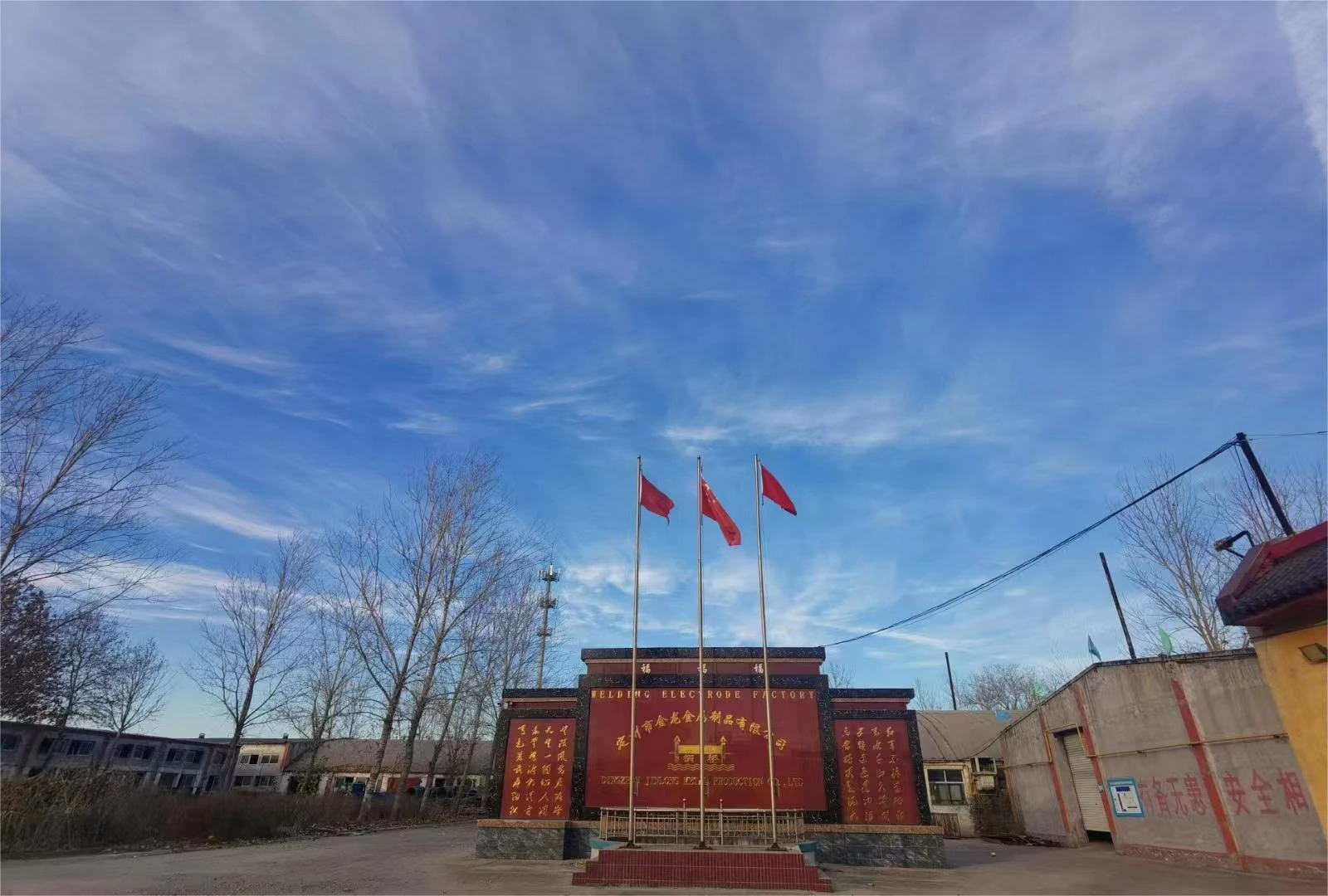
The 6011 welding rod is known for its ability to create deep penetration and is particularly favored for jobs requiring significant penetration, working on unclean metal surfaces, or in scenarios necessitating fast follow-up passes. When using a 1/8 inch (approximately 3.2 mm) 6011 electrode, one of the primary considerations should be the appropriate amperage range, which significantly influences the quality and outcome of the weld.
The recommended amperage range for a 1/8 inch 6011 welding rod typically falls between 75 to 125 amps.
When selecting the perfect amperage, several factors must be assessed
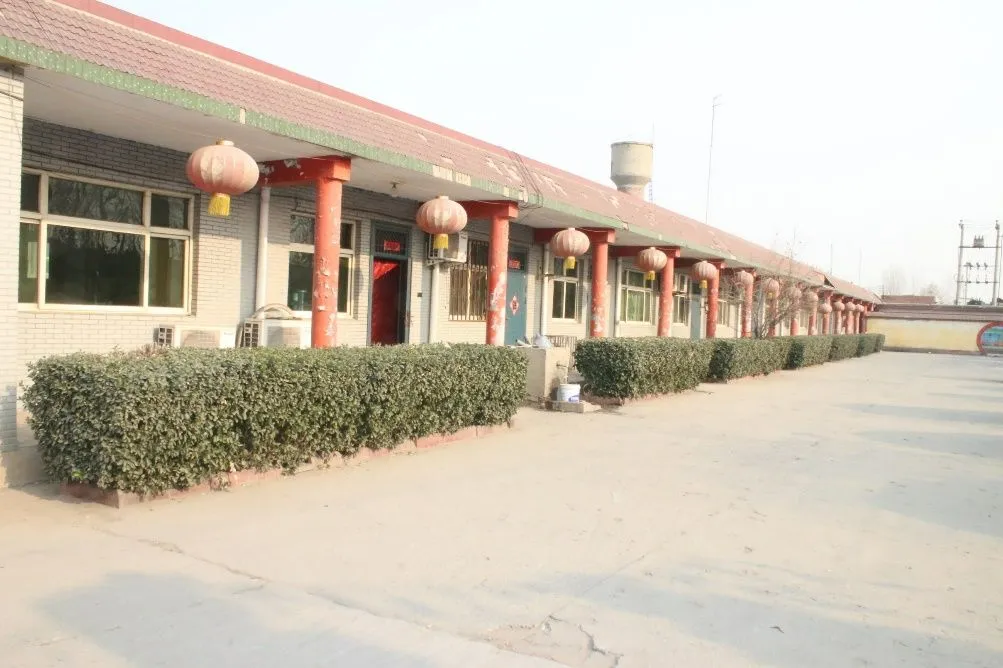
1. Material Thickness and Type Thick materials require higher amperages, while thinner metals do well with lower settings. The 6011's flexible amperage range allows it to adapt to varying material thicknesses, ensuring proper penetration without over-burning the metal.
2. Position and Technique Welding position (flat, vertical, overhead, or horizontal) can affect amperage choice. For example, vertical and overhead positions typically call for slightly lower amperage to prevent the weld pool from dripping. Similarly, welder’s technique, whether they employ drag or whip methods, can influence amperage needs.
3. Power Source Characteristics Compatibility with AC or DC power sources makes the 6011 versatile. However, alternating current (AC) scenarios might prefer higher amperage due to the natural fluctuations of current that can affect arc stability.
1 8 6011 welding rod amperage
4. Joint Design The joint type, whether it's butt, lap, or corner, can necessitate adjustments in amperage. Comprehensive understanding of joint designs empowers welders to decide the apt settings that promise integrity and strength.
Experienced welders underline the importance of test runs to fine-tune the amperage setting for specific applications. Variability in job requirements or equipment could slightly shift the ideal amperage needed. Therefore, professional welders always advise conducting a sample weld to review the bead's quality and adjust accordingly.
Moreover, the arc characteristics of the 6011 rod play an essential role in its performance. This electrode is esteemed for its forceful arc, which can tackle contaminations like rust, oil, or paint. However, without suitable amperage settings, this same forceful arc might lead to undercutting or spatter, underscoring the necessity of appropriate power adjustments.
In practice, achieving an effective weld with a 1/8 6011 electrode also hinges on the interplay of several factors beyond amperage. For example, maintaining a consistent travel speed and appropriate electrode manipulation technique, such as using slight side-to-side motions, can promote a stronger weld. Additionally, electrode angle management is crucial — holding it at approximately 15 to 30 degrees from vertical fosters stability and helps in directing the molten pool.
Safety, while not directly linked to amperage, remains an indelible part of welding. Ensuring the use of personal protective equipment like gloves, helmets, and aprons is non-negotiable, particularly when working with materials that demand the 6011’s robust penetration capabilities. Furthermore, proper ventilation in the workspace safeguards against exposure to harmful fumes.
In conclusion, mastering the use of a 1/8 6011 welding rod demands an understanding of its amperage requirements in conjunction with material specifics and welding conditions. Catering the amperage setting between 75 and 125 amps to match material needs, adjusting for positional demands, and ensuring robust joint design all contribute to weld quality and strength. For seasoned welders, each project becomes a unique opportunity to apply their expertise, optimize settings, and produce work characterized by precision and durability.