When it comes to welding cast iron, many variables need to be considered to achieve optimal results and avoid common issues such as cracking. One of the most crucial elements in this process is selecting the right electrode. Welding cast iron is notorious for its difficulty due to its high carbon content, which makes it prone to cracking. Therefore, understanding the nuances of electrode selection can vastly enhance welding outcomes, establishing expertise, and authority in the field.
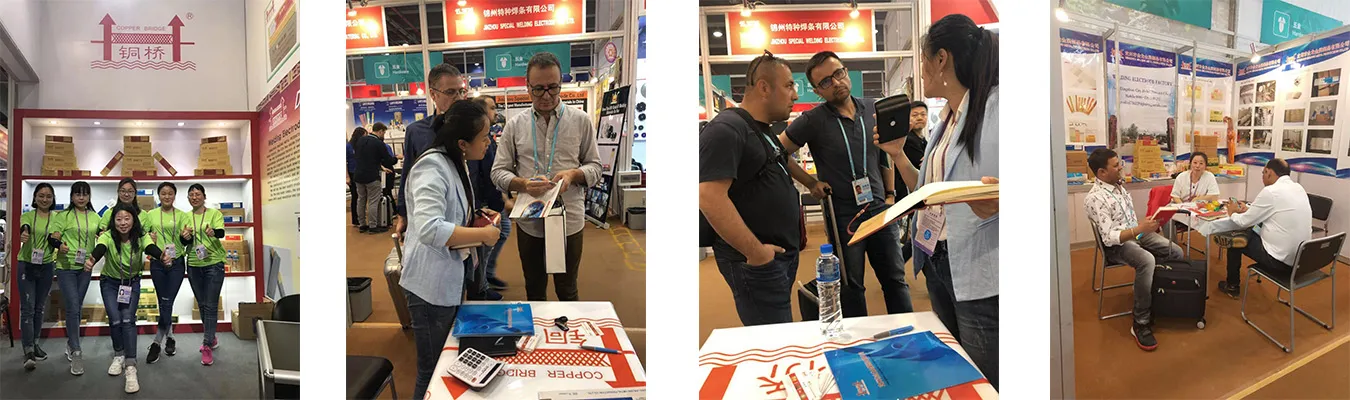
The most commonly recommended electrode for cast iron welding is the nickel alloy electrode. Nickel electrodes are divided into two primary categories pure nickel and nickel-iron (NiFe) electrodes. Pure nickel electrodes offer excellent machinability and are less likely to cause cracking. They are exceptionally good for older cast iron parts when color matching, strength, and machinability are desired. The Nickel-99 electrode, particularly, provides high quality and machinable welds and is often preferred for non-critical applications or thinner sections of cast iron.
Nickel-Iron electrodes, on the other hand, offer a stronger weld than pure nickel and are less expensive. An example of this is the Nickel-55 electrode, often selected for more substantial sections of cast iron or where strength is of significant concern. These electrodes still provide fairly good machinability, and their composition enables a balance between strength and cost-effectiveness.
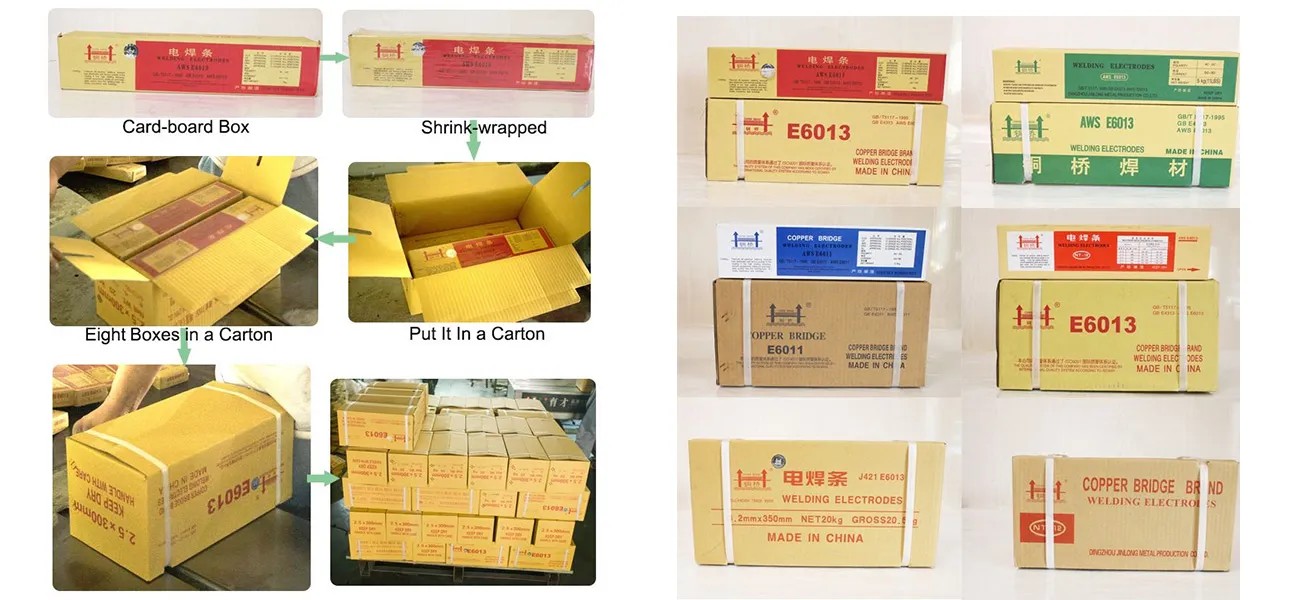
There are, however, scenarios where a steel electrode might be employed, especially if the cast iron part is non-machinable after welding. Steel electrodes provide the strongest weld but require pre- and post-weld heat treatments to reduce the risk of cracking and ensure weld integrity due to the increased hardness that results from the fusion between cast iron and steel.
In terms of real-world experience, selecting the appropriate electrode also depends on other factors like joint design, the casting's condition, and the need for post-weld machining. For instance, if you are welding a part that needs to withstand significant stress or involves thicker cast iron sections, opting for Nickel-55 or a specialized cast iron electrode such as Ferroweld can be advantageous. Ferroweld’s unique formulation is designed to minimize heat input and thus, reduce stress and cracking risk.
which electrode is used for cast iron welding
Another critical element is preheat and interpass temperature control. Ensuring the cast iron piece is preheated to the correct temperature (typically around 500-1200°F) and maintaining it during welding helps in minimizing thermal shock, reducing the risk of cracks. Slow cooling post-weld also reduces stress, making a controlled environment imperative.
Backing up these practices with specialized welding techniques such as peening (mechanically working the weld bead to relieve stress) and employing a slower, more controlled welding speed can significantly contribute to the success rate of welding cast iron.
Ensuring trustworthiness in electrode performance involves not just relying on the electrode's specification, but also on well-documented procedural adherence and welding tests. Consider conducting small-scale trials on test pieces before proceeding with actual parts, especially for high-value or critical components.
Engaging with expert practitioners, manufacturers, or even participating in forums dedicated to welding can further solidify one’s trust in their electrode selection and application processes. Collaborating with professionals can provide valuable insights into overcoming challenges, specific techniques, and equipment that further the efficiency of the welding process.
In conclusion, the prudent selection of welding electrodes for cast iron is a blend of scientific understanding and hands-on experience. Choosing nickel-based electrodes or specific ferrous alternatives based on the requirements ensures not only the physical integrity of the weld but also strategic resource allocation and cost-effectiveness in most welding operations. By mastering these elements, professionals can achieve superior results, uphold authoritative standards, and enhance trust within the domain of cast iron welding. The path to excellence in welding cast iron truly begins with informed and judicious electrode choice.