Welding cast iron can be challenging due to its unique properties, making the choice of welding rod crucial for achieving optimal results. Cast iron, known for its brittleness and high carbon content, demands specific techniques and materials that ensure durability and integrity. Understanding the right welding rod for cast iron not only enhances the quality of the weld but also maintains the metallurgical stability of the entire piece.
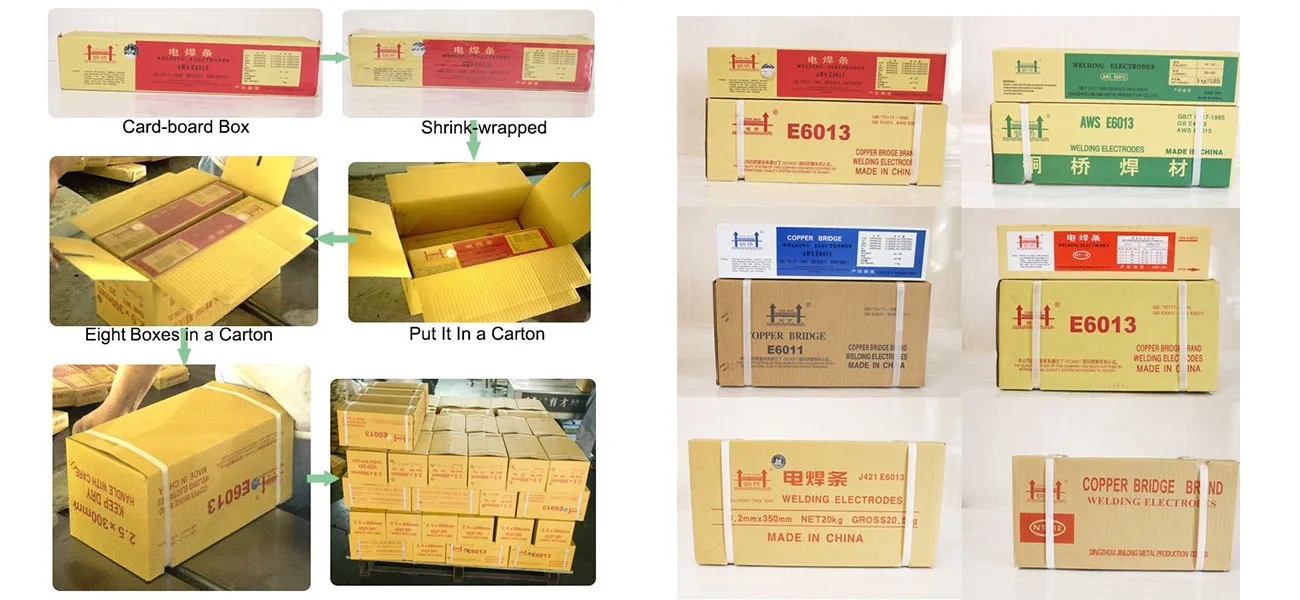
The predominant choice for welding cast iron is nickel-based rods, with two primary types often recommended ENi-CI (Nickel 99) and ENiFe-CI (Nickel 55). These rods are lauded for their ability to handle the peculiarities of cast iron, including its thermal expansion and contraction during the welding process.
Nickel 99 rods are composed almost entirely of pure nickel. They are ideal for applications where the weld must match the color and texture of the base material closely. This type of rod is particularly beneficial when working on projects that require high malleability after welding. Due to their low melting point relative to cast iron, Nickel 99 rods can minimize the risk of cracks, an essential consideration when welding delicate structures or thin cast iron sections.
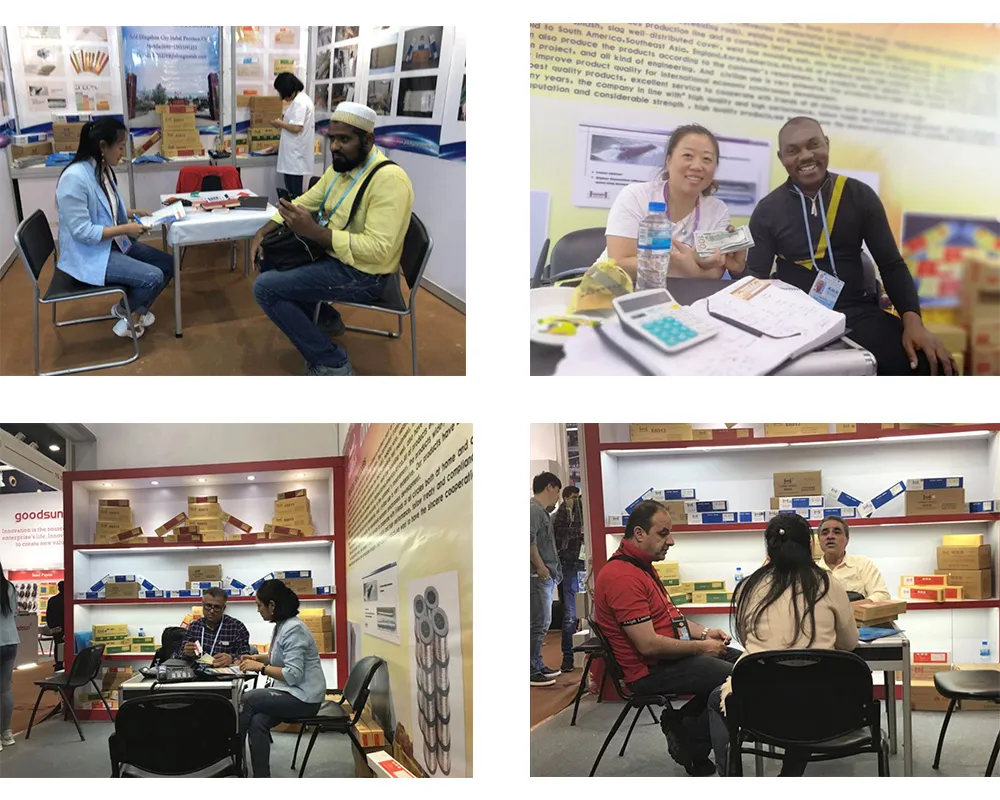
Contrastingly, Nickel 55 rods contain approximately 55% nickel and offer a balance between weld strength and elongation properties. While they may not be as machinable as the Nickel 99 rods, they provide a more robust bond. This characteristic makes them suitable for welds subjected to stress or tension, as the resulting joint is stronger and better able to withstand mechanical loads. Nickel 55 rods are often recommended for thick cast iron pieces or when the weld will undergo machining after the process.
For projects that aim to minimize costs or for applications where precision is less critical, stainless steel rods, such as the 309 or 312 grades, can offer a practical alternative. These rods are typically less expensive than nickel-based rods and deliver satisfactory results in certain situations. However, they do have some limitations in terms of color mismatch and potential difficulties in machining post-weld areas.
what welding rod is used for cast iron
Pre-heating the cast iron before welding is essential regardless of the chosen welding rod. The pre-heating process helps to reduce the thermal gradient between the weld and the base material, significantly reducing the risk of stress-induced cracks. Maintaining a uniform temperature across the entire piece can dramatically affect the eventual quality of the weld and the longevity of the structure being repaired or fabricated.
Post-weld cooling should be controlled and gradual, allowing the material to dissipate heat slowly and uniformly. This step is as crucial as pre-heating since abrupt changes in temperature can lead to stress fractures. Techniques such as wrapping the welded piece in insulating materials like sand or lime can aid in regulating the cooling rate.
The selection of the welding rod must consider not only the technical requirements of the application but also the intended use of the final product. For heritage restoration projects or antique repairs, the aesthetic outcome of the weld is often as important as its structural integrity. On the other hand, industrial applications may prioritize strength and resistance over appearance.
Professionals dealing with cast iron welding emphasize the importance of expertise and experience in achieving successful outcomes. Skilled welders understand the subtleties involved in working with cast iron, including the precise control of heat input and the considered selection of welding rods. Trust in quality materials and techniques cannot be understated, as the stakes are often high when dealing with expensive components or critical infrastructure.
As a testament to their effectiveness, the choice and application of the correct welding rod reflect an authoritative understanding of metallurgical principles specific to cast iron. Investing time and resources into the appropriate procedures not only ensures the integrity and longevity of repairs and fabrications but also reinforces the trust clients and industries place in such specialized welding services.