Choosing the right welding rod is crucial when dealing with cast iron, a material known for its brittleness and unique composition. Unlike steel, cast iron contains a higher carbon content, leading to considerable challenges during welding procedures. To tackle these challenges, understanding the category of cast iron you are working with and selecting appropriate materials are essential steps in ensuring a successful weld.
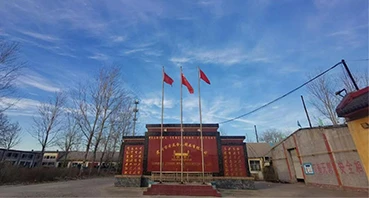
In the diverse world of metals, cast iron stands out due to its versatile applications in elements such as engine blocks, pipes, and various components in machinery. Its outstanding compression strength complements its use in areas where durability is key. However, its brittleness and tendency to crack make welding a delicate task, necessitating specialized knowledge and experience.
The first step in selecting the right welding rod is identifying the type of cast iron in question. Gray cast iron is the most common variant, recognizable by its ease of machinability and good resistance to wear. White cast iron, on the other hand, is much harder and more rigid, posing significant challenges during welding. Lastly, ductile cast iron, also known as nodular cast iron, offers improved flexibility due to its unique microstructure, a modification achieved by adding small amounts of magnesium.
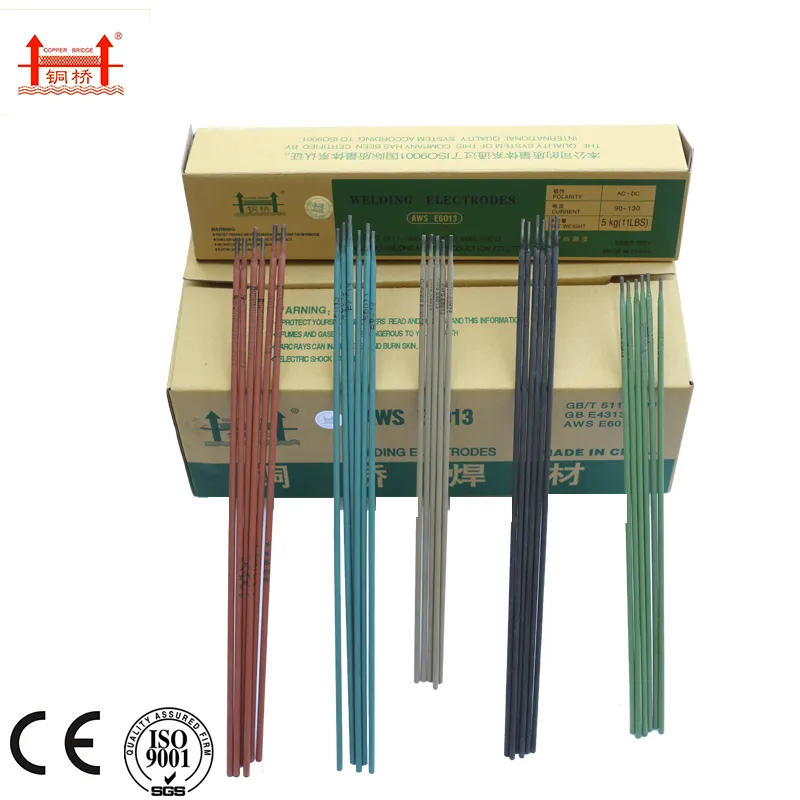
Having identified the type of cast iron, the next crucial consideration involves the welding electrodes themselves. Enabling a satisfactory weld requires electrodes that adequately minimize the risk of cracking while effectively fusing the joint.
Nickel-based electrodes often serve as the gold standard when welding cast iron. Their versatility and ability to accommodate the inherent expansion and contraction of cast iron make them a top choice. Pure nickel rods, including ENi-CI rods, provide a soft, malleable weld material that is compatible with all sorts of cast iron. They allow for stress relief, thus reducing the likelihood of cracking, which is particularly valuable when dealing with high-stress applications.
Nickel-iron alloys emerge as another viable alternative, especially useful for repairs on heavy, thick sections. ENiFe-CI rods, which consist of a composition richer in iron than pure nickel variants, offer superior welding strength, aiding in the restoration of substantial components like engine blocks. This variety excels in its ability to match the expansion characteristics of the cast iron better than their purely nickel counterparts.
what welding rod to use for cast iron
For those working under tighter budgets, steel electrodes with a specialized coating can offer a compromise. Appropriately selected steel rods, such as ESt, allow practitioners to manage repairs economically. However, these electrodes trade off some degree of malleability and require precision to mitigate increased risks of cracking.
Preheating the casting before welding plays a pivotal role across all electrode choices. By gradually elevating the temperature, usually between 400°F and 600°F, the risk of thermal shock—leading to immediate crack formation—diminishes significantly. Controlled cooling post-welding stabilizes the welded joint, reducing residual stress.
Expert welders also emphasize peening between passes. This mechanical process compresses the weld material subtly as it cools, deterring the manifestation of tension-related cracks within the brittle base metal. Equally important is selecting a suitable welding technique—such as stick welding or TIG—according to both project requirements and material handling specifics.
Finally, an often-overlooked facet involves the clean preparation of cast iron surfaces before commencing the weld. Completely eradicating oil, grease, paint, and impurities ensures that the weld material coalesces soundly with the cast substrate.
In concluding, welding cast iron necessitates more than technical know-how; it requires a cultivated finesse and respect for the material’s intrinsic qualities. Assembling a nuanced approach dovetailed with a choice of specialized electrodes tailored to specific cast iron types can significantly mitigate issues such as cracking, resulting in a structurally sound repair or modification. Leveraging expert insight and practical experience, welders can transform what is traditionally perceived as a daunting task into an achievable feat of engineering. Such informed practices not only extend the lifespan of cast iron components but also enhance the structural integrity of critical assemblies across industries.