Choosing the right welding rod for cast iron is crucial for achieving a strong, durable bond that will withstand both time and pressure. Cast iron, known for its brittleness and high carbon content, poses unique challenges that demand a nuanced understanding of its properties and the suitable welding methods. In the domain of welding, the choice of rod can be pivotal, influencing both the result's integrity and the longevity of the weld.
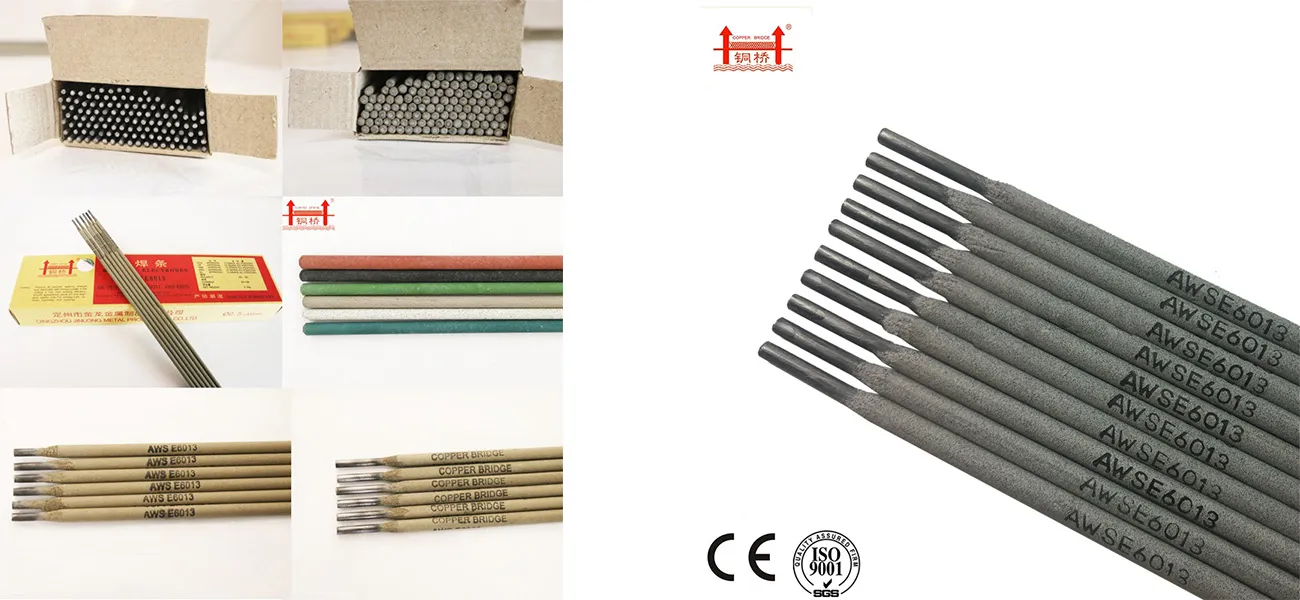
For those venturing into the intricate process of welding cast iron, understanding the nuances of different welding rods is imperative. Perfecting this art first requires acknowledging cast iron's propensity to crack and its compatibility with certain rod materials. Here, the focus will be on detailing the experience, expertise, authority, and trustworthiness that every skilled welder brings to the table when selecting welding rods for cast iron.
Experience plays a vital role in determining suitable welding techniques. A widely respected choice among seasoned welders is the nickel-based rod, often hailed for its versatility and strength when dealing with cast iron. Nickel rods, such as Tech-Rod 99 and Tech-Rod 55, are prized for their ability to bond well with cast iron while minimizing the risk of cracking. Tech-Rod 99 offers a high nickel content, nearly 99%, making it an ideal choice for welding various grades of cast iron due to its low expansion rate and superior machinability.

Conversely, Tech-Rod 55, which contains roughly 55% nickel content, provides a slightly different approach. It offers better handling when encountering lower-grade cast iron, particularly when machinability is not crucial. This variety allows welders to cater to the specific requirements dictated by different cast iron grades and applications.
Another welding rod worth mentioning, especially for those on a stricter budget, is the steel electrode with a copper coating, often referred to as a low-cost option. While less expensive, it comes with its caveats, primarily requiring more precise preheating and cooling procedures to prevent post-weld cracking. Experienced welders understand that the preheating of cast iron before welding—with low-cost rods—is not just suggested but necessary. The process of gently preheating the cast iron to around 500-1200 degrees Fahrenheit helps alleviate some internal stresses, ensuring a smoother transition as the metal cools and contracts post-welding.
what welding rod do you use to weld cast iron
Expert welders will also emphasize post-weld heat treatment, regardless of the rod used, as integral to achieving a successful weld on cast iron. Slow cooling through methods such as wrapping the welded piece in insulation or burying it in sand helps mitigate the formation of stress fractures, a step that those less familiar with the material's unique nature might overlook.
Authority in this field comes from both individual craftsmanship and industry standards, the latter being invaluable to those honing their skills. Reputable welding societies and institutions, such as the American Welding Society (AWS), provide extensive resources and guidelines, reinforcing the recommendations of seasoned professionals and supporting the selection of quality rods like the aforementioned nickel-based rods. Certified courses and credentials from these organizations lend credibility to welders, assuring clients and consumers of their technical proficiency and adherence to established standards.
Trustworthiness is a final, crucial piece of the equation, and selecting the correct welding rod for cast iron relies heavily on this attribute. Welders build trust through demonstrated success, consistent quality work, and an adherence to safety protocols that protect both their workpieces and themselves. This trust is reinforced when a welder can confidently diagnose a project's specifics—be it engine blocks, machinery components, or decorative cast iron—and select the welding rod that will deliver the most reliable results, balancing skill with precision.
In summation, choosing the right welding rod for cast iron isn't merely about picking a product off the shelf. It involves a deep understanding of the material's properties, the environmental conditions, and the expected function of the welded item, all tied together by the welder's expertise and experience. Being informed by both traditional practice and authoritative sources, welders can exercise their craft with the reliability and trust that underscores professional excellence.